Automation system integrators explain how automation upgrades benefit from digital transformation, analytics and automation asset data. Get more advice from an automation upgrade example of PLC system updates and about the automation project development lifecycle.
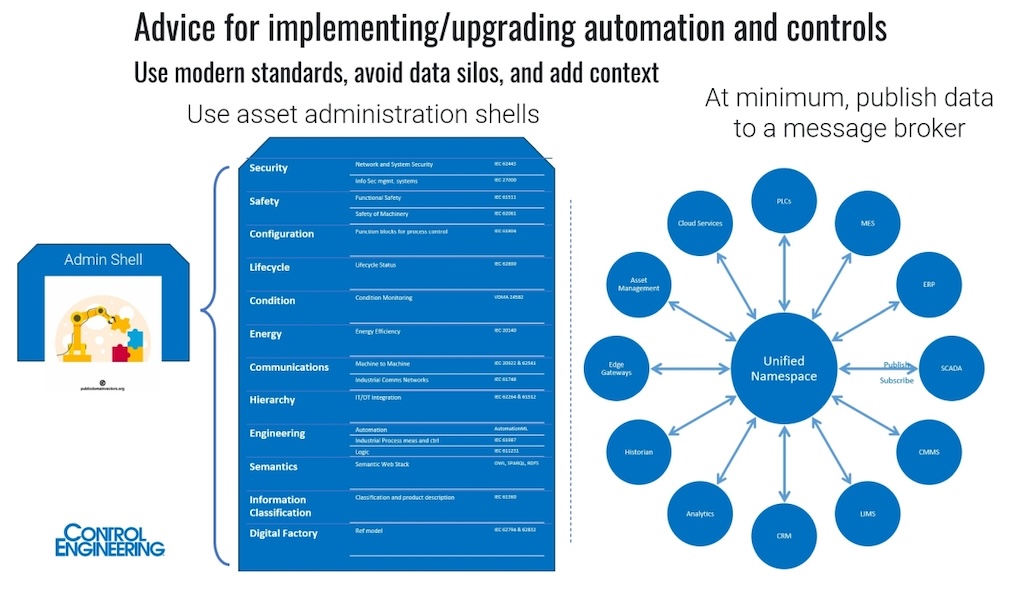
Learning Objectives
- Review how an edited transcript from a popular Control Engineering webcast provides automation system integration advice.
- Understand how automation upgrades benefit from digital transformation, analytics and automation asset data.
- Learn from an automation upgrade example of upgrading a legacy PLC system and from how automation upgrades go more smoothly with a project development lifecycle.
Control system integration insights
-
An edited transcript from a popular Control Engineering webcast provides automation system integration advice on how automation upgrades benefit from digital transformation, analytics and automation asset data.
-
An automation upgrade example of upgrading a legacy PLC system and information about the automation project development lifecycle can help.
Control system integrators explain how to use information about industrial digital transformation, automation equipment modernization and control system documentation to succeed with automation upgrades. The advice was adapted from a transcript of popular Control Engineering webcast, “Automation Series: How next-generation automation will help in 2023,” with help from OpenAI’s ChapGPT, then was reviewed and further edited by webcast moderator, Mark T. Hoske.
Webcast instructors were:
-
Tyler Graham, director business development-digital transformation, and Randy Rausch, director of technology-digital transformation, Eosys
-
Mike Howard, vice president of system integration at George T. Hall
-
Matt Lueger, executive vice president, NorthWind Technical Services.
A question asked of the system integrators during the webcast was: How can customers best understand a system integrator’s views and advice to improve automation upgrades?
Understanding digital transformation in context of automation upgrades
Rausch: Let’s define digital transformation. It’s not just digitization; it’s about leveraging a data-driven culture to make better business decisions faster. Making decisions based on data, with ready access to relevant information, allows you to adapt to the current realities faster than your competition. The primary value of digital transformation is business agility.
What decisions are we talking about? Not ones that ladder logic or a flow chart could make. I’m not referring to straightforward local optimization. I’m talking about analyzing overall equipment effectiveness (OEE) trends to decide on controls and instrumentation products, troubleshooting the root cause of a nagging issue, optimizing the supply chain, understanding why some batches are good and some bad and incorporating field data. How do you answer questions about making your business more competitive and understanding your customers?
Automation upgrades: Answering questions you didn’t know you had, analytics
Answering these questions requires analytics at a higher level. You need to address questions you didn’t know you had when you first installed or built your equipment. If you’re good at it, you resolve that issue and move on to the next question, often requiring new information. If every time you need to answer a question, you have to kick off a systems integration project to get new data, you won’t answer many questions or at least not quickly.
Traditional manufacturing information systems are good at what they’re designed to do, but you can’t just bolt analytics on top. Advanced analytics require data in a form that’s analyzable. The industry acronym is FAIR: You need findable, accessible, interoperable, reusable data. Without that data readily available in the right context, you’re unlikely to get much out of it.
What can automation and control groups do to lay the foundation for analytics? Use modern standards, avoid data silos and add context. As decision complexity increases, you’ll likely need information from many sources, with more consumers of that data. We can’t predict how future analytics will use that data, so knowing the context is crucial to derive information and higher levels of meaning.
Storing information about automation assets with the assets
A great place to store all information about the asset is with the asset. In this case, we could use an asset administration shell. It’s a digital twin of a physical asset providing a standard way to describe and access information about an asset. Think of it as a container holding information about that asset. It could tell you the type, location, details, references to other assets, and you can query that asset shell to figure out where it is, who made it, the health condition, how it’s configured. With the right security credentials, you could get livestreaming data from sensors on that asset and have all the necessary context to infer meaning and establish relationships to other data points. It gives you a standard way to interact with an asset.
Original equipment manufacturers (OEMs) can design this into assets. For legacy assets, integrators or factories can add an asset administration shell on top of existing equipment to make it a full participant in your Industry 4.0 ecosystem. Now, if using all those IEC standards is too daunting right now, I offer an alternative minimum requirement. In this case, don’t do point-to-point integrations; use an event-driven architecture. Your assets in your system should publish data to a single source of truth or a central hub using a publish and subscribe messaging system. Some call this a unified namespace. There’s a rich market of vendors providing brokers to implement this at various scales. Message queuing and telemetry (MQTT) is one frequently used protocol in this architecture. Certainly, you can use OPC Unified Architecture (OPC UA) if you use the publish-subscribe (PubSub) specification. And other protocols work well here. These are key things that you can do to help prepare for what’s coming with next-generation automation.
Modernizing automation equipment and related best practices
Howard: I will discuss modernizing automation equipment and software along with some best practices. Modernizing control systems has numerous benefits, but there can be risks, and a proven way to reduce such risks and offer the best possible outcome for our customers, especially on large-scale projects, has been a phased approach.
Considering the initial investment made in automation and control hardware and software, there are often options to ease into these modernization projects without causing a lot of stress or downtime or even excessive expense. Some key elements to this approach include developing a detailed scope of work with project scheduling and identification of facility personnel that will partner with us. It’s crucial to have somebody as a champion of the project on-site Software conversions and factory acceptance testing with client SCADA. And a drawing package that includes network diagrams, electrical requirements, mechanical layouts, are some best practices that go along with this.
Over the last few years, we’ve taken on some rather large modernization projects. We often use the manufacturer’s modernization tools that allow for this phased approach to reduce risk, expense and downtime. This technique also allows customers to gain immediate benefit from modernization through this method.
Automation upgrade example: Updating a legacy PLC system
As an example, let’s examine a legacy system with a number of hot standby programmable logic controller (PLC) systems, with a coaxial remote input/output (I/O) network that supports around 100 remote I/O racks. Using modernization hardware and software tools, we converted the programs, validated the PLC applications using the client’s supervisory control and data acquisition (SCADA) system software, and by loading that on our servers, we tested it.
After acceptance testing, we installed the new hot standby central processing units (CPUs), which continued to serve the existing remote I/O network. In this instance, we were able to install and test 13 hot standby PLCs during a plant shutdown period of approximately five days. There was considerable time savings with the automation upgrade by using some of those conversion and modernization tools.
A phased approach can be beneficial to making larger scale projects more manageable. We use software and hardware tools from the manufacturer to streamline this process. And you can’t underestimate the importance of planning and the documentation that goes along with this type of project to ensure that your hardware and network requirements are going to meet the client’s needs and result in a successful project.
Automation upgrades: More useful with a critical project development lifecycle
Lueger: As we look at implementing upgrading control, one of the things that we find most successful for us is making sure that we follow a critical project development lifecycle. A good documentation package is the best place to start for the project. Too often we find that customers don’t have good documentation for the new equipment or the existing systems that they have. So getting that documentation in place in a good drawing package or even functional requirements specification or user requirements specification is the best place to start.
But quickly after that, we put a lot of emphasis on building the infrastructure to support future growth. Not all those projects are beginning with the end in mind. We really like to have that conversation with customers about where they want to go in the future as they kind of evolve in their digital transformation. That usually means getting their IT group involved and aligned early, whether it be data acquisition or additional visualization, or even if the scope of the project doesn’t require it, they may want to maximize their current investments by setting a foundation for the future when it comes to data acquisition and tying those components together.
The final step is making sure that we’re reviewing the process along the way, and that’s different for every customer and every project. Sometimes those are in a couple of steps, and for larger projects, more extensive ones, a more phased approach, requiring more touchpoints. That includes during both the design process and through the development process, getting alignment with screenshots or with system simulations. Make sure all know where the automation upgrade project is going so that the endpoint isn’t a surprise to everyone. That’s an important step in the automation upgrade process.
Mark T. Hoske is content manager, Control Engineering, CFE Media and Technology, [email protected].
CONSIDER THIS
How can advice from system integration experts help your next automation project?
ONLINE
Webcast instructors answer more audience questions about next generation automation in this article.
View the webcast until Jan. 18, 2024