Industrial network assessments, tips, and advice: Is your legacy industrial network infrastructure ready for Ethernet, wireless, mobility, and other demands of today and tomorrow? Take this 4-question assessment, see 8 cabling issues, heed 3 implementation steps, avoid these pitfalls, and get help, if needed.
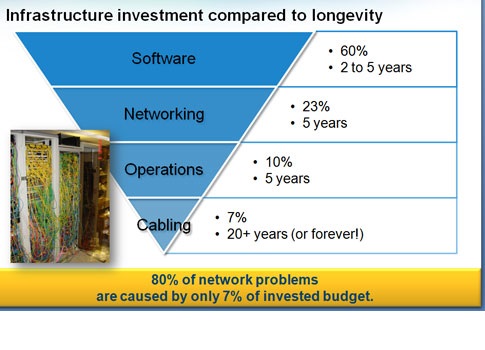
How strong is the industrial networking glue between layers of automation and controls and other parts of your organization? Is it ready for Ethernet, wireless, mobility, and other demands of today and tomorrow? An assessment can help with cabling issues and project implementation. Advice follows. In an automation project, "When it comes to design and deployment, the physical layer usually gets the least attention. The impact is often overlooked and severely underestimated," according to Andy Banathy, industrial automation solution architect for Panduit Corp.
"Consequently," Banathy said, "a significant portion of network downtime, approximately 80%, is attributed to physical layer connectivity." Causes can include a disconnect between the project lead and installer, pressure to get an installation done quickly and cheaply, changes or additions, and lack of attention to security vulnerabilities, he suggested.
Looking at typical spends for automation projects, Banathy said that software accounts for 60%, networking is next at 23%, operations 10%, and cabling infrastructure 7%. IT budgets typically prioritize spending on big ticket items like software and hardware with a very small budget percentage going to cabling. Cabling infrastructure material costs are low compared to hardware and software, but it can be very labor intensive with many possibilities for mistakes, Banathy said.
Also, he noted, because networking equipment is refreshed more often, "It pays to be forward looking when planning the cabling and connectivity planning for lifecycle as long as 20 or more years."
Assess network needs
Four steps for a physical network assessment: An assessment usually starts with the basics.
1. Count all the devices that need to be connected. This could be machines, sensors, controllers, cameras, drives, switches. Plan for today and for the next 20 years.
2. Then look at the network traffic volume, type like data, video, control, voice over Internet protocol (VOIP), and time criticality for process control. This will help determine bandwidth requirements.
3. Walk through the plant and envision how to run cable, consider how harsh the environment is, and see if there are any obstacles.
4. Work with manufacturing operations to establish an agreed-upon expected network availability. How critical is the network for operations? How much does downtime cost?
7 functional areas
In a physical infrastructure evaluation, Banathy said Panduit examines seven functional areas: thermal, grounding, rack power, pathways, labeling and administration, cabling, and racks and cabinets. Based on specific criteria from standards like Telecommunications Industry Association (TIA) and best practices, a 0-5 rating is applied to each area, where a 5 is best. For example, grounding can be a serious concern where racks are not bonded, disrupting communications.
3 implementation steps
Industrial network implementations go through three basic steps: assess, design, and deploy.
Assessment can include grounding, environmental issues, pathways, and power, among others. Network design elements include layout, programming, part selection, panel designs, cable routing, and others. Design deliverables include CAD drawings, bill of materials (BOM), and specifications. The deployment step includes installation, validation, testing, and training.
8 network cabling questions
There are eight questions to ask when considering network cabling, Banathy said.
- How much cabling is enough?
- Should we use fiber?
- What about electrical noise?
- Can the system handle the throughput?
- Is wireless an option?
- How can I control network access?
- How much downtime can I tolerate?
- How should I plan for the future?
Here are the pitfalls to avoid during a networking project, according to Banathy:
Don’t cut corners on documentation, especially for the physical network infrastructure. A complete set of design and installation documents is critical for success. Keep in mind future growth needs by thinking about what may be added to the network over the years. Investment in high-performance cable media pays for itself down the road, especially for expansion. The use of standards and reference architectures ensures optimal designs. Finally, think of what the installer needs to get the job done.
Look far and wide: Case study
When assessing industrial network needs, Dayan Rodriguez, global operations and business development manager for the consulting group of Rockwell Automation, had additional recommendations.
Examine the whole plant (from receiving, processing, and packaging to shipping) and the entire enterprise (from supplier to customers, from your one site to another), as well as goals and challenges (lower total cost of ownership, TCO, faster time to market, better asset optimization, broader risk management). Many of these issues can be addressed, Rodriguez said, by network convergence, "the ability to connect more assets and applications, be more highly integrated, and collaborate across boundaries."
For example, a global beverage company new product introduction required the design, development, installation, and configuration of manufacturing facilities, industrial control systems, and enterprise networks in multiple, geographical locations. Deadlines were established based on business impact factors. Facility construction issues caused unexpected delays. It also involved remote locations and extensive wireless infrastructure. The implementation included operational agreements between IT and production stakeholders.
Rodriguez said those working on the project developed network designs based upon the Purdue Model and vendor industry best practices employing zone and layer segregation. Additional help was sought for configuration of wireless and perimeter security devices. A core team of consultants rotated on- and offsite to ensure continuity of operations and support.
The application used a virtualized environment to maximize computing and storage capabilities in space-confined areas, Rodriguez said. The application used role-based, strong authentication using authentication services.
Results included cost savings for capital infrastructure investments and implementation levels of effort, layered, defense-in-depth architecture using zone segregation to ensure that vulnerabilities in certain zones do not proliferate into others. Ability was provided for logical storage array separation to avoid data comingling. Extensible architecture design allows for future integration of additional security products, Rodriguez said, such as centralized patching, security information and event management (SIEM), and intrusion detection.
– Edited by Mark T. Hoske, content manager, CFE Media, Control Engineering, [email protected], based on information in the June 11 webcast, "Let’s Get Physical – Building a Future Proof Infrastructure Foundation."
ONLINE
www.controleng.com/archives online for July has additional information and links with this article.
www.controleng.com/webcasts area includes multiple industrial networking topics.
Key concepts
- Legacy industrial network infrastructure or new installations need to be ready for Ethernet, wireless, mobility, and other demands of today and tomorrow.
- Assess networking infrastructure needs, looking at cabling issues, implementation steps, pitfalls.
- Case study provides network integration example.
Consider this
Can your network handle rapidly expanding communications needs?