The digital twin is set to be a key technology for the success of Industry 4.0 and the Industrial Internet of Things (IIoT).
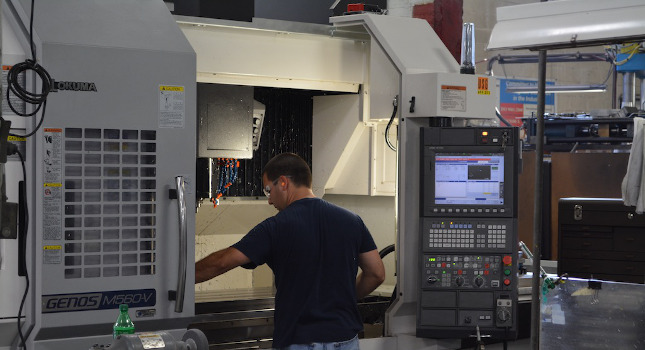
The Industry 4.0 vision of a digitally connected world relies on smart products communicating with one another and the outside world through the Industrial Internet of Things (IIoT). The concept requires a standardized approach to the description of these components and how they interact and relate to the other components or assets to make a smart machine. This precise, digital model is called the administration shell or digital twin.
The digital twin precisely describes the asset in a standardized and structured way. Each asset needs to ‘know’ its characteristic functions and features and how it fits into its environment – its relationship with other smart assets. The importance of the clarity of this information becomes clear when you look at the three-dimensional RAMI model and the relationship between the different elements of the product life cycle, the asset intelligence and the control hierarchy. The digital twin is a standardized and machine-readable digital product ‘label’ that enables the seamless flow of information throughout this three-dimensional model.
Two terms are frequently used regarding the digital twin, ‘ontology’ has been taken from philosophy and in this context is used to describe how a smart asset describes itself and has a sense of ‘being’ – what it is, what it does, its physical characteristics. Having this information embedded within the product or stored in the cloud and intrinsically linked to the product, provides the digital twin. This is the basis for smart products working in relationships to create smart machines and, when combined, smart factories.
Potential digital twin benefits
The potential benefits of the digital twin approach are enormous – reducing machine design and build times, optimizing performance throughout the machine’s operational life and having a key role in condition monitoring, predictive maintenance and smart maintenance. It enables product data to be merged with application information to provide data-driven insights and increasingly, through AI to predict future performance.
From the initial design stage savings can be made. For example, pulling digital twin information into an early-stage design concept enables the construction of a virtual 3D CAD model. This can be programmed and the operation and performance of the system evaluated without any metal being cut or assembled. Being able to seamlessly pass information between functions such as mechanical design, electrical engineering, control and software departments eliminates the wasteful re-entering of data with each function consistently building on the model rather than constructing their data set.
Future digital twin development
There is intense activity within international associations and standards bodies to continue the work of defining the structure and use of the digital twin. For over 20 years the eCl@ss e.V. organization has been working on classification standards. Now there is a clear convergence between what was originally a cross-sector data reference standard and the Industry 4.0 vision. This standard provides a structure that has already been adopted by more than 4,000 customers to semantically define even complex products and assets to support other machine-readable tools such as AutomationML, PLC Open, ProStep, etc. The eCl@ss standard defines how products are described in terms of both engineering and production, which is divided into two parts – machine and product, packaging and transport logistics). It also takes into account the hierarchy of assets to provide an asset knowledge architecture.
In a further recent development, in September 2020, the establishment of the ‘Industrial Digital Twin Association’ was announced. Commenting on this, Frank Melzer, a board member of Festo and head of the steering committee of the National Platform Industrie 4.0, said: “We are pleased that through the VDMA and ZVEI we have been given a neutral, yet industry-oriented, global platform that will carry the core technology of Industry 4.0 as an open-source into the world.” More than 20 leading digitalization companies are now working together in this alliance to enable data availability throughout product life-cycles and enhance the value creation opportunities.
This article originally appeared on Control Engineering Europe’s website.