A steel pipe maker implements supervisory control and data acquisition (SCADA), manufacturing execution (MES) and statistical process control (SPC) at their facility to improve operations.
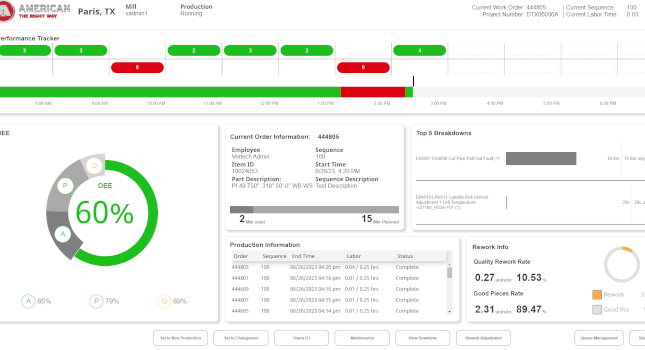
Automation insights
- Automation in manufacturing isn’t just about replacing labor—it enhances quality, safety and decision-making, improving processes without eliminating jobs.
- Even slower, manual manufacturing processes benefit from automation by enabling accurate data tracking, reducing downtime and boosting overall efficiency.
In the wake of global labor shortages and supply chain issues, many manufacturers are turning to system integrators and automation to improve efficiency and productivity. But what does innovation look like for slower, low-volume manufacturing processes that have traditionally been manual?
One such company, American SpiralWeld Pipe (ASWP), engaged systems integrator, Vertech, to implement a comprehensive automation plan for a new state-of-the-art facility in Paris, TX.
ASWP, a division of the American Cast Iron Pipe Company, is a spiral-welded steel pipe manufacturer that supports the municipal water and wastewater transmission industry as well as hydroelectric, industrial and power markets. It’s not a small operation. ASWP makes pipes up to 50 feet long with diameters up to 12 feet wide. They have three plant locations that produce a combined average of 6000 pipes, equating to more than 20,000 tons of steel, annually.
ASWP faces the same labor shortages as other manufacturing companies and is always looking for ways to improve production efficiency. Kent Davis, director of business process automation and operational excellence, explained that for ASWP, automation primarily increases quality and throughput.
But it takes more of a supporting role when it comes to labor needs. “I want to be clear that the use of automation at ASWP is not a labor reduction focus. We use automation to make the job task easier for the employee… allowing them to make decisions faster and more accurately based on data and facts instead of intuition,” Davis said.
With the large scale of its manufacturing operations, automation also protects ASWP employee safety. Davis said that advances in mechanical automation have allowed them to take a “hands-off” approach to pipe production and transport throughout the facility. Operators interact with machinery HMIs (human-machine Interfaces) rather than the pipes.
ASWP approached Vertech in 2020 to implement supervisory control and data acquisition (SCADA), manufacturing execution (MES) and statistical process control (SPC) systems at their greenfield facility in Paris, TX, and roll out the technology at their Columbia, SC and Flint, MI locations.
Phase 1 of the project, completed in 2021, tackled the SCADA system. The system tracks current and historical production data and funnels it to a centralized control room at the Paris company headquarters. The control room has 18 48-inch industrial monitors that display real-time Industry 4.0 data and analytics. Eventually, all divisional operations will be managed across multiple locations via SCADA, MES, and SPC from the centralized control room.
Phase 2, discussed below, focused on implementing the MES. ASWP wanted a system that tracked labor and production data, transforming it into useful OEE (overall equipment effectiveness), downtime efficiency and resource efficiency metrics.
The challenge
Labor tracking typically involved operators working on a pipe and then self-reporting the time it took to complete the process. However, this resulted in inaccurate data, unreliable for business decisions or improvement efforts. ASWP needed a more automatic way to track process start and end times without depending on the operators.
For OEE accuracy, ASWP wanted to track downtime and production, maintenance, and changeover times.
Spiral-welded pipe isn’t made quickly. Producing massive spiral-welded pipes requires several core processes or “lines.” A steel coil is placed into a mill and spiral-welded, formed into a pipe and cut to length. The ends are then prepped, and joints are formed with the beveler and expander. The pipe then undergoes hydrostatic testing.
The pipe is next lined with cement and cured (CML). After curing, it goes through a blaster where a blast profile is achieved. Finally, it receives an external coating. After additional quality checks, it is ready to ship.
Usually, ASWP manufactures one type of pipe for as long as possible. The changeover process takes days or even weeks.
“Our manufacturing is moderately sized volume with lower rates of speed. Thus, we were seeking ways to optimize processes and drive out inefficiencies,” Davis said.
The solution
Vertech designed the MES using Inductive Automation’s Ignition software platform to track work orders through each line and automatically calculate OEE based on machine availability, performance and quality.
Even with a somewhat manual process, Vertech was able to set up automatic triggers to track shifts, changeovers, downtime, rework and maintenance when an operator started or stopped a process. They also developed dynamic shift scheduling to track production accurately, but allow managers to delete shifts as needed.
The system included 20 screens, 13 devices, 7,812 tags, 32 clients, around 2000 alarms, and an MSSQL database. Other technology used included Sepasoft for OEE, Sierra Airlink for SMS Notifications and REST API to communicate with the ERP.
Of the 20 screens developed, five are highlighted here: the MES Overview, the Mill Overview, the Route Exceptions Report, the Changeover Report, and the Rework History Report.
Benefits and results
The SCADA and MES implementations at ASWP were both successful. The SPC project is in the preparation and design phase. Roll out of the systems to two additional locations is in the CAPEX (capital funding) phase.
The MES has improved safety and quality, decreased downtime and boosted overall efficiency. The system is intuitive and uses workflow structures. Often, operators can refer to a single main screen that displays all current shift metrics and possible actions.
Because of the easy-to-use UI, Operators easily monitor OEE to address and mitigate downtime issues. Managers can keep up with hourly metrics and strategically plan a shift. For example, they can predict how long a changeover should take and proactively schedule maintenance to increase OEE scores.
“Vertech took our vision, technical specification, and design specification and custom-built a solution to our needs. SCADA and MES are extremely valuable automation tools in our division. Now we make decisions faster and more accurately with the use of these tools. Of course, manufacturing is not always perfect, and there will be instances of failure, but we have the tools to tell us why and how the failure happened… There have been many issues resolved that were happening for decades,” Davis concluded.
Thea Sander holds the technical marketing title at Vertech, a provider of industrial automation services. Vertech is a provider of world class industrial automation services. Controls & Automation, Digital Plant Services, Industrial IT, and Panel Design. [email protected]