Inside Process: Industry 4.0, robotics and other automation technologies are helping Sohar Aluminium advance its competitiveness among aluminum smelting companies.
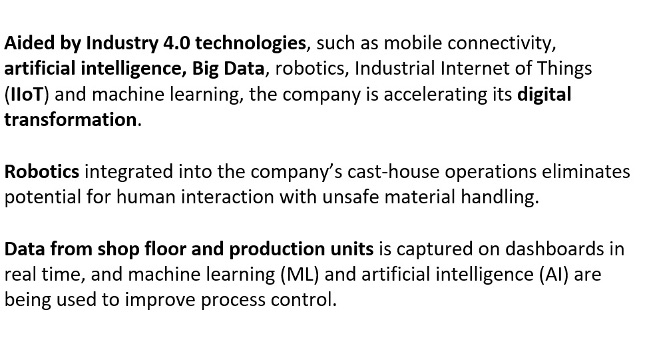
Use of leading-edge aluminum smelting technology with progressive increase in amperage, state-of-the-art production, efficiency and safety optimization tools and technological innovations has helped Sohar Aluminium advance. Automation, industrial communications, and other aspects of Industry 4.0 platform are being applied to help the company with the goal of becoming the benchmark smelter in the region. Aided by Industry 4.0 technologies, such as mobile connectivity, artificial intelligence (AI), Big Data, robotics, the Industrial Internet of Things (IIoT) and machine learning (ML), the company is accelerating its digital transformation.
Smelter of the future
Sohar Aluminium formed in September 2004 to undertake a greenfield aluminum smelter project in the Sultanate of Oman. Inaugurated in 2009, Sohar Aluminium is jointly owned by Oman Oil Company S.A.O.C., Abu Dhabi National Energy Company PJSC (TAQA) and Rio Tinto.
The information technology (IT) and automation team at Sohar Aluminium is using the technologies to advance operational excellence, the overarching goal since the company’s launch a decade ago.
“Sohar Aluminium has embraced some elements of Industry 4.0 ever since we came on stream, and we continue to evaluate new technologies and innovations as they materialize. This is a continuous journey of improvement which we don’t foresee an end to,” said Abdullah Al Maamari, IT manager, Sohar Aluminium. Robotics and other automation are among investments.
Robotics integrated into the company’s casthouse operations eliminates potential for human interaction with unsafe material handling, thereby reducing the risk of injury to its operators. Robotic cranes assist in the stacking of the refined metal bundles and applying labels to them.
Increasing networking
Increasing interconnections among machines, equipment, devices and physical objects is part of the strategy for advancing “Industrial IoT, which connects all of our systems with the enterprise,” said Ibrahim Al Maawali, automation superintendent. “All of the data from the shop floor and production units is captured on our dashboards in real time.” Additional IoT technologies are under evaluation.
Deployment of ML and AI are being used to improve process control at Sohar Aluminium by automatically recording, networking and using numerous machine and system parameters to better plan downtimes, increase productivity and drive quality.
ML has been implemented in existing processes, said Paul Ridgway, automation specialist at Sohar Aluminium. “Machine learning has been around for quite some time” inside intelligent systems and is being used “in some of our processes to better formulate our set points” and improve other areas, he said.
Data analytics
Data analytics is also being used to enhance maintenance and operational processes at Sohar Aluminium. Ibrahim said, “We use our historical data to forecast equipment failures and process deviations. This improves our uptime and allows us to do more proactive maintenance rather than reactive, and it also enables us to achieve a high level of operational production.”
Ridgway expects Industry 4.0 to continue to help in “improving productivity, efficiency, safety, resource utilization, increasing machines uptime and reducing breakdowns by using smart sensors. Also, it enables self-diagnosis, reducing turnover time, preventing breakdowns, reducing the human intervention, which will reduce human errors.”
The company’s IT and automation department, “A young, dynamic group of professionals with the requisite skillsets,” Ridgway said, is helped by management “eager for the comprehensive roll-out” in operations and through the wider value chain.
Adoption of Industry 4.0 tools began in earnest in 2018 with members of the core IT team evaluating the applicability of these technologies and deployment in key departments. Vendors have been contacted, and members of the IT and automation team have been working on technology integration as cost-effective alternatives.
Ongoing timeline for changes
Al Maamari said, “Technologies, by their very nature, keep evolving. Before Industry 4.0, there were three different waves that also evolved over decades. Our responsibility is to look at technologies and trends, as and when they come on the market, that will help us enhance our productivity, cost-efficiency and competitiveness.”
A plant-wide awareness program is designed to ensure technical staff is on board in the delivery of Industry 4.0 technologies. The company is also engaging with key stakeholders and local communities on the importance of Industry 4.0 for initiatives for safe, successful and sustainable operations.
Dana Geadah is communications manager, Sohar Aluminium. Edited by Mark T. Hoske, content manager, Control Engineering, CFE Media, [email protected].
KEYWORDS: Industry 4.0, process optimization
An aluminum smelter is integrating Industry 4.0 technologies.
Automation, robotics, Industrial Internet of Things are helping.
Communicating about efforts helps with implementation.
CONSIDER THIS
What IIoT and Industry 4.0 technologies can help advance your efficiencies?