International: A product lifecycle management conference in Europe helped demonstrate the future of design and manufacturing. New PLM tools advance digital twin technology applications, manufacturing execution, quality control, and other areas. In cloud-based implementations, 5G wireless will help.
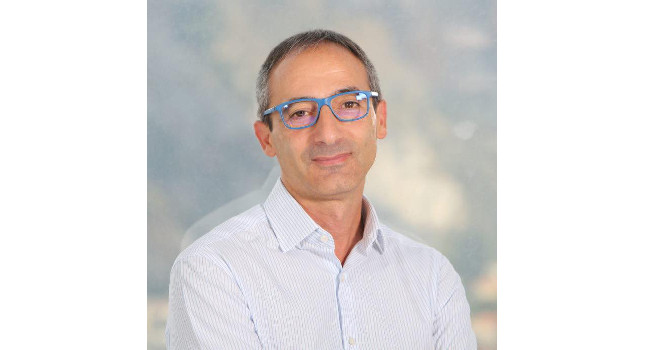
Future trends in manufacturing software were discussed at the Siemens PLM Europe 2019 in October in Berlin. At the three-day product lifecycle management (PLM) conference, Control Engineering Poland interviewed Maurizio Pazzini, vice president of technical enablement and product support, Siemens Digital Industries Software Italy. Pazzini has a key management position in the manufacturing operations management (MOM) business segment of Siemens Digital Industries Software and is involved in new product launches, implementations and post-implementations for Siemens end users, integrators, and users of the platform within Siemens.
Control Engineering Poland (CEP): The term digital twin has many contexts, including in factory maintenance applications. Where is the digital twin most used today?
Pazzini: Digital twin technology applications have room to expand, however, the most value from my point of view and from a manufacturing perspective is the area of manufacturing execution, and particularly in quality control.
The second version of a specific quality module in a modern, adaptable PLM system that connects people and processes, across functional silos. One of the most important things is when products are used in combination. MOM products can stand alone, but the full benefit of the digital twin can only be exploited when PLM and MOM systems are integrated. We are collaborating with a lot colleagues in both areas so that the offering and the configuration of the digital model fulfill shop-floor requirements.
The vision is to break down the silo between the quality department and the manufacturing department. We will create a unique backbone, where both departments will be able to have their own information. A quality execution module works with the manufacturing execution component to enforce manufacturing and quality control processes.
CEP: Will blockchain technology be used in future software for quality control or supply chain management applications?
Pazzini: Let me say we were doing a lot of investigations around blockchain and will be making a decision shortly about if we will put this into the product or not. I have seen many blockchain prototypes, so we are taking it seriously. We have specific departments in R&D for product innovation, including blockchain. They will propose the innovations, then our product management team evaluates the proposals.
Maurizio Pazzini, vice president of technical enablement and product support, Siemens Digital Industries Software Italy. Courtesy: Control Engineering Poland and Siemens
CEP: Digital twin is being used to remotely monitor what’s going on inside autonomous vehicles; how is this technology being used beyond manufacturing?
Pazzini: We look at the digital twin not from a purely manufacturing perspective, but from a utilization perspective. Leveraging the information in the case of an autonomous vehicle was a natural application of the software.
The autonomous vehicle has many Internet of Things (IoT) points, which allows us to send data mapped against the data model of the vehicle that exists as a digital twin. The digital twin knows how the product should behave and what the performance parameters are. This is why we can pretty easily perform these kinds of predictions, and we can check whether the vehicle is functioning as it was designed to and as it was planned to perform, or whether there are any deviations. That offshoot from a digital twin from manufacturing is being applied to product or system performance. In manufacturing, it is a digital representation of how the production process should be performing. Digital twin data is used to analyze the proper functioning of whatever products are produced. Digital twins differ depending on the area of application.
CEP: In autonomous vehicles and in manufacturing applications, how are 5G wireless technologies going to help?
Pazzini: The challenge is, how much can the infrastructure ease the adoption of cloud technologies in manufacturing? At the moment, customers are pretty skeptical because the MOM system is a business-critical system. Deploying a system in the cloud requires a very strong and reliable IT infrastructure. Use of 5G technologies in manufacturing requires creating a strong web-based cloud infrastructure with the same level of reliability as an on-premise platform.
CEP: We see the cloud becoming extremely important across many industries, particularly in manufacturing. Is there a preferred cloud platform?
Pazzini: It depends on the region. In Western countries, we see Amazon as a major player with large adoption by manufacturers. China is quite reluctant to implement AWS (Amazon Web Services) due to the need for greater data control. From our view, Amazon probably is the first choice of manufacturers for cloud platforms that customers are adopting.
It may be my personal view, but it seems more medium-sized businesses will endorse the cloud quicker than the large corporations because the large corporations at the moment do not see a big advantage in reducing some operational costs from redesigning their IT infrastructure. They have available big data centers and teams established, so it’s just fine for them to add one more system, for example, not the whole MOM system. We see large corporations adopting only pieces of the MOM system, and not mission-critical applications. Small and medium companies might have challenges in adopting MOM, but I see small and medium businesses adopting the whole system from the ground up, which is why I think that they will probably be the trendsetters for MOM adaptation.
CEP: Central and Eastern European manufacturing markets have an educated labor force at lower cost than other areas of Europe, but without enough labor, there’s a trend towards automated processes. How can automation continue to help manufacturing?
Pazzini: Repetitive manufacturing processes can be highly automated. The number of people on the shop floor is proportional to the complexity of the goods being produced. In aerospace, I don’t see fully automated manufacturing happening in the short term. For complex products, humans will still play an important part in production. As new industries emerge (like rockets), many engineers and production people will be needed to produce them.
CEP: So, you’re optimistic about the future?
Pazzini: Absolutely. I think our vision is well appreciated by customers, but we have challenges because our customers are always raising the bar. Once they buy the whole portfolio, they really expect a lot. Such interactions facilitate product innovation.
Michael Majchrzak is with Control Engineering Poland. Edited by Mark T. Hoske, content manager, Control Engineering, CFE Media, [email protected].
KEYWORDS: Product lifecycle management (PLM), digital twin
Integration of manufacturing operations management and PLM
High levels of automation work best for highly repetitive processes.
5G will help with cloud implementations.
CONSIDER THIS
Are you looking at advanced automation tools for a more efficient future?