Integrating information technology (IT) and operational technology (OT) organizations is difficult but critical to IIoT success. Five best practices for overcoming these cultural barriers are highlighted.
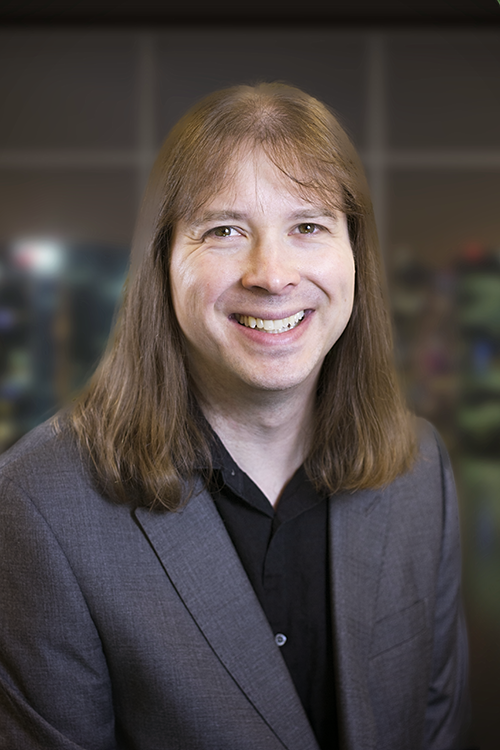
Decades of taking a siloed approach to industrial machinery has left most major facilities with a complicated mass of equipment controlled by a tangled web of ancillary systems. Additionally, each machine or system likely has custom elements requested by the person running the project when it was installed. This inefficient and expensive approach stands in the way of companies reaping the benefits they set out to achieve with increased automation and Industrial Internet of Things (IIoT) initiatives. Convergence of information technology (IT) and operational technology (OT) can help.
Sandy Vasser, a retired IC&E manager for ExxonMobil, observed in the 2017 Control Engineering article “Wider capabilities via IIoT; lowering project costs”(CE, March 2017, Feedback, p.20) that companies should be looking at how to use new automation technologies to simplify architectures and reduce the customization of existing automation systems.
On an organizational level, this is not about reducing cost of existing ways of doing business, but rather adopting a new way of thinking. According to Vasser, reducing the size and complexity of automation hardware solutions will open the door to greater opportunities with IIoT. In fact, IIoT standardization can help with the solution simplification itself. It also can help with another issue he raises, which is replacing the aging workforce.
Information integration
Advances in IIoT technologies make it easier to tap into data generated by connected equipment as well as control and automation systems. Using digital models of equipment and gathering real-time, historical, and contextual data such as maintenance and environmental information, IIoT systems apply advanced analytics, predictive reasoning, and machine learning to deliver broader and deeper insight than individual systems can.
For example, data analytics can help operators adjust real-time production variables for greater yield and quality; monitor and maintain equipment health to avoid failures and reduce repair and maintenance costs; and optimize performance as operational conditions change.
Historical operational data as well as information from other systems such as programmable logic controllers (PLCs), human-machine interfaces (HMIs), parts inventories, enterprise resource planning (ERP) systems, and others provides deeper, facility-wide insight and enables automated resource management capabilities.
However, new technologies themselves don’t solve the bigger issue of people doing things the way they always have. Before any IIoT initiative can succeed on a large scale, a shift in overall corporate strategy must occur to support the organizational and cultural changes necessary to let the technology do its job.
Crucial IT-OT convergence
Bringing IT and OT organizations together is critical to IIoT success, but it is one of the most difficult changes to make. Companies will often approach IT and OT convergence with an eye towards reducing duplication of similar systems and job functions for cost savings. This is a short-sighted strategy, and is likely to fail for numerous reasons such as:
- Firmly entrenched ways of doing work
- A lack of understanding about IT and OT’s roles
- Different executive leadership, and
- Different marching orders from executives.
According to a 2017 report from the IoT Institute, 57% of IIoT professionals identify overcoming cultural barriers and organizational silos as their biggest obstacle in achieving IT-OT alignment. Five tips to overcome these challenges are highlighted.
1. Change must be driven from the top: Management must actively lead the charge for digital transformation and IIoT initiatives. All stakeholders, especially operations, IT, and security teams, must be held accountable for support and execution of new ways of thinking and working. Among companies experiencing success with IIoT projects, it’s a common practice to designate a purpose-built organization early on specifically to drive digital transformation.
2. Plan for security at the outset: Companies also need to think about how to manage their newly created asset—the vast repository of operational data produced by connected equipment. Important details like what data to share and how to handle privacy concerns must be top of mind at the outset and require the intimate involvement of security teams.
3. Learn from subject matter experts (SMEs): The cross-functional cooperation brought about by IT-OT alignment fosters key relationships that should take advantage of the deep knowledge held by senior, experienced SMEs. While long-time workers hold entrenched beliefs and ways of doing things, they also possess expertise that should be tapped to guide the functionality of the IIoT system. When knowledge from SMEs is designed into the system, it preserves existing expertise, enabling new hires to become productive faster. Younger prospective employees expect more data-driven decisions nowadays; IIoT systems can help attract and retain new talent.
4. Lean on technology partners: Identifying internal knowledge and expertise gaps is critical at the outset of any initiative, but taking steps to fill those gaps efficiently can mean the difference between success and failure. Technology partners can infuse an organization with a deep familiarity toward IIoT. Partners also should be able to compliment internal proficiencies with detailed insight into the underpinnings of their solutions as well as possess the flexibility and willingness to adapt their systems to support changes to a company’s ingrained ways of working. By collaborating, partners, SMEs, and digital transformation teams can effectively design the right technology for the desired business outcomes.
5. Start small with an eye towards scalability: Identify one project with clear metrics for success and a reasonable timeline. Often, this means focusing on real-time and historical data for a single piece of equipment and incorporating sophisticated analytics to accurately predict potential failures in order to avoid expensive unplanned downtime. However, it’s important to approach any initiative with the intention of scaling the capability to an entire population of machinery. Companies also should think about other ways this capability can benefit other supply chain elements such as repair and maintenance and parts inventories.
Regardless of industry, companies can simplify both control and automation functions, while achieving superior business results if they are willing. As Vasser observed, “To reduce project costs, every discipline must challenge ALL historical project execution processes and procedures and eliminate or simplify the processes and procedures.”
Today’s IIoT technologies are more powerful and accessible than ever. With the right organizational changes, SME knowledge, and cooperative partners, they can help with simplification and automation goals while laying the foundation for a multitude of other potential business benefits.
Dave McCarthy is senior director of products, Bsquare. Edited by Mark T. Hoske, content manager, Control Engineering, CFE Media, [email protected].
KEYWORDS: OT and IT convergence, IIoT, information integration
- Unconnected assets stand in the way of Industrial Internet of Things (IIoT) principles.
- Information technology (IT) and operations technology (OT) organization convergence helps connect assets.
- Advice helps with IT and OT convergence.
CONSIDER THIS
What could you or your partners achieve with better industrial communications?