In advanced process control (APC), closed-loop multivariable control brings the inherent benefits of greater timeliness and consistency, fewer alarms and constraint violations and more effective process optimization. Multivariable control is core to most process operations. See “What is ‘real-time’ optimization?”
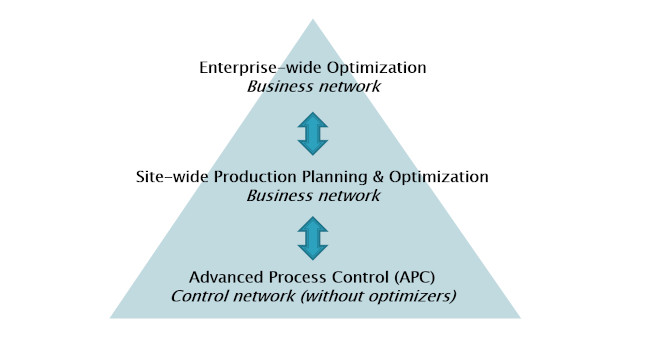
Learning Objectives
- Discover why changes are needed in multivariable controls.
- Learn why automatic multivariable control is better than manual multivariable control.
- Understand the need for multivariable competency for better process automation.
Multivariable model-predictive constraint control and real-time optimization, better known as MPC technology, has had a very good run. It has dominated advanced process control (APC) for several decades, to the exclusion of most other types of APC activity. Operating companies have invested tens of millions of dollars in MPC (hundreds of millions or billions collectively) and earned millions of dollars in return.
Changes needed in multivariable controls
The attractive promise of closed-loop multivariable control and real-time optimization has meant users have stood by their commitments to MPC for decades, even though its high costs, fragile performance, and complex ownership demands have persisted, rather than improving over time.
The conventional MPC technology ownership paradigm increasingly is considered unsustainable. MPC has proven too expensive and unwieldy to form the centerpiece of a multivariable control core competency, which the manufacturing industry needs. Accumulated experience now suggests changes in the industry’s multivariable control paradigm may hold more promise than continued efforts to fix and overcome conventional MPC’s challenges.
Multivariable control is fundamental
MPC technology can be said to comprise three parts: model-based control, real-time optimization and multivariable control. For APC purposes, multivariable control is the essential piece (noting that optimization, though not necessarily real-time optimization, is always part of multivariable control – see sidebar). Model-based control and real-time optimization are part of the way MPC technology solves the multivariable control problem, but experience has revealed there are other simpler ways to solve multivariable control that don’t require these elaborate methods.
MPC has often been shrouded in complexity. A simple way to view multivariable control is it automates the single-loop controller adjustments (setpoint and output changes) that otherwise are left to the operating team to manually implement. When operators make controller adjustments in the course of a day – of which there are often many – that’s manual multivariable control. When APC is applied to better coordinate and automate those adjustments for groups of related controllers, that’s automatic (or closed-loop) multivariable control. Like single-loop control, closed loop multivariable control brings the inherent benefits of greater timeliness and consistency, fewer alarms and constraint violations, and more effective process optimization. In many applications, this can earn hundreds of thousands or even millions of dollars annually.
When operating teams carry out manual multivariable control, they do it without the aid of detailed process models and real-time optimizers. This shows how automatic multivariable control also can be solved without detailed models and real-time optimizers by automating proven methods that have always been manually employed by operating teams. (See later Figure 1 explanation.)
The Expendables: Model-based control, real-time optimization
Not only are model-based control and real-time optimization dispensable to the central objective of multivariable control, but experience and insights suggest they may be undesirable aspects of the control network layer going forward.
Model-based control has been a huge source of costs and maintenance. It was originally anticipated that a plant step test, though expensive and intrusive, would be a one-time event. As experience accumulated that models are actually short-lived, the need for performance monitoring, model maintenance, and periodic retesting arose.
MPC technology today is pursuing continuous online adaptive modeling, but this overlooks the lesson industry has already learned from single-loop auto-tuning – if auto-tuning was not successful on a single-loop basis, it is not likely to be successful on a multivariable basis. Meanwhile, it adds yet another layer of ownership cost and complexity to MPC.
Localized control network layer optimization
Real-time optimization has been another persistent source of MPC ownership challenges, so the value-added proposition of deploying real-time optimization at the control network layer warrants new scrutiny.
Optimization within the control network layer is localized at best, encompassing a small handful of locally-available inputs. The vast majority of data inputs needed for meaningful process optimization reside throughout other process units, the business network, and the enterprise. In modern plants, the business production planning function is the natural locus of process optimization, not the control networks (Figure 1). Industry has also seen that only limited amounts of data, in the form of updated limits or targets, actually need to flow from the business layer down to the control network, which is accommodated by modern tools and connectivity.
The resources, complexity and maintenance to run massive model-based control and real-time optimization at the control network layer has largely proven incompatible with the mission criteria of industrial automation networks. In the control network layer, compact deterministic algorithms with minimal inherent maintenance and support needs are the desired characteristics for automation reliability, network reliability, and cybersecurity objectives. Deploying complex model-based control and optimization solvers with high ongoing maintenance and support burdens into the control network conflicts with these principles.
Multivariable control is a core-competency
Figure 2 compares key aspects of the conventional MPC paradigm and an updated multivariable control paradigm based on industry’s lengthy experience. The updated paradigm has already been emerging by industry consensus, though commercially available off-the-shelf products as yet remain limited.
Many aspects of the conventional MPC paradigm are fundamental to multivariable control and will carry forward into the new paradigm, such as the concepts of manipulated variables (MVs), controlled variables (CVs), the matrix, limits and targets. At the same time, other aspects of MPC the industry has been accustomed to, such as plant tests, detailed models and real-time optimization, may disappear from APC going forward based on an updated assessment of their net pros and cons.
A central aspect of multivariable control is it becomes an industry core-competency, which is desperately needed, because industry can now see multivariable control is a core aspect of almost every process operation (ask any operator). This means multivariable control is as fundamental to successful process operation as good single-loop control.
Multivariable control must evolve into a core-competency to move process automation to the next level. This is in the best interests of all APC and process operation stakeholders.
What is “real-time” optimization?
Optimization – though not necessarily real-time optimization – is always a part of multivariable control. Multivariable control is a two-dimensional multi-loop control strategy that does not aim for a single operating point. Instead, it aims to keep process operations within a two-dimensional operating window, bounded by process constraint limits. Multivariable control also uses remaining MV availability (also known as remaining degrees of freedom) to pursue optimization targets to the extent possible within the window.
The vast majority of optimization target and constraint limit values are entered into the multivariable controller by operators and engineers, just like single-loop controller setpoints and limits. Where appropriate, some target and limit values may be periodically updated from the business layer optimization solution (Figure 1). Target and limit values also may be determined in “real-time” by optimization solver programs deployed within the control layer in conjunction with multivariable control – this is known as real-time optimization within traditional model-based multivariable control technology (MPC).
Control layer (that is “real-time”) optimization made sense in the 1980s, when optimization tools in the business layer were less automated and connectivity between the layers was almost non-existent. Today, control layer optimization cannot begin to compare with business layer optimization in terms of globality of inputs, sophistication of tools, and appropriate optimization time scales. Experience also has shown real-time optimization to be in conflict with control network mission criteria because deterministic algorithms and minimum maintenance are important principles for network reliability and cybersecurity purposes.
Allan Kern, P.E., is owner, APC Performance LLC. Edited by Mark T. Hoske, content manager, Control Engineering, CFE Media and Technology, [email protected].
KEYWORDS: Advanced process control (APC), model-based multivariable control (MPC)
CONSIDER THIS
Is your software improving or decreasing process efficiency?