While common in the refining sector, many other industries have yet to take advantage of advanced process control (APC) technologies.
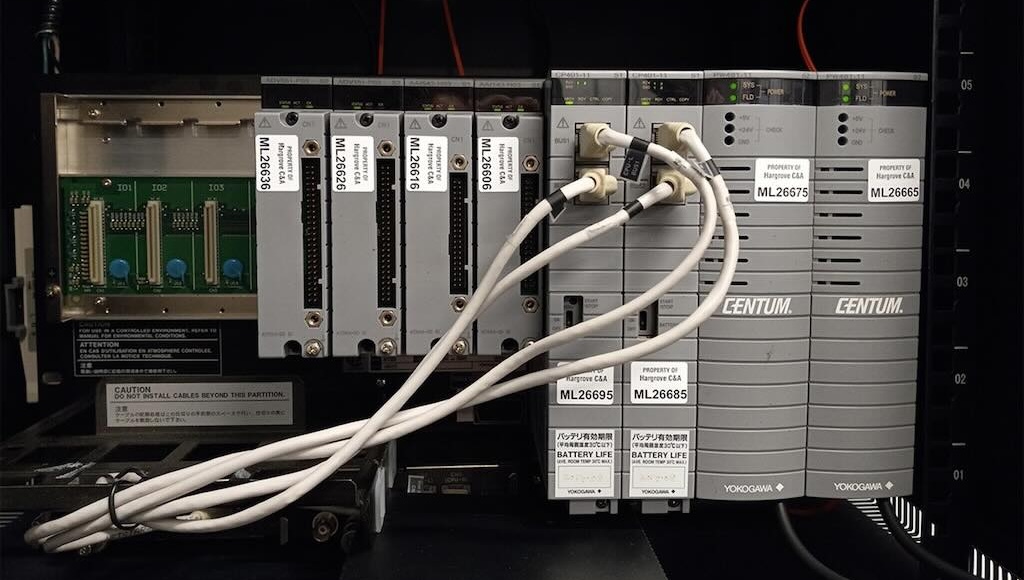
Learning Objectives
- Learn about the benefits of advanced process control (APC).
- Explore what might hinder APC deployment in industries.
- Learn how to optimize an APC system and maximize return on investment (ROI).
Advanced process control (APC) insights
- In the refining sector, where competitors may sell each other’s products, the use of advanced process control (APC) becomes crucial for increasing efficiency and profit margins.
- Refineries face evolving challenges, including environmental scrutiny, electric vehicle adoption, and fluctuating feedstock prices. APC proves valuable by optimizing production volume, quality, and uptime, mitigating these challenges.
- Despite APC’s success in refining, wider adoption faces barriers in industries lacking economies of scale. Limited manpower, poor instrumentation and non-linear processes hinder APC, emphasizing the importance of stable basic process control.
Few industries are so commoditized that it is regular business practice for a competitor to routinely sell a product as their own. However, this is the norm for the refining industry where the local BP station may be selling gasoline from the nearby refinery or vice versa. In that sort of market, you use every tool at your disposal to increase margins, and advanced process control (APC) has been relied upon by refining companies for decades. Many other companies in other industries also can use APC to facility to increase their efficiency and profit.
APC is a multi-variable control algorithm and engineers also may hear the related term model predictive control (MPC). These systems use matrix math and linear algebra techniques to build statistical relationships between variables, establishing cause and effect relationships between many variables simultaneously. APC is a control layer that sits on top of the traditional single loop proportional-integral-derivative (PID) control algorithms found in distributed control system (DCS) and programmable logic controller (PLC) systems.
The refining sector is rapidly evolving. Water, air, and pipeline transport permits are reviewed with increasing scrutiny by governments and local communities. With the increased sales of electric vehicles (EVs), institutional investors are questioning their longtime holdings in traditional petroleum companies. While there is still much debate over the practicality of EVs and what any transition timeline may look like, there is no question change is coming to this industry.
Even before these headwinds, refineries have dealt with a market where they have little control over fluctuating feedstock prices (oil being a globally priced commodity), as well as public and political pushback on increases in pump prices.
Since refiners deal with large volumes, they have high capital investment costs for their equipment. Any technique they can find to get more production volume out of their existing equipment can save tens or hundreds of millions of dollars.
There are generally three levers to increase total production volume out of a unit: Increase volumes, improve quality/conversion and increase uptime. APC can help with the first two levers by tightening process variability and shifting control setpoints to more desirable limits. It can also help the third lever by increasing unit uptime by keeping a process out of operating regions that can cause fouling, excessive equipment wear, or other issues that result in unexpected downtime or increased maintenance.
The role APC plays in manufacturing
With these advantages, refineries began the first APC rollouts in the 1970s. Widespread APC adoption throughout the refining sector occurred in the 1990s. Other industries took notice and use of APC applications by bulk commodity chemicals producers began to occur, but it never took off in other industries like it did in refining. APC has now been readily available for nearly forty years and far predates most other “advanced” technologies commonly grouped under the Industry 4.0 umbrella, yet like many of those technologies, remains to be fully adopted.
These systems have historically been standalone software applications that send cascaded setpoints to PID loops in the DCS/PLC system through an external data connection. Some newer DCS platforms have APC/MPC functionality built in, but it’s still much more limited than the standalone systems available.
The role of APC systems is to look at the “bigger picture,” look at process dynamics by monitoring many process variables, and determine which variables to manipulate to achieve improved process control. The APC system then shifts the process to a more cost-efficient set of operating conditions. The goal is tighter control closer to operating limits and saving money.
How APC was successfully used in refineries
So, if APC advantages are so obvious and the cost benefits are so tangible, why doesn’t everyone use APC? First let’s look at why APC was successfully deployed in refining. Refineries have economies of scale. Their size and throughput ensure they have an economic driver to try new things, and small improvements can add up to big dollars. Their facilities are generally larger resulting in increased staff and headcounts that offer more manpower to experiment with new tools and maintain the successful tools long-term.
Most refineries are part of larger companies that also have corporate resources and budgets. Refineries are generally well-instrumented, well-maintained, and operate largely under automatic control. Their processes also lend themselves to APC applications as it’s easily applied to steady-state continuous operations.
Refineries are the epitome of this type of operation, often running for a year or more continuously. Finally, most refineries operate similar processes, and these processes are quite well studied and understood. For example, the knowledge gained with an application developed at one refinery can often be applied to other refineries, either by a third party or as personnel change jobs.
APC has struggled for wider adoption in other industries due to the inverse of many of the situations already noted. Many companies don’t have economies of scale that refineries do. They tend to run lean organizations and don’t have the staff to try new things or maintain niche software packages. APC applications aren’t rocket science, but they do require knowledge, skill and time to deploy and maintain.
Some industries still operate with many manual gauges or poor instrumentation. If their processes are not reliably run by the control system in automatic mode, a cascaded layer of APC control will do little to no good. Finally, not all processes are well-suited to APC.
APC works best with steady-state processes with linear relationships. Although APC packages have gotten better at handling non-linear processes, they still have limited use in batch or semi-continuous processes.
Many manufacturers also make specialty products with specialty processes. Each one of these unique processes requires extra investigation and experimentation to develop quality APC models.
Recognizing how APC can benefit a facility
Despite these obstacles, APC may still be the right choice for a facility. Considering cost pressures, the need to compete, and the implementation of software packages, APC holds several benefits to reduce costs and increase efficiency.
However, there are still a few things that haven’t changed. APC will never be successful if basic process control in a DCS/PLC is not stable or reliable. Whether companies choose to use APC or not, there are numerous financial and safety reasons to get a process under stable automatic DCS/PLC control. This should be a minimum standard to operate a modern, safe, and efficient plant today. The first step to operating efficiently is to install or fix necessary instrumentation and valves and then focus on making DCS/PLC control improvements.
Next, look at the process type. Batch processes don’t generally lend themselves to APC applications, but that isn’t a strict rule. Ask questions about the process such as:
-
Are there long cycle times?
-
Are there steady state periods during the batch that need better optimization?
-
Are there support operations like distillation columns outside the batch process that operate continuously in steady state?
If so, the next step includes looking at the operating margins. How much potential profit is being wasted with suboptimal raw material or energy use or with poor conversion rates and quality issues? Based on those savings, how much could a company spend on an APC application that would pay for itself in a year or less? MPC/APC functionality built into DCS packages can have major benefits for some users. Even though these packages have their limits, they can be a great proof of concept and leverage an existing control system engineer’s skillset.
Companies shouldn’t be afraid to seek outside assistance for both initial APC deployment and ongoing maintenance. Third-party firms can often help get the system deployed and generating revenue faster than they can if they were self-deploying. Some companies have even found success with contingency fee arrangements where upfront costs are minimized for a share of operational savings.
Given all that, now may be the right time to take a page out of the refining playbook and look at APC adoption.
Heath Stephens, PE, is the digitalization leader for Hargrove Controls & Automation. Edited by Chris Vavra, web content manager, CFE Media and Technology, [email protected].
MORE ANSWERS
Keywords: advanced process control, APC
ONLINE
See additional stories at PID and APC at https://www.controleng.com/control-systems/pid-apc/
CONSIDER THIS
What benefits have you gained for applying APC in your facility?