Consider all costs when considering offshoring. Automation and other advanced technologies make a local smartforce more profitable.
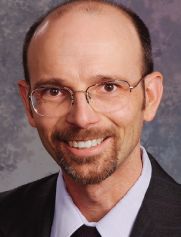
When people decided to offshore manufacturing capacity they may have excluded some things from their return on investment equations.
1. It seems that 60% of manufacturers use “rudimentary total cost models” and ignore 20% of the cost of offshoring, according to Harry Moser, Reshoring Initiative Leader, citing an Archstone Consulting survey at IMTS 2010. Moser said going local can reduce a company’s total cost of ownership (TCO) of purchased parts and tooling and offer other benefits, while retaining and regaining U.S. manufacturing jobs. He provides TCO Estimator software free to help OEMs compare the true TCO of local vs. offshore sources and to help job shops sell the benefits of local sourcing to their customers. At a NTMA/PMA Contract Manufacturing Purchasing Fair in May, 57 representatives from large manufacturers and 113 custom U.S. manufacturers attended. OEMs found competitive domestic job shops to manufacture parts and tooling; 64% of the OEMs brought onshore at least some work that was off shored. The next fair is Oct. 29, 2010, in Mashantucket, CT.
2. Smart upgrades can increase profits: In considering cost of production in their current facilities, manufacturers may not have appropriately quantified process and technology upgrades, with appropriate amounts of automation to lower production costs, saving jobs in the process.
3. Plant employees need to encourage leadership, management and unions (if present), to collaborate with others in the enterprise to revise workflows, work rules, and apply automation where it makes the most sense, to preserve manufacturing jobs onshore. All involved need to keep key goals in mind – greater competitiveness, safety, sustainability, innovation, and speed to market. Automation and other advanced technologies need to continue to help manufacturing as they have agriculture, making it less labor intensive, safer, and more profitable.
4. Spread the word: We need a manufacturing mandate and national manufacturing strategy. The Association for Manufacturing Technology, National Association of Manufacturers (p. 27), NEMA, and others have been explaining these needs to policymakers. AMT’s Manufacturing Mandate calls for a federal policy of collaboration among government, industry and academia. Policy would incentivize innovation and R&D in new products and manufacturing technologies; assure the availability of capital; increase global competitiveness; minimize structural cost burdens; and enhance collaboration between government, academia, and industry to build a better educated and trained “smartforce.”
They need your voices added to the mix, so their voices aren’t dismissed as special interests. Prosperity is special, and we all need to be more interested in explaining how smart U.S. manufacturing boosts U.S. prosperity.
www.reshoringnow.org
Control Engineering Sustainable Engineering Channel