Instrumentation devices required regular inspection to identify faults and prevent downtime, requiring large maintenance teams and high costs, but that's changing with digitalization.
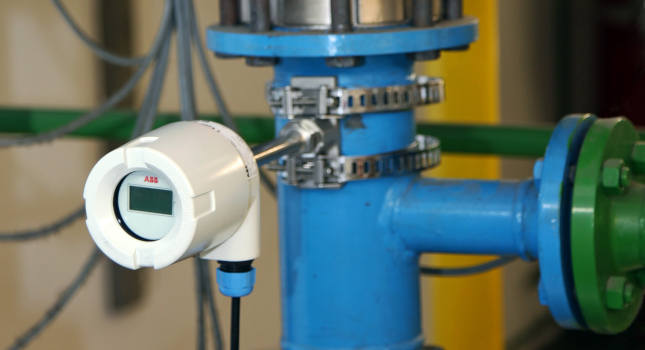
Process Instrumentation Insights
- Digitalization measurement and analytics technologies are helping to reduce the amount of feet required on the ground.
- There are more connected devices than ever in the instrumentation world, which can help provide more information than ever. It also leads to potential cybersecurity issues.
- Maintenance costs also are reduced, as smaller, specialized teams can allocate their time and expertise precisely where and when it is needed.
When it comes to critical equipment, we are entering an age where unnecessary maintenance is becoming a thing of the past. This is, in part, due to the sheer complexity of modern systems and processes. Prevention of failures and downtime is of course critical, but superfluous maintenance activities can in some cases end up doing more harm than good.
However, the risk of sudden outages for critical plant equipment must always be kept to a minimum. Digital technologies are helping to transform maintenance and help plant operators to strike the right balance between keeping vital equipment in optimal condition, while also avoiding the risk of interfering with processes that are already working perfectly well.
As a simple example, consider the modern motor car – 30 years ago, the handbook would instruct you to service almost every component, regardless of whether it requires it or not. These days, on-board computers flag up issues, in many cases before they turn into failures, and a service can now be as simple as downloading diagnostic data without even needing to inspect the vehicle. With breakdowns becoming less common than ever, it is clear that this is an approach that, if the technology permits it, can have considerable merit.
Change through digitalization
In years gone by a typical industrial facility may have had dozens or even hundreds of maintenance technicians managing instrumentation across a process. Digitalization, in the form of sensor, measurement and analytics technologies, is helping to reduce the amount of feet required on the ground, and transforming how we think of maintenance in an industrial context. This change is taking place at a rapid rate – as recently as 10 or 15 years ago smartphones were at the cutting edge of technology, yet it took less than a decade for them to reach critical mass. These days it is almost impossible to get a phone that isn’t a smartphone. In fact, the technology has advanced so far in such a short space of time that you could use your smartphone to access the diagnostics of your process plant, and even carry out some maintenance duties.
Instrumentation, and the ability to connect devices digitally to wider platforms, is set to revolutionize how we approach maintenance. Data gathered from field devices can be accessed at any time by anyone, from almost anywhere in the world. Aggregating this data allows for trend analysis across multiple devices, and even multiple sites to identify efficiency improvements and recurring faults that can help reveal underlying problems much more quickly than manually inspecting devices one at a time. Having an understanding of these trends, and access to reams of historical data to back it up, helps to facilitate a shift to predictive maintenance.
As well as improving reliability through the early detection of faults, digitalization is also providing significant benefits for safety by allowing devices to alert operators automatically if attention is required either for the process, or the instrumentation device itself. Having the ability to access devices remotely also speeds up commissioning time, as calibrations and verification can be carried out online, reducing installation costs. Maintenance costs also are reduced, as large teams – traditionally consisting of dozens of personnel manually inspecting each measurement device – can be supplanted by smaller, specialized teams that can allocate their time and expertise precisely where and when it is needed.
The concept of Industry 4.0 – whereby every device within an industrial facility is connected to the internet and equipped with its own intelligence – has been described as the fourth industrial revolution. Curiously, it is the first of all the industrial revolutions to have been identified as it was still happening, rather than in retrospect.
The number of smart, connected devices that are being installed every day is growing exponentially, not least in the world of industrial measurement and analytics. As well as opening up new opportunities for providing unprecedented visibility over processes, it also opens up new options for service – 24/7 support is now standard, while value is being added in the form of free services and tools to enhance equipment performance. Indeed, as technology rapidly evolves, manufacturers are having to evolve with it, providing new ways to add value, while offering closer collaboration with customers to develop bespoke solutions that lead to lasting partnerships. In years gone by, the purchase of a device would be the end of a customer journey, whereas now it is just the start.
Constant technology evolution
In such a rapidly evolving sector, constant evolution a necessity, as whilst a digital world of connected devices opens up vast new opportunities, it also creates new risks. The more devices that are connected, the more access points this creates for potential cyber incursions. In a worst-case scenario, the gateways and dashboards used to access, monitor and control equipment can also introduce extra layers of obfuscation between device and operator.
For instance, the Stuxnet worm, which was used to attack the Iranian nuclear program, was an attack that actually took advantage of a lack of manual inspection, by providing false readings to give the appearance that centrifuges were operating normally, when in fact they had been reprogrammed to destroy themselves. This is an example of a fail-in-place fault, which is the most dangerous type of fault. For all that digitalization is allowing us to carry out more duties remotely, mitigations must be built into any maintenance plan to prevent reliance on any one measurement or device. This can be achieved, for example, by using multiple types of sensor to measure the same variable, such as invasive and non-invasive flowmeters.
Cybersecurity has to evolve in order to mitigate against both emerging and existing threats. Protecting against cybercrime and sabotage is clearly a priority, but the value of the data must also be collected.
Digitalization is revolutionizing how maintenance is approached. By equipping devices with their own intelligence, potential issues and faults can be flagged up far earlier, and without the need for manual inspection. This in turn helps facilitate predictive maintenance, while allowing maintenance teams to be made smaller and more agile, cutting costs without compromising on reliability, safety and productivity.
– This originally appeared on Control Engineering Europe’s website. Edited by Chris Vavra, web content manager, Control Engineering, CFE Media and Technology, [email protected].