Digital Edition Exclusive: Process information flow and plant efficiency improved when a glass manufacturer replaced an aging distributed control system with a plant-wide control system, according to system integrator RoviSys. The new system provides enhanced visualization capabilities on a common control platform, with better networking, a pair of redundant controllers for each of the five main process areas, advanced visualization, and alarming.
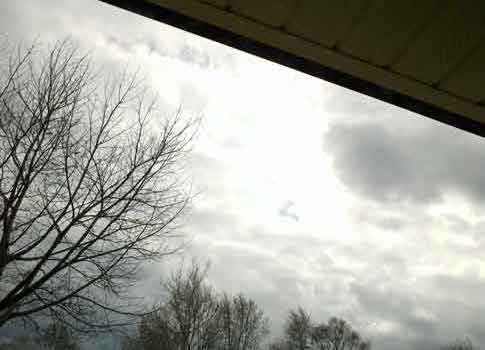
A residential window glass manufacturer has a furnace that runs nonstop at approximately 1600 C and requires nearly three weeks to reheat after shutdown. When it was time to replace the aging furnace refractory, the company also decided to replace its aging distributed control system (DCS), without extra downtime.
The original DCS was approaching the end of its lifecycle, and it lacked the functionality and visualization of contemporary distributed control systems. Not only was the existing system hampered by its closed architecture, obsolete hardware, and inability to integrate third-party components, but it also lacked advanced alarming and reporting capabilities. In a 15- to 20-year period, the plant has one window to undertake such a major upgrade project.
Nonstop since 1996
Operating continuously at extremely high temperatures can take a toll on glass furnaces—and on product quality. The plant’s natural-gas-fired furnace had been running nonstop since 1996 commissioning. As part of the aging process, the furnace walls were beginning to show signs of deterioration. The company decided to shut down operations to do a cold-tank repair, while replacing the plant’s original DCS.
For years, the plant had relied on drives and controls to manage cold-end processes, including the robotic movement of glass exiting the furnace. Plant engineers understood the advantages of expanding the control platform upstream by using a new process automation system on the hot end of the line.
New control system
Plant leaders were intent on gaining as much flexibility and functionality from their new control system as possible. The plant reported consistently positive experience with existing controls.
The project team worked with the automation provider to select a system integrator with glass-industry experience. RoviSys, based in Aurora, Ohio, with glass industry experience, met the project team to discuss objectives and then worked with the automation provider to develop a proposal and system architecture.
Functioning on arrival
After several months of engineering, a factory acceptance test was conducted at RoviSys facilities to ensure that the system would meet the manufacturer’s expectations. By the time equipment arrived on-site, the project team knew it would function as expected.
Within two days of shutting down and draining the furnace, the RoviSys team was at work commissioning the new process automation system. They followed up with system training for operators and maintenance personnel as well.
As part of the process, the project team worked with partnering automation suppliers to replace existing transmitters with new temperature and pressure sensors to provide seamless integration of the instrumentation new process automation system, easing implementation and maintenance.
The new system uses Ethernet switches to connect from the process system on the plant floor to the enterprise zone. Managed Ethernet switches at the control layer deploy standard, unmodified Ethernet and are designed to include many popular IT and control features for improved ease of use by the manufacturer’s engineers and IT professionals.
RoviSys networked the control system using a device-level-ring topology for coordinated control and data sharing between major process subsystems. The openness of the new control platform simplifies integration of third-party components and subsystems.
Within 90 days, the plant was up and running again, with the new system providing enhanced visualization capabilities on a common control platform. The system includes a pair of redundant controllers for each of the five main process areas.
Visualization, alarming
To meet the plant’s visualization and alarming requirements, the process system incorporates redundant human-machine interface (HMI) servers using thin-client technology for the operator workstations. The visualization solution provides enhanced alarming and diagnostics, and greatly improves the operators’ troubleshooting abilities. To increase system availability and maintainability, RoviSys virtualized all server applications.
During the shutdown, the plant replaced the drive system used to pull the glass ribbon from the furnace, upgrading to ac drives from Rockwell Automation and using EtherNet/IP (an ODVA Ethernet protocol) for seamless integration with the new system.
More info, easier troubleshooting
One priority for the project team was to provide operators with more detailed process information—something the plant can easily accomplish with the information-enabled process automation system. Production technicians and others were actively involved in customizing dozens of screens early on, gaining familiarity and confidence with navigation before the system was installed.
The new system provides detailed dashboards and production information. Plant operators now find it easy to access reports and troubleshoot real-time trends, including furnace temperatures, glass flow rates, combustion airflow, and batch status. The system includes change-management functionality that allows engineers to audit operator actions, which aids in troubleshooting system performance. The manufacturer believes it now has a world-class control room.
Advantages: flexibility, stability
The operations team expects that its new system will produce significant and measurable gains—including improvements in production consistency and energy efficiency. New, more advanced process controls bring needed flexibility and stability to plant operations. Additionally, engineering and maintenance people can easily diagnose production problems and get equipment back online quickly. In the plant and throughout the company, the consensus is clear: The new system provides a genuine business advantage.
– Keith Bagarus is director, global glass automation, RoviSys; edited by Mark T. Hoske, content manager, Control Engineering, [email protected].
Key concepts
- System integrator RoviSys helped a glass manufacturer replace an aging distributed control system (DCS).
- New system improves production consistency and energy efficiency.
- Advanced process controls bring needed flexibility and stability, with better diagnostics.
Consider this
Even if a dated existing DCS works fine, what operational advantages are unavailable?
ONLINE extra
This online version of a May Control Engineering Digital Edition Exclusive contains more information and a link below to: Products inside: Glass manufacturer improves process information flow