I/O wiring can be among the most challenging (and perhaps feared) of upgrades. When replacing input/output connections, what are key considerations? John Lehman, Dataforth Corp. engineering manager, offered answers to some key questions.
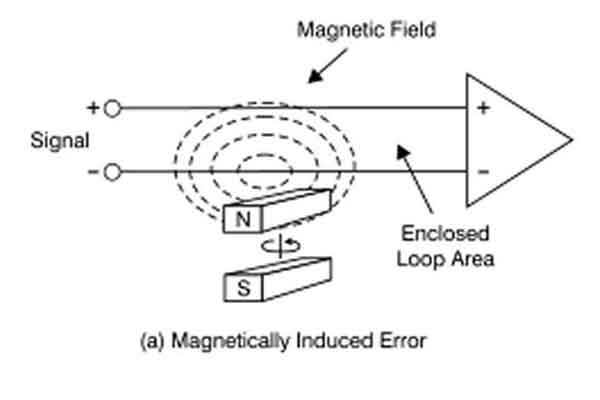
Control Engineering: When replacing input/output connections, what are key considerations?
John Lehman, Dataforth Corp. engineering manager: When replacing input/output connections, key considerations are grounding, shielding, use of twisted pair cables, cable spacing, bundling of signal and power conductors, appropriate wire gauge, insulation rating, proper wire routing techniques, hazardous location concerns, and wiring practices for system electromagnetic compliance.
Q: Is there documentation?
Lehman: Good installations and system designs will have thorough documentation on I/O connection and wiring requirements. Dataforth offers extensive information on I/O wiring to preserve signal integrity in a signal conditioning tutorial. https://www.dataforth.com/catalog/pdf/DTF-Tutorial.pdf
Q: What functionality do attached applications need to incorporate?
Lehman: The functionality that attached applications need to incorporate depends on system requirements. Using isolated signal conditioning products relaxes the many requirements of I/O wiring and solves many system wiring problems.
Q: What types of signals (analog, digital, serial, mixed…), what units (current, volts, resistance, ac, dc…), what range, and how many channels are needed?
Lehman: These are all important considerations for I/O wiring and are dictated by system requirements. Analog signals, digital signals, and power signals should be routed in separate bundles, or at least in separate twisted, shielded pair cables to preserve signal integrity. Channel input-to-output isolation, input-to-power isolation, and channel-to-channel isolation are also critical specifications of a good system design.
Q: What network protocols are required, and will they be wired, wireless, serial, digital, or a combination?
Lehman: The most common networking method remains TCP/IP. Modbus is still a prevalent and useful protocol. Wireless is making inroads into many industrial applications. Q: What are the sensing, signal conditioning, distributed control, isolation, and other requirements? Lehman: Modern sensors allow users to monitor more process variables than ever, which improves process efficiency and reliability and provides for better health-of-machine statistics, as well as prevention of downtime and accidents. Signal conditioning is an essential part of any system design as it provides proper scaling, filtering, linearization, and isolation. Microcontrollers, miniaturization of electronics, and wired and wireless networks allow more distributed control than ever. This expanded control, along with new opportunities in remote process monitoring, also supports more efficient, reliable, safe, and cost-effective systems.
Q: Will the application expand, and by how much?
Lehman: Good I/O wiring practices allow for easier future expansion.
Q: What design and how granular should the modules be?
Lehman: I/O wiring is an essential part of any successful system design and must be considered from the start of a project. Large systems, once wired, can be prohibitive to reconfigure.
Q: Will the I/O connections be enclosed or exposed?
Lehman: System requirements will specify whether I/O connections are enclosed or exposed. This is largely an environmental concern, but it is also important for operator safety and for applications in hazardous locations where arcing and sparking are not allowed.
Q: What are among the most-overlooked considerations?
Lehman: The most overlooked considerations are grounding, shielding, ground loops, capacitively and inductively coupled noise, and wiring practices for electromagnetic compliance (CE, FCC).
– Mark T. Hoske, CFE Media, Control Engineering, www.controleng.com, and John Lehman, engineering manager at Dataforth Corporation. www.dataforth.com