PID controller tuning is a keystone skill for control practitioners that is often given short shrift. What is the justification for investing in this critical skill? Why tune control loops?
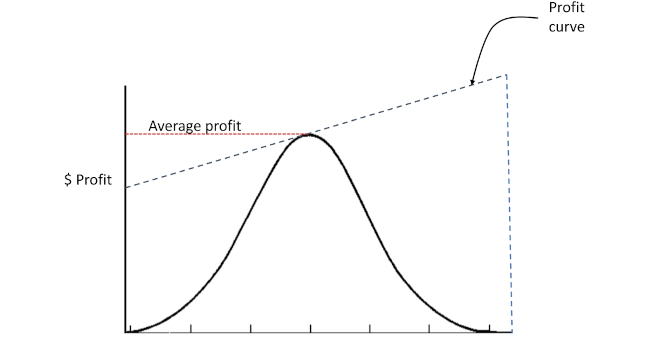
Learning Objectives
- Understand that properly tuning PID controllers will enhance the safety and profitability of any process where they are applied.
- The demand for proper tuning has increased because controls have gotten more complex with time and that process operators are expected to monitor more PID controllers. Practices that were accepted 20-40 years ago are no longer acceptable.
- Improving process profitability requires a two-step procedure; reduce variability (of which loop tuning is a major component) and then pushing process limits.
Why tune PID controllers insights
-
PID controllers need to be customized for the process they are controlling (tuned).
-
Tuning all loops well is required to help process operators run their processes safely and profitably; not tuning loops properly costs money.
-
Modern refineries (and presumably all other process industries) are adding scope and complexity to the process operator’s job, requiring automation professionals to do a much better job providing properly operating, properly tuned controls.
The simple answer for why it’s necessary to tune control loops is because different processes respond differently. Flow loops respond quickly and therefore need a fast-responding controller. Temperature loops respond slowly (usually) and therefore need a slow responding controller. The proportional-integral-derivative (PID) controller is a near universal tool for controlling processes, but it needs to be fitted to the process. Fitting a PID controller to the process is called tuning.
Why does PID controller tuning matter?
PID controller tuning matters. Process control, and appropriate PID tuning, is about:
-
Safety, first and foremost
-
Equipment protection, safety’s little brother
-
Efficiency of the process.
Efficiency of process has several benefits of its own, which can be further divided into:
-
Higher yields from the process
-
Less waste
-
Better energy efficiency.
Expanding scope, expanding complexity of process control
Early in my career the typical process control operator was expected to watch between 100 and 200 PID controllers. A process control operator also didn’t have advanced process control (APC) applications to watch or safety systems. If safety systems existed, they were generally based in the field. Compressor surge controls were provided using specialty packages that also were field mounted.
In short, the process control operator wasn’t, by today’s standards, expected to watch much.
In the intervening years (the many intervening years), a great deal of complexity has been added to the process control operator’s responsibilities. Today’s process control operator is expected to watch up to 500 PID controllers along with safety systems, compressor control systems and APC applications. The controls applied to process units are also far more complex, featuring multiple levels of cascaded loops and other complex logic.
Control professionals have made great strides putting better graphics in front of operators and also not flooding the room with useless and confusing alarms. This was all necessary, but not sufficient. Simply stated, the process control operator can no longer be expected to work with controls that are not functional. Good controller tuning is no longer optional.
Think of this another way: In the days when a process control operator was expected to watch 100 PID controllers he could handle (let’s say) 30 poorly performing controllers (30%). The operator had the time. If we have 30% of 500 PID controllers performing poorly – 150 controllers – the process operator no longer has the time to watch all of these closely. It has become much more important for the control professional (you) to ensure that all process controllers work properly.
Properly tuned loops create money, money and more money
For most chemical processes maximum profitability usually requires operating against process constraints. These will include product quality limits (such as purity), unit operating constraints (such as distillation tower flooding limits), and equipment limits (such as motor amps on pumps and blowers). There are usually severe penalties for exceeding these limits (such as off-specification product that cannot be sold or equipment trips [and the process upsets that follow]). For those who work with exothermic reactions failure to control the process within limits can result in unplanned disassembly (also known as “spontaneous disassembly.” No one wants either.)
In process plants with poorly tuned control loops, or worse yet, controls left in manual because they cannot be trusted, operators tend to operate the process far from limits. This leaves considerable profit on the table. The typical situation looks like Figure 1.
The bell curve represents the normal distribution of the process data. The tail of the bell curve is set to end just below any process limits, the nearly vertical dashed blue line on the right. The profit curve is the dashed blue line across the top. The theoretical maximum profit is at the top right corner where the profit and process limits lines cross. However, to avoid violating limits, the process is operated far from the limit, and thus the average of the process data is considerably to the left of the maximum profit point. The process is making less money than it could.
To make more money, the process needs to change to squeeze the bell curve to get the right end of the curve away from the process limits, and then the whole curve needs to move to the right so that the end of the curve is where it began. When that’s completed, the result is Figure 2.
The blue bell curve is narrower, and the curve moved so the right end is close to the process limits. The new profitability is now higher than it was before.
The manager-friendly way to say this is that proper tuning delivers:
-
Reduced variability and
-
Pushed constraints.
Many say that reducing variability alone will improve profitability. This is not generally true (unless you are doing something terribly wrong). Improving profitability requires that the process be pushed closer to constraints. A process can vary very little as still be well away from the desired optimum.
Unfortunately getting operators to push constraints is the hard part of the control professional’s job. Operators are (properly) skeptical of bright young engineers telling them they need to do something that they know runs the risk of making their jobs harder. However, operators are willing to work with engineers that are open and honest about what’s proposed. Prior victories can add credibility. Operators need to believe their jobs can become easier – or at least not harder.
A personal story about value of loop tuning in a refinery
A former boss recently told me, “What I learned from you is how much free money is laying around a refinery.” He followed up with a story about the value of loop tuning. While I was working for him he had been asking the vice president of refining for a new wet gas compressor for the refinery’s fluid catalytic cracker (FCC). My boss was hoping to increase charge by about 20%.
The vice president said no.
In the meantime, I was busy tuning and cleaning up the controls, and the process engineer was working with the operators to get them to push the FCC to its limits. Over a couple of years, we got the charge rate up by about 20%, at which time the vice president told my boss “See; I saved the company money.”
This story was repeated across the refinery, although never this dramatically. We had put in a new control system, fixed a lot of instrumentation and valves and tuned controllers. Work included installation of advanced process controls (at that time) and fix some basic controls that were just wrong. For the most part, refinery process improvements came down to reducing variability, tuning PID controllers and getting the operators to push the limits. Improving control loop tuning was at the core of it all.
What’s next for this PID controller tuning article series?
This is the first in a series of articles on PID controller tuning aimed at new practitioners. The next few articles are going to be brutally basic. Experienced readers may pass these by, but I hope you will take a look as a refresher on PID control. There may be some tidbits on PID stated in a way you or co-workers will find useful. Later articles will focus on practical concerns (all the things they don’t teach in college) and how to tune quickly and efficiently (because you have about a million other things to do).
This PID tuning series is not a math class
For those of you that have taken a college process modeling and control class, you have my deepest condolences. Successful controller tuning rarely involves LaPlace transforms, left hand poles (or was that zeros?) or any form of Bode plot. These can be useful things to know, but you can tune 99.9% of loops without this knowledge.
Tuning is as much art as science. The overall goal of this PID tuning series is to provide an intuitive feel for getting the best possible performance out of process controls. I teach (and use, often in combination) open, closed and heuristic tuning methods, but always with the admonition that these methods yield approximate answers. The real answer depends on what the process needs, how close the process is to “ideal” (whatever that means), and what is around the process. This means that after using a tuning method,tuning constants may need to be carefully adjusted (fudged is the technical term) to get the exact performance needed. This can only be done after acquiring an intuitive feel for how changing controller gain, integral or even derivative affects controller performance. That intuitive feel is what this PID tuning series aims to provide.
Ed Bullerdiek is a retired control engineer with 37 years of process control experience in petroleum refining and oil production. Edited by Mark T. Hoske, content manager, Control Engineering, CFE Media and Technology, [email protected].
Editor’s note: Ed Bullerdiek is working on a yearlong series, including a webcast. Each post will link to prior articles in the series. This is part 1.
CONSIDER THIS
By not effectively tuning control loops, how much money are you wasting?