Control Engineering international: Use of the Internet with manufacturing has evolved for more than 10 years and continues with advancements in industrial cloud, Industrial Internet of Things (IIoT), and Big Data to support enterprise and production activities, as manufacturing upgrades progress, explained Mitsubishi director Nan HeHao to Control Engineering China.
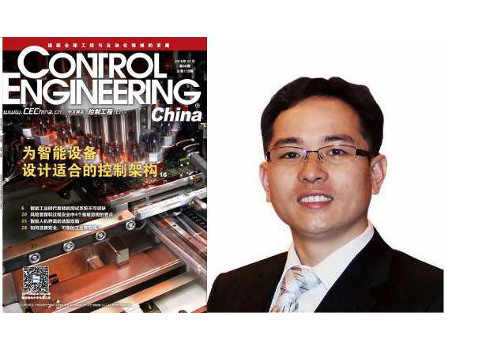
The tide of Industrie 4.0 with intelligent manufacturing at its center is sweeping global manufacturing. The Chinese government is making efforts to boost and upgrade the transformation with integrated development of manufacturing and the Internet. As a factory automation manufacturer, what will Mitsubishi Electric do to realize the future "Intelligent" manufacturing? At the recent "Industrial Automation and Standardization" seminar, Control Engineering China interviewed director Nan HeHao of the e-F@ctory Promotion Department of Mitsubishi Electric Nagoya Laboratory.
Manufacturing intelligence, 3 layers
Industrie 4.0 has not been clearly defined by many experts and manufacturers. According to HeHao, Mitsubishi Electric has centered its understanding of Industrie 4.0 with intelligent manufacturing. The intelligence should be in mass production of the manufacturing site and extended and optimized through the industrial value chain.
HeHao said manufacturing intelligence includes three layers.
- Intelligence- and information-based capabilities should extend beyond manufacturing to higher level systems.
- Beyond mass production, coordination is required through the entire business flow and system from design through mass production.
- More than within the company, intelligence-based and information-based operations also should include suppliers and contractors qualified to participate in supply chains.
HeHao also advised on the implementation of intelligent manufacturing. He said: "Before the implementation of intelligent manufacturing, first, the purpose should be clarified: improving productivity, enhancing production quality, or lowering the production cost. Intelligence cannot be made just for the purpose of intelligence." HeHao said Mitsubishi can offer technology for full production line automation, but automation and robotics may not suit all processes. Sometimes human-assisted operations may better fit the application; designs and associated costs should meet the identified needs.
Available technologies
Mitsubishi Electric offers technologies for realizing all three layers of manufacturing intelligence. Information can be shared seamlessly between the production site and upper systems. According to HeHao, different information is required for different layers in the production site and IT systems (such as production management and business support backbone systems). Especially on the IT system side, data required usually is not the same as production equipment data. Instead, summarized data is required based on units, such as production lines or entire factories.
With Mitsubishi e-F@ctory solutions, information sharing groups for the intermediate layer (factory automation and information technology) bridge the production site and the IT systems.
For the second layer, from design to mass production and then to business flow and system sharing, HeHao said setup tools include computer-aided design (CAD), computer-aided manufacturing (CAM), computer-aided engineering (CAE), simulation software, and analysis tools. The universal interface platform EZSocket from Mitsubishi connects software tools, allowing easier sharing of data between tools or between equipment and software tools, which can greatly improve the design efficiency of each link of the engineering chain.
For the third layer, HeHao said that extending overall intelligence beyond the company involved requires attention to all parties in the manufacturing value chain, such as the equipment manufacturers, design software manufacturers, and system integrators. And intelligence and digitalization should be extended to supplying manufacturers. The Mitsubishi Electric e-F@ctory Alliance partnership program, by summer 2016, included approximately 3,320 corporate partners. That program began in 2013 with initial focus on visualizing data at the production site.
"With the continuous development of e-F@ctory for several years, we’re heading for the effective utilization of the collected visualized data," which HeHao called a "perfect match for Industrie 4.0."
The e-F@ctory requires sensing of site information, data collection and analysis, transmission based on an interlinked network, and coordination of upper-level systems, such as the cloud, manufacturing execution systems (MES), and enterprise resource planning (ERP). These efforts fit with the trend to integrate "Made in China 2015"and "Internet +" initiatives from the Chinese government. HeHao said the efforts will bring about a new generation of intelligent manufacturing by coordinating the digital space, machinery, and human activities.
Mitsubishi e-F@ctory efforts continue to evolve and use advanced technologies such as cloud, IIoT, and Big Data to support the enterprise activities and production activities and joins with China in upgrading and updating all aspects of the manufacturing industry, HeHao said.
Stone Shi is executive editor-in-chief, Control Engineering China; edited by Mark T. Hoske, content manager, Control Engineering, CFE Media, [email protected].
ONLINE extra
See additional stories from Control Engineering China linked below.