Combining a scalable human-machine interface (HMI) system and supervisory control and data acquisition with additional edge functionality gives machine and plant designs a high degree of flexibility and adaptability to quickly react to changing market environments and maintain fast innovations cycles.
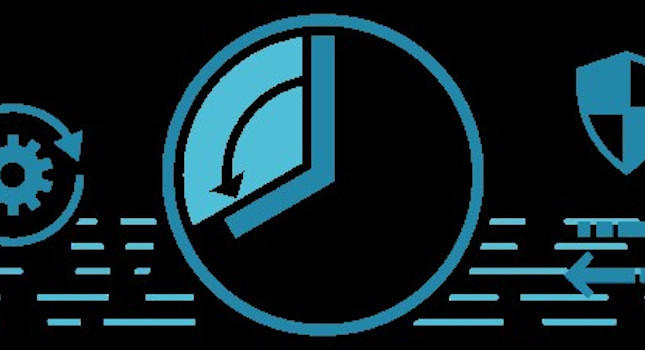
Things in engineering and technology are changing quickly and we must adapt. Changes in daily life are sometimes small and barely noticeable; sometimes they’re big and have an immediate impact on everyone.Â
All these changes also influence production and how those involved prepare production for the future.Â
One of the biggest challenges companies still face is increasing flexibility and time to market while reducing production cost at the same time. While this challenge isn’t new, the pressure to adapt has increased in recent years.Â
What can companies do today to prepare for production tomorrow?Â
Production data everywhereÂ
New production concepts for Industry 4.0 don’t rely on the classical International Society of Automation (ISA) automation pyramid anymore. Instead, they split production in smaller and flexible units which exchange data on many levels.Â
This requires flexible and scalable human–machine interface (HMI) systems where the same project and screens can be used on a 7-inch HMI panel, a supervisory control and data acquisition (SCADA) system or a smartphone. The data is available in real time on any device when needed without increased programming effort. Â
This allows engineers to adapt to production to the everchanging requirements while using existing automation equipment.Â
Continuous optimizationÂ
Continuously increasing productivity is everyone’s goal. The challenge is how to adapt production while keeping everything running smoothly at the same time.Â
This is where edge devices can help. Edge devices provide a platform to run analytics, predictive maintenance and other tools that help optimize production without interfering with production itself.Â
An edge computing device could be an industrial PC (IPC) or the edge functionality can be integrated in the automation device like an HMI panel. This way the HMI panel fulfills both requirements, ensuring stable production while allowing for a high degree of flexibility in running new programs or tools that help increase productivity.Â
One possible use case might be to have the HMI device controlling the machine while the edge portion of the device collects additional data for predictive maintenance or runs complex algorithms for machine optimization.Â
Of course, this combined functionality isn’t just beneficial for HMI devices. Programmable logic controller (PLC) modules, drives and network devices with integrated edge functionality will allow for further increase in productivity as well.Â
To summarize, combining a scalable HMI system covering 7-inch HMI panels as well as SCADA systems with additional edge functionality provides a unique advantage for future machine and plant designs. These new systems provide a high degree of flexibility and adaptability to quickly react to changing market environments and while maintaining fast innovations cycles.Â
Bernd Raithel is director product management and marketing, Siemens Factory Automation, Siemens Industry. Edited by Mark T. Hoske, content manager, Control Engineering, CFE Media, [email protected].Â
KEYWORDS:Â Programmable logic controller, I/O devices, edge computingÂ
Wider use of production data requires updated HMI, SCADA, and edge devices.Â
Continuous optimization benefits from edge computing.Â
CONSIDER THISÂ
How will more advanced edge computers help your applications?Â