There are no widely adopted business and technical standards for the system integrator industry, so setting benchmarks and selection criteria can help you sleep better with the decision.
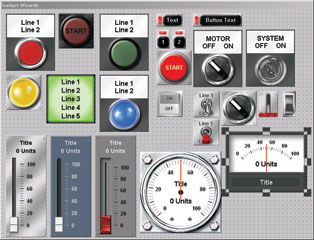
Think you’ve done your due diligence in selecting the best integrator for your next control systems project? Picking the right system integrator can be a mission-critical decision. In a tight economy, businesses cannot afford to travel down a project path saddled with mistakes, delays, miscommunications, and cost overruns. Plus now in our highly connected business environment, your choice of a system integrator can cascade—for good or ill—via social networks to impact the brand reputation of integrators and their customers as well as the global chain of partners, vendors, suppliers, distributors, and end users.
3 fundamental criteria
A decision needs to be based on the sound business fundamentals of technology expertise, industry experience, and best business practices. If an integrator is missing one of the three fundamentals, you probably will not have a good fit for a project. One of the challenges in selecting the right system integrator is the broad definition that is often applied to the industry regarding specialization and expertise. Some professionals focus on specific related tasks, such as programmable logic controller (PLC) programming, configuring sensors, and building system control panels. Others offer a full range of hardware and software support, from installation, configuration, and programming to complex, higher-level systems development in the realm of enterprise resource planning (ERP) decision-support platforms. For the customer, the challenge is whether to engage with a generalist firm offering a broad menu of services and wide systems expertise, or a specialist with highly developed skills in specific technology solution sets, such as HMI programming or SCADA control system support. A specialist may not always be able to deliver a wider range of experience when needed. The recipe for trouble always occurs when a specialist offers to solve a manufacturing execution system (MES) or other advanced technology issue without a track record of working with complex industrial control systems.
Unfortunately, there are few industry standards or benchmarks to help customers with the decision-making process. Some companies rely on the ISO 9001 certification, which reflects a global standard for consistency in business processes. But there’s no guarantee that an ISO 9001-certified system integrator uses business processes that result in successful automation projects. Other companies tap internal expert resources or outside technical consultants to establish selection criteria and technical guidelines as well as participate in the business review process. Or they have an established vendor request for proposal (RFP) qualification process, with requirements for candidates to address questions on business and technical capabilities.
Industry benchmarks
Early on, the Control System Integrators Association (CSIA) established a certification program to offer an industry standard for best practices and business benchmarks. Setting guidelines, criteria, and benchmarks can go a long way in helping a company address many issues and concerns involved in the control system integrator selection process. Ultimately any set of criteria can’t offer an absolute guarantee of success, but relying on a consensus of industry expertise coupled with a diligent in-house review process can ensure a good outcome with minimal risk.
It’s important to stress that selecting a system integrator is more than a technical capabilities decision. Acquiring a technology service is different than buying a commodity. Though not always covered in the selection process, criteria that should be considered include business development and human resources management, marketing, financial management, project management, and system development, as well as life cycle, quality assurance management, and service and support management.
Without reliance on some form of industry guideline, such as the CSIA Certified integrator program or a structured RFP audit process, most customers probably will not ask all the right questions. For example, key questions that are not asked focus on the topics of disaster recovery and computer systems management. If the system integrator’s building was destroyed as a result of fire or natural disaster during the course of the customer project, how quickly could the project resume? For computer systems management, what kind of security is in place and is all of the software managed properly in terms of licensing? Does the integrator have a plan for loss of senior management as a result of position change, retirement, or personal accident? A good integrator needs to deal with all of those, but does the customer think to ask those questions up-front?
When failure is a factor
Failure may not be an option, but it happens. Unplanned downtime or project interruptions are often not factored into the equation, and the customer needs to plan for such worst-case scenarios. What if a project goes south and the integrator has to be replaced halfway to completion? Many projects fail simply because the system integrator didn’t require a quality functional requirements specification from the customer or the integrator did not write a good functional specification at the outset. Both parties proceed with the project making design and development assumptions along the way. Nobody’s on the same page. The result at the end of a project is directly related to the comprehensive pre-planning phase and the written technical specification set at the beginning of the project. If you didn’t do a quality start, you’re not going to get a quality end.
Pre-planning includes identifying all risks to project success. It’s the job of the system integrator to identify any pitfalls in the customer objective before project initiation. If no risks are cited, that shows inexperience or an integrator fearing pushback from the customer. A no-risk project assessment is a red flag in the integrator qualification process.
The top 10 key guidelines for making the right system integrator decision for a project follow.
- Match the technical sophistication level of the system integrator with the complexity of the project. If the integrator “offers” to tackle issues outside of the company’s business domain, be cautious.
- If you don’t have in-house expertise for making the integrator selection, consider hiring a third-party technical consultant to establish selection criteria and/or participate in the review process.
- System integration is a people business. Does the system integrator have a satisfactory human resources program, in compliance with all applicable state and federal laws? Is there a focus on development, training, recruitment, and retention?
- If the system integrator relies on subcontractors, review the systems deployed to monitor and control workflow.
- What are the risks of the project? Are you prepared to manage those risks?
- At the conclusion of the project, what kinds of training documentation, manuals, and records will be included as a project deliverable?
- At the outset, establish the strategic objectives and goals of the system integrator. Are these goals and objectives in line with the mission of your business?
- Will you get along? Establish criteria for assessing the business culture of the system integrator. Does the integrator respond in hours or days to requests? When do casual discussions turn into consulting charges?
- Meet with your integrator’s project team before documents are signed. It’s important to have a good relationship with your day-to-day contacts, in addition to the managers.
- Keep up-to-date milestone records during the course of the project. If you have to replace an integrator, refer to the specification and decide on a fair settlement covering payment for all completed deliverables.
While there’s no one right way to select a system integrator, you can be reasonably assured of a good outcome by doing your homework and incorporating established selection criteria templates and industry benchmarks. Most important, you are going to make a business decision, so remember to compare notes on how you and your system integrator see the bottom line.
– Robert Lowe is executive director of the Control System Integrators Association (CSIA); John Weber is president of Software Toolbox. Edited by Mark T. Hoske, content manager CFE Media, Control Engineering, Plant Engineering, and Consulting-Specifying Engineer, mhoske(at)cfemedia.com.
https://www.softwaretoolbox.com
ONLINE
https://www.controleng.com/integrators, the Control Engineering Automation Integrator Guide, offers a multiparameter search function to help narrow the field.