Is the project that you’re working on making any money? Here’s a way to find out before it’s too late.
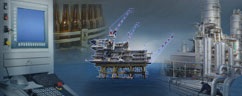
There is a scene in the screen adaptation of Ayn Rand’s “Atlas Shrugged” where a struggling businessman comes to speak with the protagonist, Hank Reardon, in his office and the following exchange takes place:
Paul Larkin: They say you’re intractable, you’re ruthless, your only goal is to make money.
Hank Rearden: My only goal is to make money.
Just so. We are in this business to make money. But that raises the question for us controls professionals: How do we know our projects are making money? It’s relatively easy to make the determination at the end of a project, but unfortunately, by that time it is too late and a project may have not yielded what was expected or, even worse, lost money. So the challenge is to monitor and direct a project during its execution so that small problems can be detected and remedied before they become big problems. That is where the concept of Earned Value (EV) comes in.
EV was developed and popularized in the 1960s by the Department of Defense for tracking projects in an attempt to identify and avoid cost and schedule overruns. The methodology was gradually adopted by different, project-intensive sectors of the economy and today is a key aspect of the Project Management Institute’s toolbox.
In a nutshell, EV uses the time-sequenced values of work that has been planned (PV), the work that has actually been executed (EV), and the actual cost of the work that has been executed (AC), to develop a set of indices that gauge how a project is performing from both cost and schedule standpoints. In a sense, these parameters ask, “Given the amount of work I had planned to complete by a certain date, did we get that work done, and how much did it cost versus what was expected?”
EV can be administratively complex, but fortunately we have computerized tools to assist with that task. My preference is to use Microsoft’s Project to facilitate my EV calculations. MS Project has a full EV engine programmed into it that makes extracting the necessary data quite simple. The best part of using an automated solution like Project is that not only are EV and its indices calculated for the overall project, but also for individual tasks. This is valuable for determining where a project that looks like it is going well overall may be coming off the rails in some underlying way.
When using Project for EV, it’s necessary to lay the groundwork properly:
1. Create an MS Project file for your job
2. Enter the time-sequenced tasks and dependencies into the Gantt table
3. Enter resources to be used into the appropriate table, along with costing information
4. Associate the appropriate resources with their tasks to generate task costs and planned values, and,
5. When the base project plan is complete, set the project baseline.
As the project progresses and work is completed or costs incurred, enter the actual hour and dollar values into their respective tasks. Don’t neglect to discuss task completeness with project team members. This will be important in projecting the final project schedule and cost.
To extract EV reports and data, simply set the project status date to the desired date (usually the current date). Then instruct Project to display the EV table of your choice. Three basic tables are available, an overview EV, a cost indicator, and a schedule indicator table. Summary tasks will roll up subordinate tasks, and if a project summary task has been created, the overall EV statistics for the project will roll up to that task.
The scope of possible reports that Project can generate is fairly broad and beyond the discussion here, but the data tend to be distilled into two primary indices: CPI and SPI, reflecting cost performance and schedule performance, respectively. A CPI greater than 1 indicates that the project is performing better than expected with regards to cost. A number less than one indicates the opposite. SPI is similar. In this way, lagging tasks can be singled out for corrective action without interfering with tasks that are performing well.
Find more on EV concepts at Wikipedia.
This post was written by Brad Ems. Brad is a senior engineer at MAVERICK Technologies, a leading system integrator providing industrial automation, strategic manufacturing, and enterprise integration services in the manufacturing and process industries. MAVERICK delivers expertise and consulting in a wide variety of areas including industrial automation controls, distributed control systems, manufacturing execution systems, operational strategy, and business process optimization. The company provides a full range of automation and controls services – ranging from manufacturing plant energy efficiency to data historians and continuous improvement solutions. Additionally MAVERICK offers industrial and technical staffing services, placing on-site automation, instrumentation and controls engineers.