Each manufactured product has some impact on the environment and produces carbon emissions. Manufacturers are using obsolete equipment can reduce that impact.
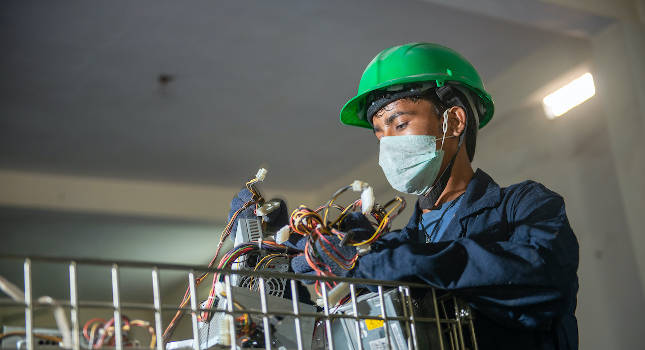
Learning Objectives
- Manufacturing sustainability is not only about carbon emissions, but also the use of rare earth metals that go into semiconductors and other products.
- Manufactured objects start as raw material and they give off a carbon footprint.
- Companies should reduce energy usage, incorporating carbon capture or carbon offsetting technologies into production processes whenever possible.
Every manufactured object started its life as a raw material. This could be a tree for wooden objects, or mined ores, quarried stones and extracted oils found deep underground. Resource extraction alone contributes up to half of all carbon emitted into the atmosphere worldwide. However, despite the impact resource extraction has on the environment, extraction companies are simply producing to meet demand.
Beyond extraction, the equipment used to process raw materials adds a large amount of carbon to the atmosphere through its own manufacturing process. Each component in a piece of industrial equipment comes with its own embedded carbon, which is the sum of the carbon emissions produced across the whole lifetime of the component. When considering the complexity of the average production line, it is easy to realize its amount of embedded carbon.
The problem with electronics
According to sustainability website Treehugger, two-thirds of the carbon emission of electronics can be traced to the manufacturing of storage devices, semiconductor and printed circuit board (PCB) components, which appear in many pieces of electrical and electronic industrial equipment.
Furthermore, the embodied carbon found in electronic parts and components used to assemble computer products account for nearly 60% of their total footprint. According to the same study, a further 40% is generated by the embodied carbon from various chemical, gases, metallic materials, and other semiconductor materials supplies.
Nevertheless, sustainability is not only about carbon emissions, but also the use of rare earth metals that go into semiconductors and other products. Some of these materials are scarcer than others, so overproduction of electronics diminishes the availability of these critical raw materials.
At the end of a product’s life, it is disposed of and more waste is created, which increases carbon levels. According to business website The Balance, an estimated 55 billion in e-waste material is thrown away each year in the U.S. alone. Similarly, only 20% of e-waste is documented to have been collected and recycled despite the potentially high reusability of materials like gold or copper.
Stepping forward: Reuse of electronics in manufacturing
From a manufacturing, repair or maintenance perspective — standing a few steps removed from the point of extraction — several actions can be taken to control the total carbon footprint of products and the emissions produced during production. These include reducing energy usage, incorporating carbon capture or carbon offsetting technologies into production processes and minimizing production waste.
Legislation is evolving to reflect the need for industrial businesses to operate more sustainably. For example, the European Union’s Emissions Trading Scheme (ETS) introduced a cap on the carbon emissions that companies can emit each year, with any excess emissions produced requiring the trading of carbon credits. This provides a financial incentive for manufacturers to minimize emissions.
On an equipment level, new European guidelines aim to reduce the waste generated by equipment that is still functional and compliant with energy specifications. From July 1, 2021, lower-efficiency — IE1 and IE2 — electric motors will no longer be accepted as a wider range of motors are brought into scope and held to higher standards.
However, there is one exception in regard to repairing products containing motors that were placed on the market before the new regulation came into force. This will avoid scrapping equipment early if motors can be repaired and is designed to avoid problems if it is impossible to replace a non-compliant motor with a compliant one without disproportionate costs to the end user.
Go green with obsolete parts to reduce industrial environmental impacts
One of the best ways to reduce environmental impact and increase sustainability is to assess whether a system needs upgrading. Manufacturers can be tempted to consider an upgrade just because older components have broken down and spare parts are hard to find on the market. However, upgrades should be deliberately planned according to a precise business growth strategy. It should not be commissioned as a way to bypass the difficulty of coping with obsolescence.
Like with new parts, each stockpiled obsolete part passed through the same environmentally damaging pipeline only to end up gathering dust in a warehouse. From there, the best outcome is they are scrapped and recycled, possibly straight into new parts to be stockpiled indefinitely.
This is unless they’re used. When faced with a part breakdown or end-of-life notice for a vital component, businesses can choose potentially expensive upgrades to the new models and systems with the prospect of repeating this process when the next end-of-life notice comes along.
A part may become obsolete for a variety of reasons, such as new specifications or regulations, changes in design, or because the original equipment manufacturer (OEM) stopped production to make space for a newer model. However, these parts might be still in stock somewhere in the world, so an automation parts supplier should be able to locate them.
Assessing whether these obsolete parts are workable in a system represents a two-pronged attack on potentially wasteful practices. First, if an obsolete part can be sourced, the demand for new parts is lowered. Secondly, using obsolete parts wherever practical makes the most of the resources, energy and associated carbon emitted in the original production of that part.
Claudia Jarrett is the United States country manager at EU Automation. Edited by Chris Vavra, web content manager, Control Engineering, CFE Media and Technology, [email protected].
MORE ANSWERS
Keywords: automation, green products, obsolescence
CONSIDER THIS
What steps is your company taking to reduce its overall carbon footprint