A survey of industrial machinery companies explores the biggest issues with digital twin adoption. Machine builders are using digital twins to increase efficiency of machine design processes to get machines completed and running in less time at lower cost.
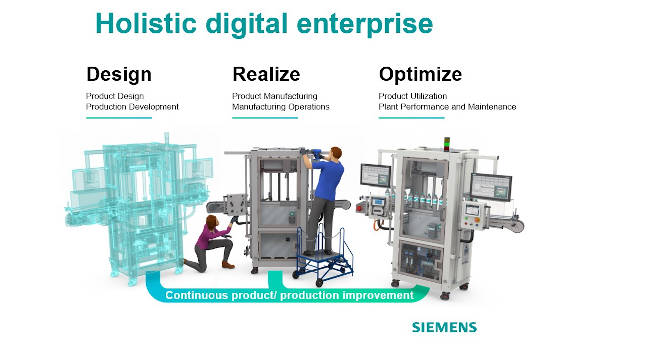
Customers are making increasing demands from machinery suppliers, which leads to greater customization, ease of use and integration to the customer plant and ecosystem. Machine reliability and lower total cost of ownership are among other needs. Software tools seamlessly integrate the machine development silos of mechanical, electrical, software, and simulation into one platform.
Scott Felber, NX product engineering software marketing manager, Siemens Digital Industries Software, in a June 30 Control Engineering webcast, “Accelerate machine designs, speed to market, collaboration, digital twin,” is expected to explain insights from customers and share recent research results to help industrial machinery companies with digital twin adoption.
Digital twins address transformation industrial trends
In preparation for the webcast, Felber outlined several transformational trends that mark a significant turning point in machinery evolution, helping to reshape the engineering, manufacturing and service operations for most machinery manufacturers.
A shift toward personalized products and customized services is challenging machinery companies to design and build machines that support expanding product mixes and more rapid and frequent changeovers, Felber said. Because consumer preference changes are more immediate, there is added pressure to innovate quickly and compress delivery schedules.
For example, a potato chip package has the potential for multiple variants, which help lead to an explosion of complexity, in size, shape, packages per box, recyclability considerations (output of machine) and regional flexibility including (flavors, size weight).
IIoT technologies, hyperautomation
Industrial component suppliers are quickly embracing Internet of Things (IoT) enabled technologies in products, and machinery manufacturers are on a steep learning curve to take advantage of petabytes of data that can be generated from today’s machinery. This has rapidly changed the landscape for electrical and controls automation engineers, from huge increases in input/output (I/O) channels, new communication protocols like 5G, to building intelligent programming that provides more interactive and granular control of devices.
The trend of hyperautomation requires vast amounts of data and cloud-based analytics to accelerate learning about machine behavior and performance to automate machine functions. Adding sensors may not be enough. Capabilities are needed to analyze the explosion of complex data being monitored.
Machine feedback from sensors; low-code cost reductions
For example, Felber said, even a simple fabric weaving machines are precision machines that can increase throughput by taking advantage of automation and incorporating feedback from speed, vibration, noise and temperature.
Hyperautomation also is enabled by low-code tools that can mine data analytics for many business processes – manufacturing optimization, as well as engineering reliability and cost reductions.
Leaders in the machinery space, the disrupters, are expected to embrace three key concepts to turn complexity into a competitive advantage.
These are the most comprehensive digital modern, adaptable, personalized solutions, and a flexible open ecosystem.
Overcoming obstacles to digital twins
Research conducted with Control Engineering sought to understand the biggest roadblock to adoption of the digital twin/digitalization. Largest three replies were corporate culture, initial cost and complexity of the solution at 18, 17, and 15% respectively. Responses in the next tier were: “tools currently in use” and “adoption is underway” at 7%, and training at 6%.
By using an integrated digital twin software based on one model eliminates the need to re-enter data into other systems, Felber said, for an efficient, accurate business process. The digital twin lower costs to manage intellectual content across assemblies, part manufacturing, and commissioning. That helps maximize revenue with proactive service, replacement part response, and upgrades to the machines.
Siemens Digital Industries Software NX design software platform has software for modeling, electro-mechanical design tool, including design input from simulation and manufacturing teams, managing the process and data across multiple domains and disciplines, use computing power based on a set of key inputs and outputs, and embracing additive manufacturing for more than prototyping.
A multidisciplinary platform serves the enterprise. The webcast provides more information and trends on digital twins.
– Edited by Mark T. Hoske, content manager, Control Engineering, CFE Media and Technology, [email protected].
KEYWORDS: Machine builders, industrial digital twins
Digital twins address transformation industrial trends.
Hyperautomation, machine feedback from sensors; low-code cost reductions can help machine builders and their customers.
Overcoming obstacles to digital twins can accelerate time to market.
CONSIDER THIS
How are you using digital twins to address industry demands and increase competitiveness?