There’s a big difference between a phased process control system migration and just putting delaying the problem of control system obsolescence. Those who don’t plan for distributed control system (DCS) obsolescence will see options narrow.
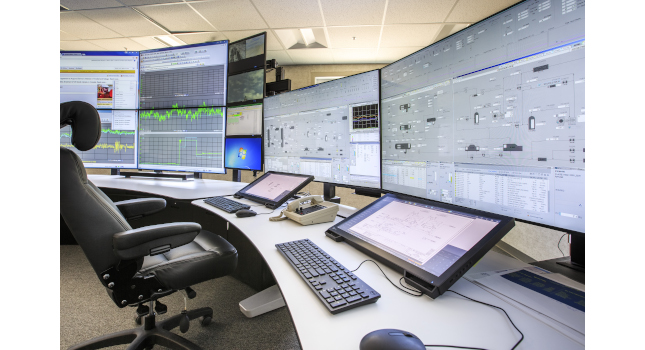
Obsolescence in the process control system is such a significant threat that reluctance to migrate to newer technology can seem baffling. Aging controls and equipment bring a whole host of problems. These include, but are not limited to, difficulty sourcing spares and rising prices for them, increasing maintenance costs, declining reliability, capacity constraints, and a skills gap when those with experience on legacy process control systems retire.
At best, obsolescence leads to higher costs as plants mitigate the rising risk of downtime or compliance failures. At worst, it can jeopardize continued, safe operations.
Moreover, this ignores the massive strides in control technology and the benefits this can bring in terms of operator performance, safety, efficiency, cybersecurity, enhanced functionality and controller capacity. Users that migrate to a modern system can integrate control, safety and auxiliary systems, and benefit from enhanced control and visualization. They can respond to new business opportunities, expand capacity, and make use of new applications and solutions for advanced process control, asset management and production management.
In addition, in most cases, the control system is a small expense in comparison to the overall plant and the value of its production. A single, significant period of unplanned downtime is often enough to result in losses well above the cost of a new distributed control system (DCS).
Despite all this, the number and range of legacy process control systems show little sign of shrinking. Many thousands of legacy DCS systems continue in operations across the world with a large proportion of these two decades old or more.
Control system migration is not easy
In fact, it is these potential losses that probably explain much of the reason businesses are reluctant to migrate a DCS. The very risk of downtime and disruption as a result of the process scare them off. It may be the direct disruption and requirement to take systems offline and shut down the process while putting the new control system in place, or the potential for longer-term disruption from unforeseen problems when the new process control system is brought online.
While the case for migration in the face of obsolescence is compelling, it is rarely so clear-cut in practice.
“Obsolescence” itself is poorly defined. It may mean technical DCS obsolescence, with performance deterioration and declining reliability manifesting in missing yield. It also can mean functional obsolescence with constraints resulting in lost opportunities; or supply obsolescence, with the lack of process control system support, in-house expertise or spares creating a risk for continued operation. In all these cases, most of the signs of obsolescence gradually accrue.
Vendor support might be withdrawn for a process control system on a particular date, but the costs of aging equipment and systems grow and develop over time. It is not always easy to determine the point at which those costs and lost opportunities justify replacing the systems.
Operators do have other options. Rising maintenance costs, for instance, can be controlled through switching to predictable service contracts. Upgrades also can extend the life of the control system and stave off some of the impacts of obsolescence.
Limiting DCS migration options
Human-machine interface (HMI) migration is one of the most important aspects of control system modernization. Upgrading legacy DCS operator stations to HMI technology allows plants to provide a common user interface to the integrated process control system architecture. This reduces training and maintenance requirements by keeping existing graphics, networks, controllers and I/O in place. It also provides direct access to the control network with read/write data access and integrated alarms and events.
When a control system requires change, replacing existing controllers also makes economic sense. For migration, two critical functions are required: the existing DCS field signals must be quickly moved to the new process control system, and the existing control schemes must be migrated — and preferably improved.
For a large-scale process control system retrofit, it is often best to use a phased migration. This approach eliminates risk by incrementally narrowing the focus, while providing a fall–back position to the old DCS system. It requires communication with the existing system for interim phase-in, physical co-existence with the old equipment to enable a hot cutover, and the ability to switch seamlessly between old and new signals for testing and tuning purposes.
Phased migration does have its drawbacks, but it is a lower risk approach with less downtime. Further risk and downtime reduction can be achieved by simulating the new process control system prior to installation. With phased migration, the control system is in a transition state. This means the appropriate scope must be selected for each phase so the end user can stop at any point in the migration and still have a supportable system.
A process control system partner, not a DCS product
Of course, there are good reasons plants may stick with the existing vendor. It may be that the updated system is the right solution for them. In many cases, though, plants do not seriously look at the other options.
The caution around migrating the process control system is due to the perceived risks of disruption. Remaining with the existing vendor is less a vote of confidence than a risk management strategy.
On the one hand, this makes some sense. Some aspects of the DCS migration are likely to be simpler remaining with an updated version of the same technology. However, the technology alone will not determine the success or otherwise of the migration. The tools available for migrating, the experience of the engineers, their plan and strategy for the project, and the expertise of those involved will play a major role in determining how smoothly a migration goes, and how well disruption to operations can be minimized. And that is not to mention differences in the DCS’ functionality, capacity, price and performance.
When selecting a process control system vendor, plants are selecting a technology and migration partner. They need to pay equal attention to both. Anything limiting that choice should be carefully considered.
Satnam Bhogal, global initiatives leader, Migrations, Honeywell Process Solutions. Edited by Chris Vavra, associate editor, Control Engineering, CFE Media and Technology, [email protected].
MORE INSIGHTS
Keywords: process control system, distributed control system, control system migration
Performing a phased migration of a process control system is expensive, but it’s cheaper than letting a DCS become obsolete and break down.
Some manufacturers hesitate disrupting the process control system because it will cause downtime.
Phased migration has some risks, but if done correctly, the end user can still have a supportable process control system if a stoppage is needed.
Consider this
What was the biggest challenge you faced when migrating your process control system?