Engineers tasked with modernizing their process control systems and distributed control systems (DCS) have many considerations.
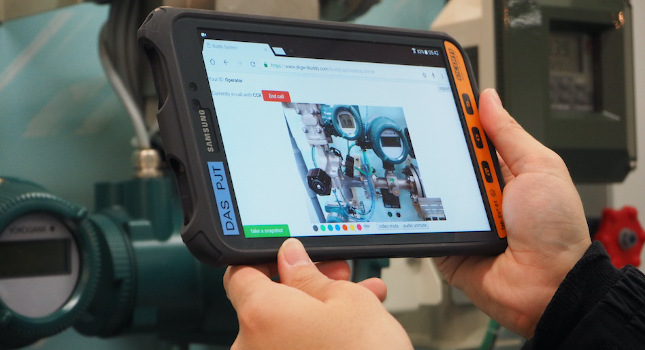
DCS insights
- Modernizing distributed control systems (DCS) involves assessing the lifespan of process units and existing DCS components to make informed strategic decisions for upgrades, partial migrations or full replacements.
- Incremental upgrades allow for targeted updates with minimal downtime, while ensuring interoperability between existing and new hardware, aligning with production schedules and budget constraints.
- Open process automation (OPA) architecture offers significant benefits like interoperability, flexibility, cost efficiency and enhanced cybersecurity, making it an attractive option for comprehensive DCS modernization.
In the dynamic landscape of process control, modernizing distributed control systems (DCS) requires a great deal of strategic foresight. Although the typical lifespan of a DCS system is around 15 years, the process units can outlive the control systems by decades.
Due to rapid advances in operational technology (OT) and information technology (IT) convergence, as well as demanding economic and cybersecurity needs, modernization of DCS has become a priority for many organizations. Better control strategies — leading from industrial automation to industrial autonomy — are now available to improve process performance.
Today’s DCS systems no longer work as islands. They are, for example, now able to integrate with enterprise resource planning (ERP) systems.
Some fundamental factors can help guide the critical decision-making process. These include:
-
Process unit lifespan: First, assess the expected lifetime of the controlled process unit. Understanding its longevity will set the stage for informed modernization choices.
-
Existing DCS evaluation: Next, scrutinise the existing DCS. Is it in the sales phase or the maintenance phase? What is the support strategy offered by the DCS vendor? Assess the current DCS in terms of hardware and software. Understanding the existing system’s capabilities and limitations can help guide what needs to be upgraded or replaced.
The DCS components’ lifetimes may help to make the right decisions:
-
Wiring: 40 years
-
I/O and termination panels: 20 years
-
Controllers: function trouble-free for about 15 years
-
Displays: 8 years lifespan
-
Workstations: 5-6 years
From this, we see that strategic DCS modernization hinges on understanding lifespans, evaluating existing systems and aligning choices with business needs.
Strategic decisions
Once evaluations have been made, engineers will then be armed with the information they need to tailor the modernization approach, choosing one of the following:
-
Operation-level upgrades: For targeted enhancements, focus on updating or upgrading operation-level components (operator/engineering stations).
-
Partial migration: Alternatively, explore partial migration options to optimise existing infrastructure.
-
Full replacement: If warranted, consider a complete overhaul of the DCS system. This is a more suitable option if the plant lifetime is more than 15 years, and the priority is improvement, better control, cost reduction and new technology adaptation.
Incremental upgrades represent a strategic approach to modernising components rather than overhauling the entire system simultaneously. This method allows for targeted updates, such as individual Human-Machine Interface (HMI) improvements without halting control functions.
The primary advantage of this approach is the significant reduction in production downtime and a lower risk of operational shutdowns. Upgrade plans can be tailored to align with the production and maintenance schedules, as well as budget constraints.
A crucial element enabling this strategy is the interoperability between existing and new hardware within the system, ensuring seamless operation.
It is important to choose technologies that not only address current needs but which are also scalable and adaptable to future advancements. There are considerable advantages to selecting the same vendor as the existing system, if the vendor has the right support and conversion tools to reuse the existing application.
Additional modernization considerations include:
-
Integration with other systems: A modern DCS should seamlessly integrate with other systems to enable data flow across the organization, facilitating better decision-making and efficiency.
-
Cybersecurity measures: With the increasing connectivity and openness of industrial control systems, cybersecurity becomes paramount. The new DCS should include robust security features to protect against both internal and external threats.
-
Training and change management: Adequate training for operators and maintenance staff, coupled with effective change management strategies, ensures smooth system adoption. Consider building a digital twin or operator training simulator.
Full replacement strategies
If your strategic decision is a full replacement and overhaul of the existing DCS, the best option is to consider an open process automation (OPA) architecture. This offers a new approach to DCS design and implementation, aiming to provide greater interoperability, flexibility and efficiency compared to traditional DCS architectures.
OPA architecture presents several advantages, including:
Interoperability: OPA promotes the use of open standards, making it easier for equipment and systems from different vendors to work together seamlessly.
The interoperability of OPA facilitates the integration of legacy systems with new technologies.
OPA’s modular framework supports plug-and-play components, enabling users to add, upgrade or replace system parts with minimal impact on the overall system. This modular approach supports scalability and future-proofs investments.
The flexibility of OPA allows for tailored solutions that meet specific operational needs, enhancing process optimization and performance.
Cost efficiency: The modular nature of OPA can reduce lifecycle costs, as individual components can be updated or replaced without a full system overhaul. As such, a full plant stop can be prevented in most cases, saving costs.
Enhanced Innovation and rapid adoption of new technologies: The architecture’s openness and modularity make it easier for organizations to adopt and benefit from advances in AI, machine learning and data analytics.
Improved cybersecurity: OPA includes cybersecurity considerations from the ground up, incorporating current best practices and standards for industrial control systems.
Considerations for minimizing risk during DCS migration include:
-
Phased implementation: Instead of a complete overhaul, consider a phased approach to migration. This reduces operational costs.
-
Pilot projects: Start with pilot projects in less critical areas of operation. These pilots can serve as benchmarks, allowing adjustments before full-scale implementation.
-
Data backup and recovery plans: Ensure there are robust data backup and recovery procedures in place. This is crucial for protecting against data loss during the migration process.
The OPA architecture brings a transformative approach to DCS migration, offering significant advantages in interoperability, flexibility, cost efficiency and innovation. These benefits make it an attractive option for organizations aiming to modernise their control systems in line with contemporary digital transformation goals. Yokogawa was selected by ExxonMobil as the system integrator for the first field trial of an OPA system designed to operate an entire production facility — this is currently at factory acceptance stage (FAT).