The manufacturing workforce is changing and companies can benefit from workers that are better connected and prepared.
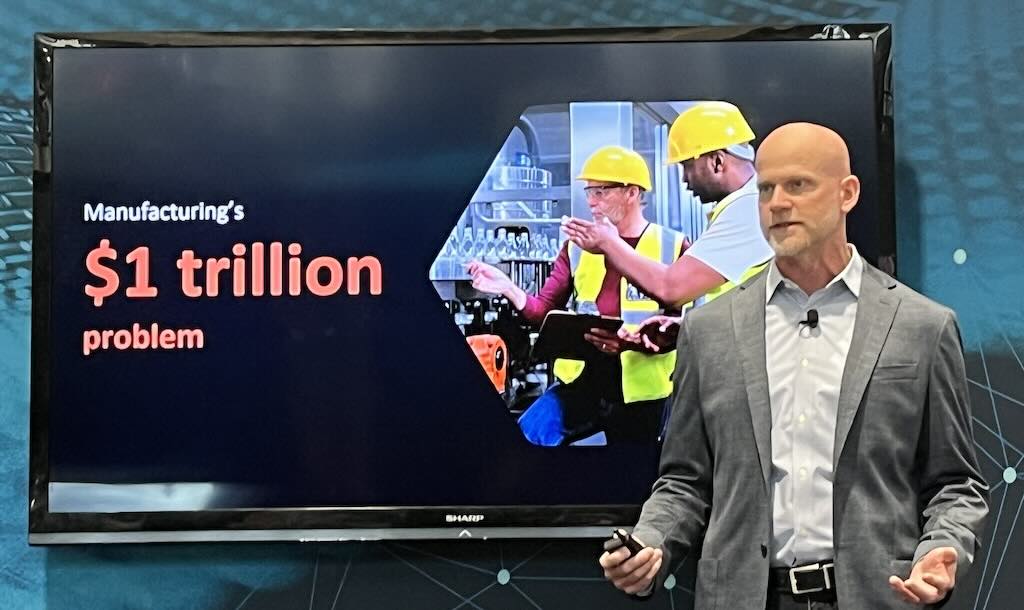
Connected worker insights
- Manufacturers face operational challenges due to a lack of skilled workers, resulting in increased downtime, safety issues, and compliance concerns.
- Digitizing processes and creating an augmented workforce with smart onboarding, personalized training, and AI-powered workforce intelligence.
Manufacturing has gone through many challenges over the last several years with workers retiring and leaving a vast wealth of knowledge behind. Even with companies trying to retain that knowledge, challenges persists.
Chris Kuntz, VP of strategic operations for Augmentir, said the root of manufacturing’s $1 trillion problem is people in his presentation “The Future of Industrial Work – How the Augmented, Connected Worker is Transforming Manufacturing” at IMTS 2024 in Chicago.
The lack of skilled workers leads to increased downtime, more safety incidents, quality and compliance issues. It’s not just the lack of skill; it’s the lack of experience, Kuntz said. Whereas workers in a manufacturing facility would stay in one spot for years, that’s become an outlier. Now, workers leave their jobs in under a year—sometimes in as little as three months.
Creating an augmented and connected worker
Manufacturers have to keep operations running regardless, which puts them in a bind. Kuntz said companies have to hire workers who aren’t as skilled, but still give them the training they need and it has to be efficient. They also need to personalize learning and development and highlight the skills their new workers already have to make them better at their job.
Kuntz said an augmented and connected worker needs smart onboarding, guidance, support and the data working behind the scenes to help them improve. The process, more than anything, needs to be digitized, Kuntz said. Everything from training and skills management to general work execution.
“It’s shocking how much still exists on paper,” Kuntz said. “Might have been okay with a stable workforce, but not now.”
A connected workforce is more than just the worker, though. It also comes down to the people and the systems running operations.
Ways to improve the augmented and connected worker include:
-
Track and manage skills inventory. Digitize and efficiently managed skills for rapidly changing workforce and use the worker’s skills to personalize guidance and support.
-
Intelligently assign work. Assign work to employees with the required skill level, increasing safety and equipment uptime. Digitally prevent unqualified workers from executing tasks.
-
Replicate paper-based forms with smart forms. Create smart forms with no-code authoring tools. Include data collection, validation and workflow branching based on input and job criteria.
-
Career pathing and continuous learning. Give workers visibility, control over career path. Drive continuous learning with training and micro-learning in the flow of work and improve worker engagement and retention.
-
Smarter collaboration and knowledge sharing. Modern collaboration tools for frontline teams can share and capture knowledge in the context of work.
-
Close skills and experience gaps. Reduce onboarding time for new hires and give them access to context-aware, personalized guidance in the flow of work.
-
AI-based workforce intelligence. AI has a great sense of making sense of the noisy data from humans.
-
Enterprise integration. Connect workers into the enterprise. Incorporate frontline workers into the digital thread of the business.
If done right, Kuntz said workers and manufacturers will have a facility controlled by a single, unified interface where everything and everyone is working together toward the same goal.
“A truly connected workforce has a single interface into all these systems,” Kuntz said. “Their daily work happens through a digital device that reduces time to resolve issues and keep systems up and running.”
Chris Vavra, senior editor, Control Engineering, WTWH Media, [email protected].