Leverage IT/OT convergence technology to create sustainable applications with supervisory control and data acquisition (SCADA) software, industrial PCs (IPCs) for edge computing, machine learning software and cloud connections.
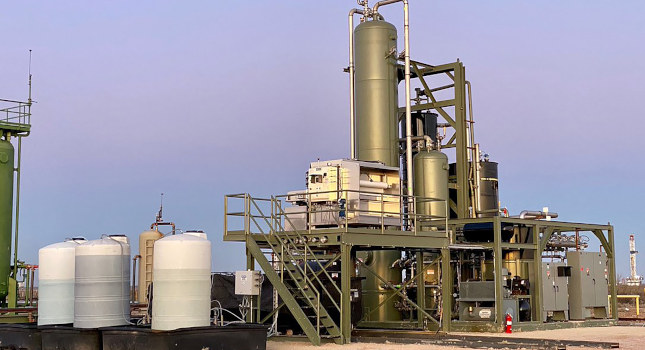
Learning Objectives
- H2S redox require that the quantities of differing chemical agents being added to the gas be adjusted constantly, which has required a manual expert be on-site in the past.
- Through the use of a SCADA system and the MQTT communication protocol, rapid data transfer can be achieved without consuming too much bandwidth, allowing the process to be automated even via a cellular network in a remote location.
Process automation insights
-
An H2S Gas and Acid Treating System removes H2S from natural and converts it into agricultural-grade elemental sulfur for soil remediation, crop fertilizer, and pest control.
-
Measuring and removing H2S from natural gas in new chemical processes are enabled with a SCADA software control system, industrial computers, less bandwidth, self-tuning fuzzy logic control system, integration of weather data and cloud server data distribution.
A process to measure and remove hydrogen sulfide (H2S) from natural gas uses sensors, industrial computers for edge processing, cloud-based applications, machine learning and supervisory control and data acquisition (SCADA) software in a plant that processes agricultural-grade elemental sulfur for fertilizer and other applications. The automation reduces manual measurements and overall labor costs by 75% making the plant cost effective.
Measuring, removing H2S from natural gas
H2S is a flammable, colorless gas that impacts human safety, regulatory compliance, and infrastructure integrity tremendously in a wide variety of applications. Found in about 40% to 60% of natural gas wells worldwide and in almost every gas well in North America, this poisonous gas, with its characteristic smell of rotten eggs, is both an irritant and chemical asphyxiant, thus affecting the central nervous system and breathing. The toxic gas must be removed from the natural gas stream Several technologies exist to remove H2S. While chemicals exist that can directly remove the H2S from gas, they can be expensive and hazardous to dispose of. Such chemicals are only cost effective when dealing with low concentrations of H2S. When dealing with vast amounts of H2S, large plants need to be built to remove the toxic chemical. Most gas wells only contain an intermediate amount of H2S — not enough to warrant building a $50 million facility, but also too much to treat with a $10/lb chemical. In between these two options, there are not a lot of good technologies available to remove H2S efficiently.
New chemical processes, control systems for H2S removal
Streamline Innovations has significantly improved the Redox process and has created one of the most efficient H2S treating solutions on the market. Their Valkyrie H2S Gas and Acid Gas Treating System employs new chemical processes and advanced control systems to remove H2S from natural gas at size scales that range from single wells to entire fields. Representing a step change in H2S treatment, this patented process removes 100% of H2S from the natural gas stream at the lowest cost-per-pound of H2S removal compared to all other competitors, lowering lease operating expenses. Most importantly, the Valkyrie converts H2S into agricultural-grade elemental sulfur, which is beneficial for soil remediation, crop fertilizer and pest control.
So far, Streamline Innovations has produced more than 20 million pounds of sulfur from its plants in Texas and New Mexico, and it is expanding into international markets, biogas treatment and refinery treatment. The produced sulfur would otherwise have turned into SO2, a key generator of acid rain.
Control system challenges for reduction, oxidation processes
Redox requires running two precise chemical reactions: reduction and oxidation. However, it is very difficult to control these two processes optimally. What makes it challenging is that H2S concentrations and flow rates vary in natural gas. Thus, the corresponding amounts of chemical agents added to the gas need to be adjusted constantly. If too much is added, the chemical process can come to a halt. If too little is added, then some of the H2S might get into the pipeline. For this reason, the old process required an expert in the field to check the concentrations and flow rates every few minutes. Unfortunately, experts cannot be always on-site in natural gas facilities, or even travel to them frequently, especially to smaller units on remote wells. Streamline Innovations’ Valkyrie process replaces the “expert in the field” with intelligent and rigorous control of the chemistry, allowing the chemical processes to maintain the equilibrium of chemical agents without human intervention.
At first, Streamline Innovations tested an automation platform written on a standard PLC, but it could not perform the complex calculations and model-based controls. They also built a customized OPC server that communicated with a cloud server, but it had no authentication and security protection. To explore and find the ideal solution, Streamline spent another half-year reaching out to almost every branded solution. Their search led them to two automation companies to help facilitate the control and automation process, data collection, and remote control to solve the redox challenges, reduce variability and stabilize the chemical processes.
SCADA software, industrial computers, less bandwidth
Streamline Innovations uses SCADA software running on rugged industrial PCs, which communicate with a server via the message queuing telemetry transport (MQTT) communication protocol. MQTT allows transfers of relevant data without consuming too much bandwidth, meaning cellular data in remote areas is usually sufficient for operations. As managing the data can be a challenge, intelligently tiered calculations are done between the edge and cloud. Complex calculations, such as model predictive control, by contrast, require historical data and therefore can be done cloud-side.
By contrast, motor vibration data generates huge quantities of subsecond data, and the data is processed at the edge as it is too bandwidth intensive to send all of it to the cloud. Finding the right technology for edge-side processing is critical for successful operations.
Self-tuning fuzzy logic control system integrates weather data
This industrial computers also run Python scripts, enabling Streamline Innovations to perform complex calculations, which include incorporating weather forecasts from the U.S. National Weather Service to help determine optimal operating temperatures. These calculations would not have been possible with a PLC alone. Machine learning (ML) and fuzzy logic algorithms running on Python provide advanced control efficiency and a self-tuning system that increases operational efficiency.
“Ambient temperatures and humidity can have a big impact on sulfur production. ML helps us to predict the temperature and allows us to adjust our surfactant and pH levels for more optimal performance. For example, if the temperature would drop over the next 6 hours, we will actually start heating up our unit even if the ambient temperature is fine,” explained Peter Photos, PhD, chief technology officer at Streamline Innovations.
Convergence of information technology (IT) and operational technology (OT) is “one of the major reasons we were able to develop the technology at a much smaller scale,” adds Photos. “If you think about it, from an IT standpoint using an API for the weather forecast is a trivial calculation. But, with regards to an OT application, in the past, there was no rugged equipment with a fair amount of reliability in an oilfield to facilitate a process like this.”
Industrial computers collect, process data before cloud server distribution
Now, Streamline Innovations employs robust industrial computers, using straightforward IT practices that have incorporated IT into the OT world. Streamline Innovations’ architecture includes Class I, Div 2 certified rugged computers that gather data from the PLC and convert it to useful key performance indicators (KPIs). The KPI data is transmitted to the cloud, with the cloud server distributing the data to the users. When the cellular modem is down, the industrial computers record the data and then transmit it to the cloud as soon as the modem is back up to ensure maximum uptime of the OT equipment.
“That means the system is watching itself, which demonstrates the power of connectivity” with the industrial computer architecture, said Photos.
In addition, Streamline Innovations has extended the SCADA software by running a full version with a module deployed via a local Wi-Fi network. This allows users to access the unit, including its full HMI and historical on-site data from any computer near the unit. This means operators can access the unit from their laptops in their trucks shortly after pulling into the site. This has virtually eliminated the need for a dedicated HMI. Additionally, the cellular communications module allows users to access the same HMI from anywhere, meaning the centralized control room or even the operators’ cell phone can see and control exactly as if they were on-site. This has greatly eliminated the need for operators to go into the field, for example, if the unit has shut down or an alarm has been triggered. They can simply restart the unit remotely with their phone from their home or office.
Wireless communications replace at-site flow measurements
With Moxa’s solution and Ignition, Streamline Innovations has benefited from a 75% reduction in labor costs as they do not need as many fulltime employees on-site to manage the units. The constant updating of flow rates and chemical addition by an employee is no longer necessary. Industrial computers are doing the calculations and provide maximum uptime. Furthermore, in the past, Streamline Innovations could not address several variables, such as temperature and humidity variations, which could affect the amount of water during the chemical process. Now, they can because ML has been added to model-predictive control with help from SCADA scripts running on the industrial PCs. “I call it Edge of Glory. It is the data revolution. It helps Streamline unveil the revolutionary H2S removal technology,” added Photos.
A robust data collection system improves operational performance, and the integration of the data benefits every branch of the company. The data is used in maintenance planning, designing more efficient units and corporate-wide business model calculations. In the future, the fully integrated data will help automate the business across the spectrum, allowing data-driven decisions to be made at every level of the company.
The improved Valkyrie System, using advanced automation, has brought several benefits to Streamline Innovations and their clients. Benefits include cost-savings with set-up, labor reduction, improved uptime and efficient intelligence gathering from the systems for continuous operational improvement. Streamline Innovations plans to expand the use of Valkyrie technologies to more customers by leveraging their solutions team and experience to help solve the challenges facing industrial markets.
Eddie Lee Director, Global Industry Marketing, Moxa Inc. Edited by David Miller, content manager, Control Engineering, CFE Media and Technology, [email protected].
CONSIDER THIS
How can real-time, intelligent controls be used to replace formerly manual processes in your own operations?