While thermowells are often used in process safety measuring, non-invasive measuring can offer many benefits and improved results.
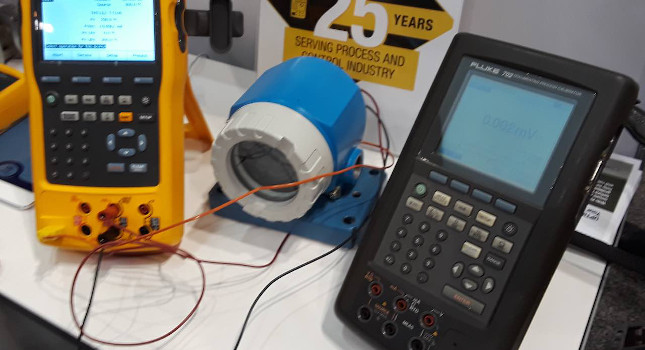
The importance of temperature as an indicator of the efficiency and safety of industrial processes makes it important to measure it as widely as possible. In many cases, thermowells have been the preferred solution. Essentially they are metal sheaths which protect the measurement sensor against the process being measured, and are widely used in temperature measurement applications – from food and beverage through to oil and gas.
Despite being the go-to solution for many process operators, thermowells can be problematic. Constant exposure to process mediums, especially those moving at high speeds and/or containing high levels of abrasive particulate matter, can lead to wear and tear that can cause a sensor to fail or break. If the failure is detected, the process will need to be shut down to maintain or replace the device. Although specialised options are available offering higher resistance, the exotic nature of the materials used can substantially increase the total purchase price.
Disruption is also an issue when installing a thermowell. The need for the thermowell to be in direct contact with the process medium requires a hole to be drilled into the pipeline, requiring the process to be shut down.
Complications can also arise when it comes to specification and installation, with the wrong choice of insets, incorrect insertion lengths, or poor contact all increasing the risk of measurement errors. If a second thermowell is not installed in the same location to compare and validate readings, these errors can go undetected, potentially causing issues and consequent damage elsewhere in the process.
To address these and other issues, there has been a tightening of standards such as ASME PTC 19.3 TW-2016, which govern the stability of thermowells, increasing engineering costs and restricting the application of conventional thermowells in some situations.
Non-invasive measuring solutions
A new type of measurement device has emerged that can be used in many industrial measurement applications to reduce the complexity, time and cost of setting up new temperature measurement points. ABB’s non-invasive temperature solution, for example, eliminates the need for a temperature sensor to be inserted into a pipeline, instead using the pipe itself as the temperature sensor to produce an accurate reading of the process temperature.
This is achieved through two steps. The first step involves predicting the temperature difference between the process and the pipe surface temperature. Using pipe geometrical and material parameters coupled with fluid flow rate, viscosity and density, the thermal field within the pipe can be accurately modeled. These models show that for turbulent flowing media in a metal pipe, there is a negligible but calculable temperature difference between the bulk temperature of the process and the skin temperature of the piping. This condition accounts for the majority of process conditions in the industry.
The potential suitability of non-invasive temperature measurement for temperature applications can be assessed using an engineering tool. Data on the pipeline and flow characteristics can be used to assess the likely performance of a non-invasive sensor against a thermowell, enabling engineers to make an informed decision about which technology will offer the best performance for their application.
The tool was recently used by a chemical producer that wanted to ensure that its process – which involved a highly viscous polymer liquid – did not drop below a given temperature. The company previously had encountered significant challenges with invasive thermowells in terms of wear and tear and product quality.
The second step is to get a simple, repeatable, and reliable surface measurement of the pipe surface temperature. Traditional ‘skin temperature’ sensors, which measure the temperature at the pipe wall, have been one way of achieving this. However, the performance of these devices can be hampered by a variety of factors, including potential inaccuracies caused by ambient conditions.
Non-invasive sensors can eliminate these drawbacks by using a double sensor architecture, where one sensor is in contact with the surface of the pipe and the other measures the ambient temperature conditions in the immediate vicinity.
The data produced is then used by software which compensates for contact resistances and ambient effects to calculate an accurate temperature measurement for the process medium in real time. By combining data on the ambient conditions with models that predict the behavior of liquid or liquid-like mediums flowing in turbulent regimes in metal pipes, the accuracy and responsiveness of the surface measurement is improved, enabling comparable performance with a traditional invasive device to be achieved.
Save time and cost
A key advantage of this new approach to non-invasive temperature measurement is its reduced cost, with potential CAPEX savings of up to 75% achievable compared to a classic thermowell installation.
Much of these savings are due to the easy-fit nature of the sensor. The use of two clamp collars allows the sensors to be attached without penetrating the pipeline. The amount of insulation required is also reduced, with just the foot of the device needing to be covered. As a result, the sensor can typically be installed in under an hour, enabling operators to quickly get up and running.
There is also little work required for specification. One major area that is eliminated is the need to carry out wake frequency calculations, which are needed for invasive installations to assess criteria such as sensor size and the material of construction that needs to be used. The need for such calculations, together with the associated process adjustments, can typically increase the total price tag of thermowells by two to three times over their material cost.
Cost savings can also be achieved when it comes to checking thermowell performance and accuracy. The inherent installation and cost benefits of non-invasive temperature sensors make them ideal for validating measurements from both thermowells and other non-invasive sensors. If the non-invasive sensor is delivering substantially different readings to the installed devices, this may indicate a problem that requires investigation. Previously, the only way of achieving this would have involved installing additional thermowells, with all the attendant drawbacks this entails.
As the idea of non-invasive temperature measurement takes hold, companies will be able to transform the way they measure an expanding range of flow regimes and fluids with more complex heat transfer behavior with the same levels of accuracy, reliability and responsiveness as thermowells. So, if you are considering a thermowell, now may be the right time to consider making a switch to non-invasive measurement.
– This originally appeared on Control Engineering Europe’s website. Edited by Chris Vavra, web content manager, Control Engineering, CFE Media and Technology, [email protected].