Millennials are realizing manufacturing’s potential as a career with the advent of smart technology; companies can leverage technology use to attract them.
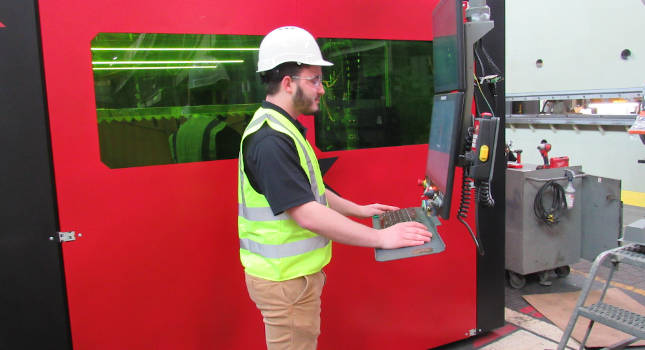
Learning Objectives
- Using real-time data from the manufacturing floor does more than reduce waste and increase efficiency.
- Manufacturers should provide clear pathways for career progression with customized training for industry specific skills.
- Advancement and networking opportunities help manufacturers acquire and retain talent.
The manufacturing workforce is changing, with more than 2-million existing workers set to retire within 5 years while more than 2 million manufacturing jobs are being created in the same time frame. Without a change, the manufacturing industry is looking at a 5-million-person job deficit by the end of the decade. As a result, manufacturers must look for innovative ways to attract millennials, who are the largest group of workers.
They are technology savvy and often socially conscious individuals who may not see manufacturing as a good career for them. Many millennials view manufacturing as a field without the purpose, vision and leadership they are looking for in a career.
However, with manufacturing modernizing, millennials are beginning to be attracted to manufacturing jobs that have smart technology and opportunities for advancement and networking. Manufacturing executives and operators can attract millennials with these three strategies.
1. Add, upgrade manufacturing technology
Using real-time data from the manufacturing floor does a lot more than reduce waste and increase efficiency. This technology can help fill labor gaps to bring employees a greater work life balance and can reduce mundane tasks like manually writing data points. Technology enables mobility since employees can check in from home or set up automatic notifications if they want to be kept up to date with a process. Automating processes with technology also can assist with the critical industry knowledge that is leaving manufacturing with retiring employees.
Older employees may have been used to calculating scrap from manual processes, but an Industry 4.0 solution could place sensors on existing machinery to capture data for real-time analysis. Modern employees should thrive with this type of solution. This ends up saving time for employees and money for the manufacturer.
2. Opportunities for advancement in manufacturing
Manufacturers should be upfront to employees providing clear pathways for career progression with customized training for industry specific skills. Millennials want meaningful work that contributes to the success and value of the company. Even motivated employees can feel frustrated at stagnant jobs without clear opportunities for internal advancement. Industry 4.0 solutions can bring these opportunities through tech-savvy roles which should bring less employee turnover.
Manufacturers can help employees move on to supervisory roles like an area manager or more technology-based roles like a quality control inspector that could use internal real-time data analytics to track waste from production while finding ways to prevent it. Company specific training gives employees opportunities for growth in the reinvigorated field of manufacturing.
3. Smart manufacturing: Build a successful foundation
Manufacturers should encourage younger employees to attend workshops, executive forums, and to be on the look-out for ongoing education opportunities. At a recent executive forum hosted in Cleveland, the hosting company invited speakers to highlight their commitment to smart manufacturing initiatives for mid-sized manufacturers across the United States, bringing Industry 4.0 knowledge to a new generation of workers. This is a great way for companies to put a story and a face to the narrative and show the opportunities manufacturing can bring.
An eye toward future-proof manufacturing
The perception around manufacturing has been moving in a positive direction but there is still work to be done. According to a Deloitte US study, 67% of Americans believe a career in manufacturing can be rewarding and are more likely to speak positively to children about a future career in the industry. In addition, manufacturing reshoring efforts are being supported by the United States government as a tentative solution for supply chain woes.
If manufacturing processes rely on smart technology instead of gated internal knowledge, this can guard against employee turnover to help “future-proof” factories while providing opportunities for employee growth. Providing this room for advancement and networking opportunities will help manufacturers acquire and retain talent.
Terri Ghio, president of FactoryEye North America. Edited by Chris Vavra, web content manager, Control Engineering, CFE Media and Technology, [email protected].
MORE ANSWERS
Keywords: automation, workforce development
CONSIDER THIS
What plant-floor upgrades are attracting your next-generation workers?