Soapbox: Don’t settle for faults inherent in PLCs and PCs. Take the best of each for a more effective hybrid system for process control, according to a software and hardware provider to the process industries.
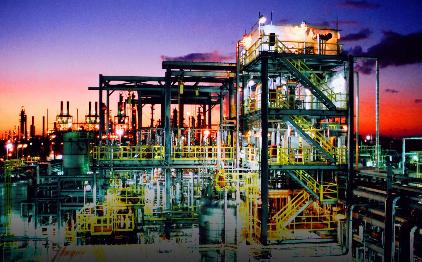
PLCs have been an old-time favorite for automation and control. The top-down programs and input-output type of ladder logic offered reliable control of process. However, with the ever-growing need for production information and quality control, the inadequacies of the PLCs were exposed.
Enter the PC as a tool for automation and control. The PC, with its user friendly operating systems, looked more like a candidate to displace the PLCs. However, the reliability of the operating systems left a lot to be desired. If working on a word processing document and the PC freezes, it is simple to hit the reset button. This, however, is not an acceptable solution when a PC-controlled machine is reaching dangerous operating conditions. Hence the PC is not an answer for process control.
The PLC is inadequate when complex mathematics is required. PLCs do not handle image analysis well either. Even process control like temperature and pressure are not well handled by PLCs where high levels of accuracy are needed. This kind of temperature and pressure control is better left to intelligent field devices like dedicated temperature or pressure controllers. Recently PLCs have been benefitting from special process control modules that may be added to PLCs. One thing that PLCs do very well is discrete control like opening and closing valves. PLCs have been fairly efficient in positioning for robotics.
In short, the question is how to integrate the reliability of the PLC’s discrete control, the precise control of intelligent field devices, and the processing power of the PC. The obvious answer is a hybrid system with the PC as the supervisory device with delegated controls to the PLC and other field devices.
All calibration, data analysis, and data history are handled by the PC. The human machine interface is provided by the PC. Actual process control is carried out by the PLC and the field devices best suited for the application. With the advent of interdevice communication capabilities, hybrid control systems are more popular than ever.
This way the best capabilities of all the devices are safely leveraged for the best results. This model also lends itself to cloud-based remote control or data acquisition.
– Jacob George is application engineering manager at Turbomation, a company engaged in engineering and automation consultation for process control. Edited by Mark T. Hoske, CFE Media, Control Engineering, www.controleng.com.
www.turbomation.com
https://www.controleng.com/process