Control Engineering China: As intelligent manufacturing trends continue, enterprise are no longer concerned if they should implement digital transformation, but how, how to make it more efficient and maximize the return on investment.
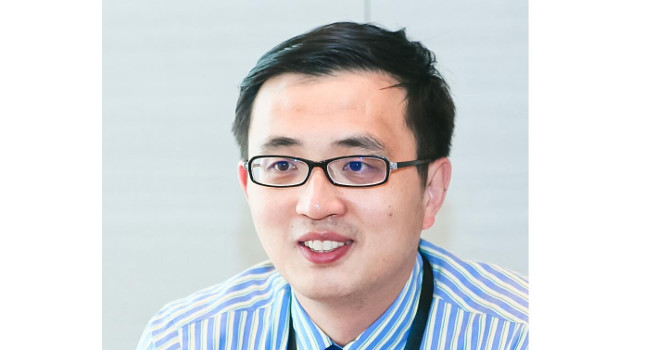
Manufacturing enterprises are faced with pressure brought by users’ differentiated demands and the global trade uncertainties. They are in urgent need of realizing production line upgrades, efficiency increases and consumption reduction to improve competitive advantages in global markets. As intelligent manufacturing continues, enterprises are concerned about how to implement digital transformation, make it more efficient and maximize the return on investment (ROI).
Control Engineering China interviewed David Dai, business manager of Rockwell Automation Greater China Center of Excellence, at the Rockwell Automation global road show at Tianjin Station. Dai has more than 10 years of experience in the automation industry and in intelligent manufacturing consulting, and believes that the key to the successful digital transformation is in finding best practice.
Digital transformation best practices
According to a survey on the current situation of global digitization, 84% business administrators believe that digitization and the Internet of Things (IoT) will help enterprises grow in the medium and long term, but only 7% enterprises have formed specific implementation plans. What has hindered the digitalization process of enterprises?
Dai has strong feelings on this point because the Center of Excellence for which he is responsible provides users from various manufacturing industries in the region with customized operations and management schemes for intelligent manufacturing operations. The center also consults on interconnecting enterprises.
Avoid stagnation
Many factors cause the stagnation of manufacturing enterprises in the process of digital transformation. Dai summarized four common reasons: Complexity, connectivity, agility and scale. Industrial applications are significantly different in different industries, production lines, process requirements and other aspects, and each industry has its unique needs.
At the same time, the automation level of enterprises is also uneven. Many enterprises have not reached the digitization of equipment, let alone networking and intelligence. How can ROI be maximized, given the scale, project cycle and objectives of different enterprises? Doing so requires helping enterprises “find the best practices for digital transformation,” Dai said.
Intelligent manufacturing diversity
Different from IT digitization, great differences exist in every industrial application, every factory, and every production line. Faced with diverse customer needs, “We wish to pool more technical resources through establishing a platform,” to focus on a certain kind of products to allowing technical personnel to have more access to knowledge on one platform to meet the continuously increased demands of customers in applications.
At present, the Center of Excellence has more than 100 experts in five fields including intelligent manufacturing consulting, industry solutions, original equipment manufacturers (OEM), components, and products. Whether vertical connection or horizontal coordination, it can provide precise technical support and services for users.
In its three years of operation, those involved believe “the needs of customers change rapidly,” Dai said, from the original focus on products to more attention to applications, from information to intelligent manufacturing. “With the change of customer demands, our architecture is also constantly optimized.”
Future intelligent manufacturing: three trends
In addition to consulting for intelligent manufacturing, the department where Dai works also advises product experts. It resolves problems that the front-end product team has no way of solving, but also maintain deep focus on cutting-edge technology trends.
Dai believes the three trends of the future of intelligent manufacturing are worthy of attention.
- Cooperation among platforms.
- Applications of disruptive technologies, such as artificial intelligence (AI) and augmented reality (AR) in the automation industry. AI-enabled software can detect production anomalies, perform predictive analysis without data experts, and remind workers of the implementation of investigation or intervention when necessary, thus enabling enterprises to simplify the decision-making process.
In addition, the rapid development of 5G, a new generation of wireless mobile communication technology, is also of interest.
“5G will bring huge opportunities to the entire industrial intelligent manufacturing ecosphere,” said Dai. Its advantages such as low delay, high capacity and high speed will facilitate the large-scale application of AR, AI and other technologies in the industrial field.
“Expanding Human Possibility,” Rockwell Automation’s new brand commitment brings more innovative spirit. In the future, we also expect Rockwell Automation to bring Chinese manufacturers unlimited possibilities to explore intelligent manufacturing.”
Aileen Jin, editor-in-chief of Control Engineering China. Edited by Mark T. Hoske, content manager, Control Engineering, CFE Media, [email protected].
KEYWORDS: Digitalization, digital transformation
Digital transformation is happening but there’s concern about ROI.
Digitalization concerns include complexity, connectivity, agility and scale.
Automation experts can help with industrial implementations.
CONSIDER THIS
How are you overcoming digitalization challenges?