Automation Integrator Guide: Criteria help in selecting the best automation system integrator for your next project.
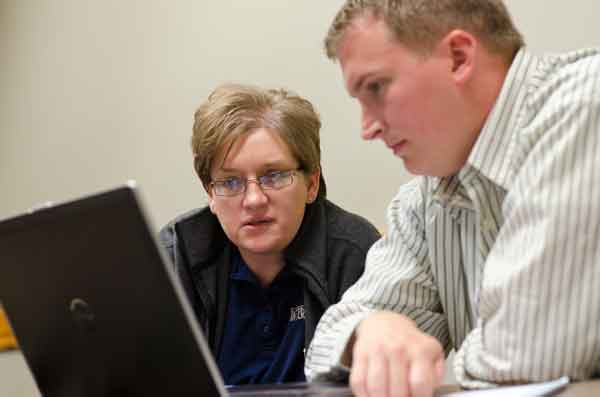
With so many system integrator options available, how do you know what makes a good system integrator good? Some offer a full spectrum of services from engineering and design to panel construction. Others concentrate on a specific service. Some integrators focus on a particular industry, while others work across all types of industry. No doubt you’ll find that many systems integrators are excellent at providing robust and inclusive solutions for clients.
So, what really makes one systems integrator stand out from the others? It might be the integrator’s ability to always meet your project schedule. The integrator may be an expert in the system platform that you wish to use. Maybe it understands your industry inside and out. Whatever the case, you want to choose an integrator that will provide your company with value-added engineering services that focus on your company’s specific needs. Whether those needs are for industrial control systems, manufacturing execution systems, or plant automation, such highly technical areas require industrial processing knowledge and control system expertise to be of value. The value that a control systems integrator provides is unique to your company. Your experiences and perceived value will differ from those of another company.
Evaluate, prioritize
Your company will need to evaluate and prioritize which qualities will drive decision making. Here are some things to look for that excellent systems integrators do well:
1. They listen to clients—really listen—to understand the business and production issues that clients face.
2. They use the information obtained by listening to engineer superior solutions that meet clients’ current needs and position them for future success.
3. They do all that within budget.
Excellent systems integrators employ team members who have the innate ability to understand client needs. Project managers, designers, engineers, and other people involved in the project should be skilled at interpreting technical requirements and translating them into an appropriate control solution. Excellent systems integrators can do this either from an engineered drawing or by studying a process that isn’t already documented to evaluate how to help you improve it. In addition to responding to the written specifications, they also can identify value-added opportunities to make the solution better.
When you engage a systems integrator about a project, an excellent systems integrator will spend a great deal of time asking questions and seeking to learn about your company’s process and future plans. The integrator will seek to understand where your company is going to ensure the solutions presented are in your best interest and position you for future success. Most importantly, great systems integrators listen for what you are NOT saying, taking it upon themselves to look out for your company’s future growth even if at first you don’t know how to best articulate what you seek.
Excellent systems integrators have a balance of specialized industry work and experience across industries. They are knowledgeable about process control, data, and information management. While specialization in a single industry can have its benefits, experience in a wider range of industries allows you to benefit from new innovation. Perhaps advances or regulation in one industry may shed light on a similar issue in your industry. Engaging with a systems integrator who has worked in multiple industries will help you apply those innovations in your business.
Excellent systems integrators are experts in process control. They implement solutions to increase productivity and quality, and drive facility performance. In addition, great systems integrators can help you with data and information management. With appropriate tools, you can equip operators to manage production remotely or with wireless devices. You can also provide management or executives with a dashboard view into what is happening on the plant floor. This level of information management allows your company to track performance and compare locations to one another to establish best practices and benchmarks for your company.
Repeat work
In your search, be on the lookout for integrators who have a record of repeat work for their clients. When companies use the same systems integrator repeatedly, it speaks to their level of trust and performance with that integrator. Ask the integrator about its project completion rate. If it has ever walked away from a project leaving it unfinished, it could indicate any number of things: poor project scope and estimating, poor planning and budgeting, or poor internal project management systems.
You may also narrow your search to systems integrators who are certified with the Control Systems Integrators Association. CSIA certified integrators have been evaluated in areas including general management, human resources management, marketing and business development, financial management, project management, system development lifecycle, supporting activities, quality assurance, and service/support. Each of these areas includes standards set by industry members who have determined what elements should be met to be considered the “best in class.”
When you reach the point of comparing proposals, if you choose to comparison bid, you might find that project quotes from systems integrators can differ significantly. When one quote is substantially lower, be wary. The integrator may be overlooking significant project elements. In addition to comparing bottom-line price, be certain the deliverables are also comparable.
Client communications
Much of what separates an ordinary systems integrator from an excellent integrator is the ability to communicate well with clients. That sometimes includes delivering news that you do not like to hear. Perhaps the client is asking for a process change that does not appear to be in its long-term best interest. Or, maybe the client is asking for a project to be completed in a very short time frame without fully understanding the impact that the timeline may have on budget or scope. These kinds of issues require a systems integrator to be able to skillfully and truthfully say “no” to the client. While this idea goes against the old saying that the customer is always right, sometimes, the client needs to hear that its choices may not be what is best long-term. That’s really where a great working relationship comes in to play. An established relationship with a great systems integrator can be a boost to your company. Look for these traits and open the lines of communication for a great start.
What really makes a good integrator good? It depends on what you are really after. Your best move will be to ask the systems integrator a lot of questions to see how its philosophies compare to your own. Pay attention to how well the systems integrator is listening to you. Choose an integrator that you are comfortable will add value and help you build a solution that meets your future needs. Certainly a third-party evaluation of its business processes (like CSIA certification) adds icing on the cake.
– Jeff Miller is director of automation services at Interstates Control Systems Inc., a Control System Integrators Association (CSIA) certified company based in Sioux Center, Iowa. Reid Vander Veen is a business development representative for Interstates Control Systems Inc. Interstates specializes in electrical and automated control systems for industrial and processing facilities in industries such as food and beverage and value-added agriculture. Edited by Mark T. Hoske, content manager CFE Media, Control Engineering, Plant Engineering, and Consulting-Specifying Engineer, [email protected].
Consider this
Do you make a system integrator specification as you would a product or machine specification?
Go Online
Select the right integrator for your project using the Control Engineering Automation Integrator Guide multi-parameter search tool.