What does it take to implement a systems integration project? This case study examines several potential challenges and how they were resolved.
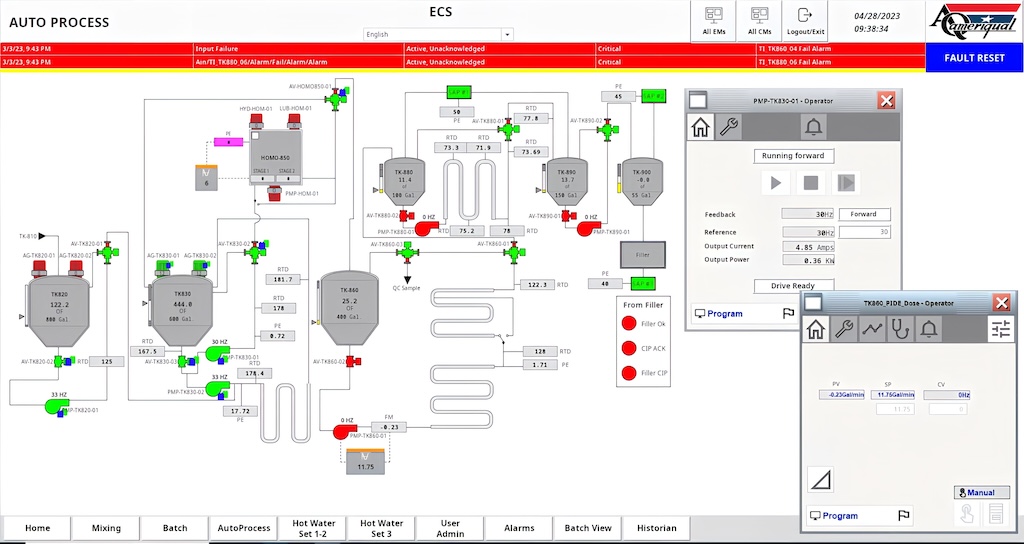
System integration insights
- Understand how a control system integration company like ECS Solutions can provide solutions for batch processing applications in various industries, including private label food manufacturing.
- Learn about the benefits of using Inductive Automation’s SCADA solutions for maintaining a high level of readiness and delivering flexible batch solutions.
- Gain insight into the importance of partnership, transparency, accountability, and communication in successfully completing projects with short timelines and complex systems.
ECS Solutions partnered with AmeriQual Group to implement a batch solution running on Inductive Automation’s Ignition platform. The project was delivered on an aggressive timeline.
What does it take to successfully implement a systems integration project that includes aspects of both operations technology and information technology?
Success in many industries – in many walks of life, in fact — is the product of preparation meeting opportunity. This may be especially true in private label food manufacturing. “The people, processes and equipment must be able to adapt to ever changing market demands,” said Wes Blankenberger, VP of operations & maintenance for AmeriQual Group, Evansville, IN.
Much as brand owners make timely use of private-label manufacturers, the goods makers themselves leverage systems integrators and others to assemble existing and new equipment into functional processing systems.
Moreover, similar qualities define success for the control system integration space. Integrators are often recognized for their ability to deliver in specialized market segments. Having as a team a rational mix of technology professionals allows the integrator to apply staff, often on short notice, to priority projects. Integrators tackle projects or parts of projects, often in concert with yet other partners.
At Evansville, IN-based ECS, daily conversations revolve around equipment modules, recipe procedure models and equipment availability, including from entry-level technicians to the highest-order software specialists and project managers. One tool the entire team knows well is Inductive Automation’s SCADA solution.
“Every ECS teammate learns Ignition from day one with us,” said Mark Randall, ECS Project Manager. “The training is online, free of charge, and modular. That makes it relevant upon hire at ECS and then regularly as a teammate matures,” Randall said.
Specific instance
AmeriQual Group is frequently called upon by major food companies and the U.S. Department of Defense to provide packaged solutions. AmeriQual’s reputation for quality gives the company opportunities to work on these challenging projects.
When presented with a chance to land a series of large contracts with a well-known label, AmeriQual quickly pressed all their assets into action to create an entirely new kitchen.
AmeriQual ordered long lead-time items with less-than-optimal information available. Equipment from its local storage cache was inspected, tuned up and prepared for deployment. Existing relationships with local contractors allowed it to prepare the plant infrastructure and quickly move into detailed piping and wiring. Perhaps most important, its relationship with ECS allowed for a quick project assessment and documentation of a framework to establish budgets and obtain bids.
AmeriQual also gave ECS personnel a tour of the facility and explained what it had in mind. “From that point ECS came back to us with ideas and showed us what its systems looked like and could do. We came up with a strategic path and a phased approach to implementation. The phased approach allowed us to implement operations improvements on shorter timelines and simplify the training requirements for our team members,” Blankenberger said.
A fully integrated solution from ECS was integral to AmeriQual’s long-term success. The solution would allow for as much automation as reasonable, minimizing the number of new operators needed to run the system.
“We didn’t consider using manpower as a stop gap because it is tough to find manpower and the processing requirements for the product would be challenging to accomplish manually,” said Blankenberger.
Down to brass tacks
Following these conversations, ECS received an order in early January of 2022. Working from preliminary piping and instrumentation diagrams (P&IDs), the ECS team crafted a flexible batch solution on the Ignition platform.
Folsom, CA-based Inductive Automation’s Ignition is an integrated development platform that can be applied to supervisory control, manufacturing execution and achieving digital connectivity by means of the industrial internet of things.
“This project encompassed a few elements that we’re uniquely positioned to address,” said Randall. “The fact that it was batch processing put it squarely in our wheelhouse and the fact that it was based on Ignition opened up many options for the team delivering the solution.”
ECS extends Ignition’s capabilities by developing custom faceplates that tie into the Rockwell FT Batch engine running behind the scenes. “We have more than twenty custom faceplates in our Ignition library that we’ve deployed to tie into Rockwell’s PlantPAx process objects,” Randall said.
The team used elements of ECS’ S88 builder, developed in Ignition, to make the connections via Rockwell’s existing API for PlantPAx. “This level of integration allowed us to speed development in a way that keeps things from getting unruly. Our R&D and prior use of these elements made a real difference on this project,” Randall said.
Support for operators
In addition to the process control and SCADA tie-in, ECS also addressed the client’s multilingual requirements. “Approximately 20% of our staff is Spanish speaking,” Blankenberger said. “Operator interfaces are easily toggled from English to Spanish depending on the team member. This has improved willingness to work in this area of our facility as well as reduced training time.”
PlantPAx prompts are mirrored as well. “We used the localization capabilities within Ignition to accomplish the switching,” Randall said. “Before we could do that, however, we used our native Spanish speaking teammates to examine and tweak the generic translations that were delivered via software. The adjustments add contextual value to the translations that software alone cannot deliver. Batch operations require specific terminology. Given effective direction, the pool of workers able to be productive for our clients grows in depth and quality,” Randall concludes.
AmeriQual’s Blankenberger agrees, stating “Transparency, accountability, and communication are the attributes critical on projects with short timelines. AmeriQual and ECS were true partners in the project. There were many challenges and tough discussions throughout, but we were able to prioritize tasks based on what was best for the project.”
The project came together successfully on a very aggressive timeline. “I thought the batch system would be ready on time for testing to begin, but that there would be a few bugs to work out, due to the short timeline and complexity of the system,” Blankenberger said.
Instead, the ECS solution delivered high quality, finished batches the first week of launch. Thus, at the confluence of preparation and opportunity, another successful project built on Ignition was delivered by ECS Solutions.
Benefits and challenges of batch production
According to MES provider Tulip, the benefits of batch processing in the food industry include the following:
-
More control over quality and better traceability
-
Shorter production time
-
Lower cost equipment
-
Lower chance of contamination.
On the other hand, challenges of batch processing include
-
Greater storage space needed for in-between production stages
-
Batch errors can lead to greater waste and production costs
-
Increased employee downtime
-
Possibility of bottlenecks that limit production.