Automation system integrators explain what technologies to consider for control system integration projects.
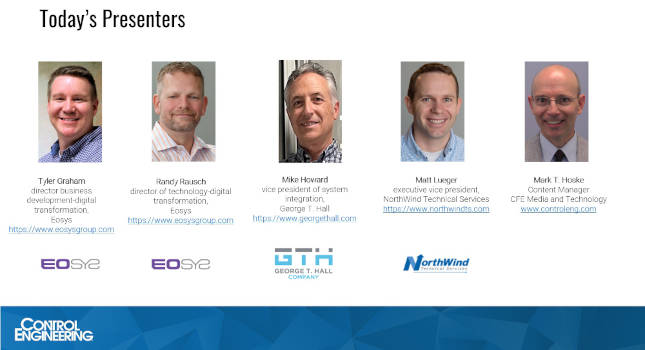
Learning Objectives
- Edited transcript from a popular Control Engineering webcast provides automation system integration advice about automation technologies to consider.
- Understand benefits of MES and 3 more things to help digital transformation, automation project implementation.
- Review benefits of newer industrial technologies such as Git version control for PLC programming, augmented reality and software conversions, along with technologies to attract and help the new generation in manufacturing operations.
Control system integration insights
-
An edited transcript from a popular Control Engineering webcast provides automation system integration advice on technology selection and use.
-
Manufacturing execution systems (MES) and 3 other technologies can help digital transformation, automation project implementation.
-
Newer industrial technologies can help with control system integration, including Git version control for PLC programming, augmented reality and software conversions. Use of newer automation technologies such as mobile apps can attract and help the new generation in manufacturing operations.
Control system integrators explain what emerging and existing automation technologies can help with automation system integration projects. The advice, part 3 in an article series, was adapted from a transcript of popular Control Engineering webcast, “Automation Series: How next-generation automation will help in 2023,” with help from OpenAI’s ChapGPT, then reviewed and further edited by webcast moderator, Mark T. Hoske.
Webcast instructors were:
-
Tyler Graham, director business development-digital transformation, and Randy Rausch, director of technology-digital transformation, Eosys
-
Mike Howard, vice president of system integration at George T. Hall
-
Matt Lueger, executive vice president, NorthWind Technical Services.
A question asked of the system integrators during the webcast was: What is important automation and control technologies for system integration projects?
MES and 3 more things to help digital transformation, automation project implementation
Rausch: Having a manufacturing execution system (MES) is a really important part of your digital transformation. That’s not necessarily a new fancy technology in 2023, so I’m excluding it from my new technologies list. Ensure you have a good MES, and then pay attention to the following three things that will accelerate you on your digital transformation journey.
-
Artificial intelligence and machine learning (AI/ML): AI/ML finds nuggets in highly dimensional data
Utilize MLOps (combining machine learning and DevOps) for inference at the edge.
-
Ontologies and graph databases: Need context and ability to learn/persist new relationships. Enable analytics at a higher level.
-
Event-driven architectures: Use a centralized message broker (Unified NameSpace) and publish/subscribe protocols.
If you embrace digital transformation to run a business better, sophisticated analyses are likely necessary. They’ll likely be highly dimensional, lots of different inputs. Humans are usually pretty bad at this type of problem, but computers are actually quite good. AI/ML tools are readily available to help make sense of all the data you’re collecting.
When deploying a machine-learning model, keep it fresh. Take advantage of the fact that every day more data is available. If you’re using data to train your models, you can make your model better daily. The training, testing, evaluating and deploying of these models can be automated. Usually that’s called MLOps, a combination of machine learning and DevOps. That make machine learning more effective, keeps it fresh and improving daily, instead of fading as the process naturally varies.
Why you cannot just drop AI/ML onto traditional manufacturing
AI/ML are fantastic technologies that already have changed the world, but they require a massive amount of data to really do a good job training and to run predictive analytics. You really can’t just drop AI on top of traditional manufacturing systems, because there’s two key problems to overcome.
One, the relationships between all those data points in those various information systems, it’s usually not codified in a way that automation can learn from. Second, data is trapped in silos, and it’s difficult to get a massive amounts of data out in a usable format. To get the context, meaning and relationships from data, use ontologies. Ontologies classify and explain data relationships in a formal way. Ontologies allow us to link entities and understand, for example, how a temperature sensor value relates to a product quality attribute, and how that relates to another thing of interest.
When these relationships and context are captured in an ontology, automated information processing systems can be applied. If you store these relationships in a graph database, you can efficiently learn new relationships to build from an ever-growing understanding of your operation.
To contrast that to a more familiar way, suppose you identify that a previously unknown relationship between two sensor values, so now you need to change a property in a relational database. It used to be single-valued, now it needs to be multi-valued, which would require you to delete the entire column for that property, create an entirely new table and add a foreign key reference. It’s a ton of work, hard and expensive to do, so usually it’s not done.
Instead, learning a new relationship about two data points with the graph database that would be inserted as a node in the database is a much easier way to apply and take advantage of that new data relationship that you learned.
I’m not suggesting replacing the MES or enterprise resource planning (ERP) historians. I’m suggesting you add a graph database that stores relationships among existing data stores. This lets the AI/ML algorithm provide the context, enables you to discover new relationships and accelerates learning. Using a graph query language as part of the query helps eliminate a lot of the performance problems of trying to extract massive amounts of data multiple times for AI/ML systems.
We can’t know everything in advance, if we expect business to continuously learn, one of the things that we need is all that data. We need that data with context. Because you don’t know ahead of time what data you need, one suggestion is to grab it all. Using an event-driven architecture as opposed to a point-to-point integration that can give you all that data.
The PLC can publish data. If you don’t end up using the data, it doesn’t really matter. The technology enables you to move all that data without a huge load on the processor and on your network. Once you learn something new, you can push the knowledge back into that event-driven architecture or name space so that others can take advantage of it also. Using data that becomes information lowers the cost of future systems integrations and maintenance.
To summarize: Get all the data, publish it to a central hub or unified data space, capture the relationships you know today in an ontology, update that ontology when you learn a new relationship between data points, apply machine learning and machine learning applications to automate complex analysis and help discover the root cause of your nagging problems.
If you stack all these technologies together, you can make your better business decisions faster, accelerate your digital transformation and give yourself the business agility you need to win in the market.
New technologies: Git version control for PLC programming, augmented reality, software conversions
Howard: Some of the new technologies in 2023 that George T. Hall is looking at and starting to implement include Git version control for PLC programming, augmented reality and additional software conversions.
For us, this version control is a pretty exciting new technology that leverages cloud-based type solution that allows you to share development across regional offices and allows developers to work on the same file at the same time, all while maintaining version control and traceability.
Some Git advantages include that it’s a mature open-source tool, around since 2005 and it’s the most widely used version control system in the world for software developers. Git version control has been a challenge for PLC companies to embrace, because there’s not a lot of standardization across manufacturers. Git is distributed and the files are stored locally and in a repository, so developers can work without network access. It’s fast, and history is stored local on a user’s device. It’s secure. There’s an algorithm that ensures that every edit is traceable. This is a tool that we’re finding to be very valuable.
Another interesting technology that we’re exploring further is augmented reality. Having seen numerous demonstrations and applications for this technology, we’re exploring how it can benefit our clients in training and maintenance and troubleshooting of machines and equipment. It’s a technology that’s designed to add a digital element over equipment using a tablet to provide a visual of the equipment inside, say, an enclosed enclosure that may or may not be accessible. Data that’s available in augmented reality can help with troubleshooting and improve machine health. Different types of data are available through that graphical type interface while on the plant floor.
We’re also looking at additional software conversion applications. This software continues to reduce our time and expense in a lot of modernization and upgrade applications. Most manufacturers are offering software conversion utilities to convert legacy platforms to newer systems. Some even offer cross conversions to convert from one manufacturer’s PLC to another. Most of applications we convert are legacy ladder logic, and we’re moving to an IEC 61131 standard. Five languages are incorporated with that: instruction list, structured text, ladder logic, function block, and NSFC.
Conversion tools are efficient and help expedite the conversion and modernization process, but they’re not perfect. They capture 80 to 90% of the original code usually, but there are some functions that need to be rewritten in the new language. Conversion tools also can prevent a user from taking advantage of some of the other languages. Example, when converting ladder to ladder, we may see some functions that would be better suited for structured text, and those would have to be coded from scratch.
These are some of the exciting technologies that we’re exploring and using. There are too many to discuss, but I think the industry as a whole is going through its own modernization. It’s exciting time. It’s constantly changing. It’s useful to help people explore and understand what is new and what is coming out in industry.
Technologies to attract and help the new generation in manufacturing operations
Lueger: As system integrators, new technology applications are most exciting for us and has been for a while. But even as Industry 4.0 is gaining traction, we personally felt that we had a lot of customers who were hesitant or dismissive of the potential of many available new industrial automation technologies. Over the last couple of years, primarily due to the changing workforce and a younger generation of people coming in, we’re finding prevailing technologies that can help, the stuff that has risen to the top to provide benefits for many customers, including analytics, mobility software and advances in robotics.
At the top of that list is advanced analytics, AI and machine learning capabilities. You see an adoption from OEMs and machine manufacturers and component manufacturers to make their stuff accessible to systems and to have more data embedded in them. There’s still the challenge of getting that to a central kind of storage place. The tools are there. The digital twin software applications are there to help you get more predictive information out of the systems.
New tools enable a more mobile workforce. We’ve grown up and had children grow up with tablets or devices in their hands, and we haven’t seen as much of that adoption on the plant floor. The younger generation’s coming in and expecting app-based interfaces. They expect to be able to pull something up on a tablet and have the same sort of interaction, same sort of icons that they’ve grown up using. Why can’t they get that information out of the system?
The last is more robotics. Industrial robots have been around for a long time, but as an example, many industries haven’t applied them in the processing areas or upfront in workflows. A lot of customers are striving for efficiency gains. They’re struggling to find people in those areas and are looking at how robots can go into those places. The need to find someone to do some of those jobs is greater than it has been before.
Auto-guided vehicles or autonomous mobile robots can help in traditional warehouse spaces or processing areas spread out at the front side of facilities. People are diving into many applications, not because they want to go down this Industry 4.0 journey, but because they need to, and their workforce is demanding it.
Mark T. Hoske is content manager, Control Engineering, CFE Media and Technology, [email protected].
CONSIDER THIS
How can system integration experts help your next automation project with technology selection?
ONLINE
View the webcast until Jan. 18, 2024
Webcast instructors answer more audience questions about next generation automation in this article.