Technology Update: Putting Ethernet over RS-485 resolves product obsolescence issues and rapidly migrates fieldbus infrastructure to Ethernet, extending usefulness of a variety of end-of-life products.
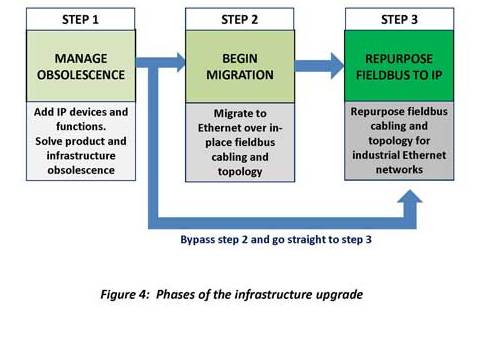
Facilities managers face end-of-life (EoL) hurdles in industrial control infrastructure due to product and network obsolescence. Faced with product discontinuation, and operational or regulatory challenges, there are daily choices between a variety of patchwork solutions to correct point problems, or invest capital budgets to overhaul infrastructure.
Ethernet can be run over existing networks to enable the:
- Replacement of obsolete products with new Ethernet products in fieldbus infrastructure
- Migration of legacy fieldbus network segments to Ethernet
- Transformation of entire fieldbus networks to Ethernet.
This can be achieved without adding new structured cabling or impacting active fieldbus operations. This can be done by re-purposing existing fieldbus wiring, replacement of RS-485 based, migration from legacy serial devices to their Ethernet counterparts, and implementation of Internet protocol (IP) into the legacy infrastructure, avoiding a rip-and-replace strategy.
According to a recent IHS research report, “Industrial Ethernet and Fieldbus Technologies – World – 2013,” while the total number of network nodes to be installed will increase by more than 30% between 2011 and 2016, the mix between fieldbus and Ethernet products over the years remains relatively unchanged, growing only by 3 percentage points from 23% to 26%. A primary reason for the muted growth in the industrial Ethernet market segment may be that facilities managers lack a cost-effective and risk-free strategy for the transition of fieldbus infrastructure to one based on Internet protocol and are only adopting the latter when they have green-field opportunities. With the cost of structured cable running around $50 per meter on the factory floor and an order of magnitude higher in environments such as automotive manufacturing facilities, putting Ethernet over existing network infrastructure becomes a key to accelerating the adoption of Ethernet in industrial networks.
There are three main barriers against ease of adoption for industrial Internet connectivity, and each represents a distinct challenge for network management.
1. First, in dealing with obsolescence (Figure 1), one must consider that legacy environments have been operating for decades with serial systems interfaced to their respective fieldbus infrastructure. A number of these systems are facing discontinuation by suppliers, and the only remedy possible is a replacement with refurbished units on the gray market or a new generation of IP products incompatible with the existing network. Solutions can integrate new IP products (Figure 1A) onto legacy infrastructure and retain all native serial systems and fieldbus functionality.
2. The next logical step is to repeat the strategy to systematically replace other serial devices with IP products as needed. This enables the phased transition from a reactive remedy to obsolescence, to a proactive program of migration (Figure 2) that allows the network to constantly upgrade over time as budget and functionality requirements dictate. It is possible to manage and transport simultaneous serial and IP traffic on the same physical infrastructure.
The end game for facilities managers is to migrate to IP products in a modern open standard network infrastructure. Each step in network migration brings a repurposed (Figure 3) infrastructure closer to this reality, where the fieldbus network supports the transition to IP functionality and provides all of the benefits of the latest generation of IP products. This can be achieved without the costly rip-and-replace of the copper infrastructure normally required to upgrade to a 100% IP environment.
Installations can start with solving obsolescence by using Ethernet over existing networks, then repurpose the network cabling infrastructure to IP only, eliminating the second step of the migration of intermixing serial, as shown in Figure 4.
Put Ethernet onto other networks
Technology can enable the simultaneous transport of IP data and serial data over the same wiring infrastructure, such as twisted or untwisted pair(s), even in the presence of significant conducted and radiated noise in the medium. Figure 1 shows how these products may be installed in a typical legacy industrial network to deal with product obsolescence and network migration. At the head end, the legacy master controller is connected to the RS485 port of a one-channel server.
In addition, an Ethernet master or panel may also be connected to an RJ-45 port. This enables simultaneous transport of the serial (Modbus, Profibus, DeviceNet, ControlNet, Data Highway, etc.) and Ethernet data on the proprietary bus established at the output port. With the server in place, up to four clients may be connected to each single channel server. Each client accepts information from the private bus as input and routes the serial communication to its RS485 port and Ethernet communication to its RJ-45 port. They do not generate traffic; they only manage data transport. Legacy PLCs may then be connected to the RS485 port, while IP-PLCs could be added through the RJ-45 ports. In this manner, individual legacy PLC products may be replaced, or entire network segments connected to remote I/O points can be changed to Ethernet. The architecture described in Figure 1 may be applied to industrial networks with DeviceNet, ControlNet, Profibus, Modbus, Sercos, or other legacy products.
How to deploy
Projects can replace an individual obsolete controller or involve a phased changeover of entire network segments. Using products that put Ethernet over networks such as RS-485 offers a simple, straightforward approach to modifying an existing network infrastructure. Replacement of individual PLCs requires only the integration of one server product where the master controller of the network segment is located, and the client product at the location of the replaced PLC product.
With these steps, product replacements are essentially complete. For migrating entire network segments, integration of the server at the head end would be followed by the integration of a client at each of the locations where legacy PLCs are replaced with their IP counterparts. From a project perspective, the deployment typically requires a site audit prior to the completion of network design, and basic electrical and PLC/SCADA programming skills for product deployment and test. Site audits are recommended to obtain and understand basic information about the legacy infrastructure, including the make and model of existing master controllers and PLCs, wiring types, termination conditions, bandwidth, or data rate requirements, wire lengths, and wiring topology.
While the basic network design presented in Figure 1 remains unaffected by the information obtained during the audit, it is critical to in-situ network testing and validation of the product deployments.
Return on investment
The technology enables rapid transformation of legacy networks to IP and has thousands of deployments in operation, with more than 1 million hours mean time between failures (MTBF). The value proposition of Ethernet over RS485 products is significant and involve+es reduced project time, cost, and complexity, with negligible impact to ongoing operations and revenue collection. As an example, in the retail petroleum market, IP upgrades on the forecourt used to involve construction, permitting, projects costs of a hundred thousand dollars or more, resulting in service station shutdown for weeks.
Putting Ethernet over existing RS485 wiring+, the job can be completed without construction requirements, for less than $10,000 in less than two hours. In industrial networks, it eliminates the need for tens of thousands of dollars in cabling costs alone. In automotive environments, the overall cost savings could be an order of magnitude larger. In addition to the cost, risk, and downtime advantages, there are other intangible benefits. Facilities managers can develop a structured way to integrate parts of their industrial network with the corporate IT infrastructure. In the meantime, they can begin to integrate the data across the two networks using gateways. And finally, staff re-training needs are substantially reduced and more manageable by putting Ethernet over existing industrial networks across the factory.
Industrial integration
Resolving product obsolescence in this way enables network migration to IP at significantly lowered cost and technical risk. This value proposition has been demonstrated in a variety of markets through Ethernet over RS485 product integration, and adoption in industrial environments is ramping up. To facilitate easy access and integration for automation and control installations, channel partners can offer industrial domain expertise and distributor relationships. As facilities and installation managers rapidly migrate networks to IP over existing network infrastructure, the market will increasingly favor use of Ethernet over fieldbus products in brownfield applications.
– Dave Karpenske is chief operating officer at PCN Technology Inc. Edited by Mark T. Hoske, content manager, CFE Media, Control Engineering, Plant Engineering, and Consulting-Specifying Engineer, [email protected].
ONLINE
www.pcntechnology.com
PCN Technology Ethernet over RS-485 networks can be added to many fieldbus operations including DeviceNet, ControlNet, Seriplex, and others.