An ultra-compact angle sensor built from flat optics captures these measurements at 30 frames per second, which will allow for more accurate and precise measurements of tiny atomic materials.
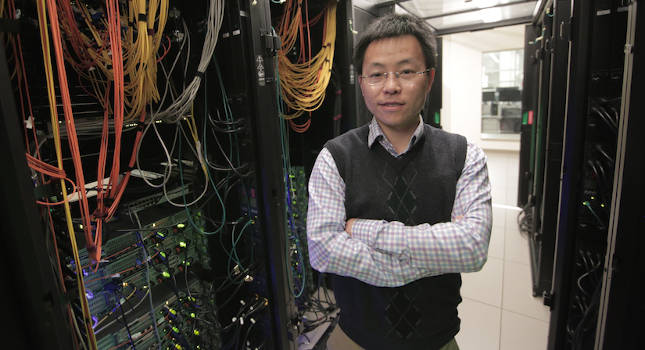
Peering through a microscope reveals all sorts of information—the structure, composition and even atomic arrangement of a sample material. But quantifying what’s visualized by the microscope is very tricky, since specialized tools are often needed to make such tiny measurements.
When researchers want to map and measure the topography—the overall form and features on the surface of a sample—they rely on large benchtop gadgets called white light interferometers, which measure features all the way down to tens of nanometers.
The problem, however, is these interferometers take up to a minute to produce a single measurement. That’s much too slow to record changes over time.
Now, an ultra-compact angle sensor built from flat optics captures these measurements at 30 frames per second, allowing high-resolution video capability. A team led by Zongfu Yu, an associate professor of electrical and computer engineering at the University of Wisconsin-Madison, created the sensor, described in the Oct. 13, 2021, issue of Nature Communications.
“You can get an impression of what a material is like from a microscope,” Yu said, “but measuring the surface morphology quantitively gives you a lot more information.”
The design works by measuring the wavefront of light using a novel type of sensor developed by Yu’s team. Light travels as an electromagnetic wave, but currently there is no way to measure this wavefront—the light wave’s shape—directly. Instead, researchers can only measure it when it interacts with another light wave (a process called interference), or when the wavefront is reflected or refracted.
To measure wavefronts, current sensors use a beam of light to create interference patterns that are then interpolated to provide information about its shape. Another current method, called angle-based wavefront sensing, uses a grid of micro-lenses that sample the incident angles of the wavefront, producing an image.
In practice, both methods are slow, bulky and low-resolution.
To produce its angle sensor, Yu’s team modified an off-the-shelf 6.6 millimeter CMOS sensor—the type of flat sensor found in many cell phone cameras—which uses millions of pixels to produce an image. Using photolithography, the team deposited an extremely thin layer of aluminum over the sensor, producing a grid of tiny square apertures, each made up of just four 5.2 micrometer pixels. Each four-pixel square acts as an angle sensor, able to determine the incident angle of a wavefront. Combined, the millions of tiny angle sensors on the CMOS chip collectively operate as a wavefront sensor and can create high-resolution surface topography measurements.
The most significant advantage of this wavefront sensor over other technologies is its high resolution, which is two orders of magnitude larger than traditional angle-based sensors. This allows the device to collect images rapidly enough to produce high-resolution video of morphological changes in real time. As a test, Yu and his team analyzed a small drop of liquid polymer using the device, recording the microscopic surface changes as they dried it using a heat gun.
The sensor, which is small enough to fit in a housing the size of a cell phone, could have applications in many different fields of study and in industry. “For example, this could be used in material manufacturing. If you need a very smooth surface, you could measure atomic smoothness with it, or you could look at biological samples and how living tissue changes over time,” Yu said.
– Edited by Chris Vavra, web content manager, Control Engineering, CFE Media and Technology, [email protected].