Think Again: Increase data flow and analytics while decreasing risk of cyber security intrusions, by using services, according to experts in cloud-based manufacturing services, cyber security, and digital factories. These are building blocks of Industry 4.0 and Industrial Internet of Things.
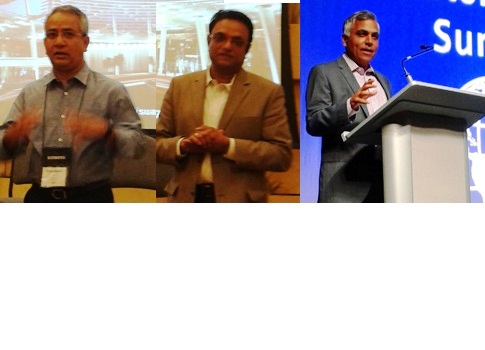
Customer services are gaining in importance for manufacturing and other industries, to make better use of data previously collected and often not used because of lack of computing power and the high cost of storage. Those issues can be resolved, explained Jagannath Rao, president, customer services division, Siemens Industry Inc., industry sector.
Advancements in procedures and technologies allow companies to increase connectivity and lower risk of cyber-security intrusion, said Rajiv Sivaraman, senior vice president, global head of plant security services, Siemens Industry Inc., digital factory division. Rao and Sivaraman shared advice with editors and analysts at Siemens Automation Summit, a user conference, in June.
Raj Batra, president, digital factory, Siemens Industry, said a revolution is coming to industry, with "digital everything," including scalability.
"I’ve even seen a digital car wash. If a car wash can do this, so can everyone in this room," Batra told attendees at the conference, which was held in Las Vegas June 21 to 25. "We need to find ways to be ultracompetitive." Summarized comments and advice from Sivaraman and Rao follow below. Most of the advice involves elements of Industrial Internet of Things (IIoT) and Industry 4.0, which improve the use of technology data and information flow.
Digital factory opportunities
Manufacturing may have a head start in the world of big data analytics, said Rao, because of the large installed base for automation and drives. Connected sensors have always generated data, but, unfortunately, that data hasn’t been used consistently to improve the plant reliability. Over the last 5 years the cost of computing power has decreased, allowing greater capabilities.
Remote connections require security. "I don’t think there’s any plant out there that hasn’t been hacked, whether they know it or not," Rao said.
Cloud-based data services
Plant-data services offer cloud-based data services, providing data analytics on all plant-machinery data dumped into a central repository, Rao continued. A connectivity model will be used so the data collection is device- and vendor-agnostic. The challenge is in having a legacy-installed base (dating back 30 years in some cases), which can create wells of disparate information. A cloud-based service can help collect, store, and analyze the data to provide intelligent information from customer data that previously provided little value.
In March, Siemens announced a partnership with SAP to provide cloud services on an open-source base. The next step is to create an application layer where tools and analytic technologies will reside. It will contain customer applications and Siemens applications, and will allow third parties to operate in the application layer in an open ecosystem. Pilot customers will be testing the concept over the next 6 months. The cloud-based services software was launched at the SAP Sapphire annual users’ conference in May.
November will be the official phase-one rollout, creating transparency for visual analytics. Phase two will contain more analytic applications.
Expected benefits include the ability to see data patterns that predict device failure so issues can be addressed before failures, which can provide root-cause analysis of failures before they happen. Patterns of data allow users to see correlations and how, in some cases, to prevent failures and downtime.
Another benefit will be optimization of plants by using operational data. Many control loops very rarely get tweaked as the plant evolves and grows. The open ecosystem will provide opportunities for vendors to provide software services and for customers to receive benefits, Rao said.
Greater connectivity, securely
By 2025, 80% of plants will be connected in some way; OPC Unified Architecture (UA) is one way for more effective information integration, Rao added, but a lot of work is needed since so many controllers are in locations where data sharing is impossible. Cellular and satellite connections will help with the most remote applications.
Once technologies are deployed, they have to be co-developed so every customer can adapt to domain knowledge of each industry for more effective implementation.
Automotive and mining are two industries interested in generating greater data flow while also ensuring cyber security; hacking into a paint booth or taking control of remotely controlled mining equipment would be large concerns.
Digital access, risk reduction
Business models are getting increasingly digital. Embrace automation and connectivity, advised Sivaraman. Cyber security reiterates the need to ensure compliance and safety. Many false dogmas surround the use of computers, Internet, and information.
Identify cyber-security risks based on business needs, plan mitigation, manage risks, and determine how the company will recover when attacked. It’s important to bring security features into products and use knowledge from working across industries. Perform a cyber-security assessment, implement mediation, and continue to manage risk.
Strategy partners can help develop a portfolio, offering knowledge and expertise. Siemens has one cyber-security center in Ohio and another opening in Portugal within a few months.
Knowing that viruses usually must travel through systems helps in understanding that cyber security is more than putting up a fence. Those involved must understand the ecosystem and monitor parts of the value chain, supply chain, and production systems to identify and mitigate real cyber threats. Data transparency means being able to react to an audit and continue with production. Substantial investments are needed so that can happen.
Often a response to an incident is a minor bandage. To increase resilience, a deterrent, denial, and detection are needed.
Closing the digital divide
The gulf is narrowing between information technology (IT) and the plant floor, and customers and partners need to work more closely to prioritize risk and move forward. Those on the plant floor often are unwilling to ask for the budget required to lower cyber-security risk if they don’t know what to do.
Rao added that solutions must be developed and prioritized from the plant floor with budgetary support from the top.
Sivaraman agreed that prioritization is key, and added that Siemens practices all the cyber-security advice it preaches, including embedding security into products.
"Businesses need to have cyber-security business processes," Sivaraman said. "Security can never be 100% fixed. I don’t think any business is not considering this."
Digital factory advice
Factory digitalization and big data analytics are within reach, according to Batra.
With a rapidly expanding number of connected devices (in less than 5 years, 80% of the world will have smartphones), manufacturers need to find ways to manage and drive better digital quality. Digitalization and big data are creating a unique moment; the good news is that much of the enabling technology is already in place, said Batra.
In an "Industrial Internet Insights" report from Accenture, 87% of industrial CEO survey respondents said big data analytics was among their top three priorities, but only 5% have big data strategy.
Morgan Stanley said $65 billion of automation system assets are reaching the end of life, and the average age of U.S. industrial equipment is the highest since 1938. Disturbingly, half of U.S. manufacturers become aware of a problem only after a breakdown occurs.
30% lower production costs
Digital factory tools offer up to a 50% reduction in time to market, up to a 30% reduction in engineering costs, and up to a 50% increase in throughput. Faster time to market is one of most decisive factors for business success. Control-engineering code has increased fourfold in a decade.
Tools available now can integrate, simplify, streamline, and speed processes, such as design and engineering, installation and commissioning, and operations and maintenance.
Discrete digital manufacturing streamlines product design, production planning, production engineering, production, and services. Devices such as power supplies can be connected to the network to monitor for pending failures and increase reliability, Batra suggested.
"No one is handing you the IIoT DVD. Those who start early have a first-mover advantage," Batra said.
Digital factory examples
Siemens, an early leader in industrial digitalization, has nearly 300,000 remote connections to devices through its service platform. Siemens services partners include Atos, McAfee, and SAP.
Batra said the benefits of using IIoT technologies are many, including the following:
- Wacker has 1,400 trained users and 4,700 piping and instrumentation diagrams. Plant engineers and plant operators can access Comos product design and simulation software data at any time, in real time, enabling informed decision making.
- Automobile manufacturer Maserati has a goal to increase production 300% by 2018 to 75,000 units, by integrating all production steps through a central data source. By using digital tools, Maserati output has tripled while maintaining quality.
- A Siemens plant makes 12 million programmable logic controllers (PLCs) per year for customers worldwide. Manufacturing execution systems gather 50 million pieces of process data daily, with defects at 12 per million—down from 500 per million in 1989.
But think again because digital manufacturing is not only automation, noted Batra; people matter. Employees generate 40% of the company’s annual productivity increases, he said.
– Mark T. Hoske, content manager, CFE Media, Control Engineering, [email protected].
Key concepts
- Manufacturing efficiency improves by using Industrial Internet of Things and Industry 4.0 concepts of digital manufacturing.
- Big data analysis and cloud services can help.
- Automation is important, but people also generate productivity increases.
Consider this
How can a more digital factory improve your efficiency?
ONLINE extra
https://www.news-sap.com/sapphire-now-sap-hana-cloud-platform-for-the-iot/
https://www.accenture.com/us-en/insight-ceo-briefing-2015-productivity-outcomes
See an additional story below about the motion controls inside Cirque du Soleil’s KÀ