Sophisticated “all-in-one” systems help overcome barriers to productive use of industrial data and realize their full value.
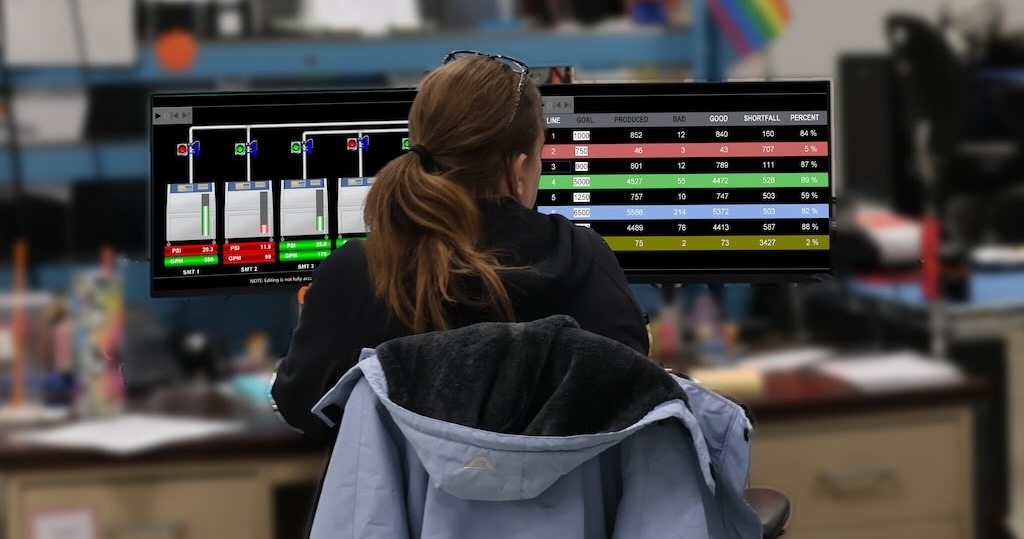
Learning Objectives
- Understand how all-in-one industrial data platforms can help companies advance their digital transformation initiatives.
- Learn how human-machine interfaces (HMIs) and programmable logic controllers (PLCs) have evolved to meet modern users’ needs.
- Learn how modular flexibility and cybersecurity play a role in keeping data secure and easy to access.
Industrial data insights
- Manufacturers need software support for basic to advanced-level industrial applications with capabilities such as protocol conversion, edge computing, advanced networking, remote access, visualization, cloud integration and the ability to send data to relational databases.
- All-in-one software platforms deliver that support, simplifying many key industrial data access and connectivity steps with drag-and-drop capabilities that make it easier for companies to capture and use their most valuable asset – their data – to measure automation productivity.
- These platforms feature a common environment that simplifies many tasks critical to accessing industrial data, connecting that data to other systems within the plant or across the enterprise and ultimately visualizing that data in real time so operators and plant managers can optimize industrial performance.
Today’s industrial manufacturing and process companies are intensely invested in building smarter, more sophisticated production systems. Digital transformation has created a data-rich environment with layer upon layer of equipment generating critical information about the performance, efficiency, energy consumption and reliability of a manufacturer’s plant and production systems.
Across every industrial segment, manufacturers have been expanding the digital backbones that connect their disparate systems. At some companies, multiple production and networking systems feature a range of hardware and software installed over time with incompatible communications protocols. Many factories and plants have equipment such as programmable logic controllers (PLCs) and human-machine interfaces (HMIs) with older software and firmware, creating serious obstacles for efficient access and use of industrial data.
Building out strong and productive industrial data systems calls for software that is sophisticated and feature-rich. However, it also needs to be easier to implement and configure and overcome the barriers to productive use of industrial data.
Developing an all-in-one industrial data platforms
Automation technology suppliers have developed a wide range of hardware, software and communications networks to enable today’s advanced manufacturing and process production systems. In many cases, this technology is self-contained and uses proprietary communications protocols and programming tools that need training and familiarity to carry out many routine tasks such as updating a packaging system’s production recipes or programming and integrating a new touchscreen operator HMI.
These obstacles are compounded by the fact that many industrial applications consist of legacy equipment with limited operability. The older equipment, while reliable, may have outdated communications protocols and other software features that make it problematic to extract and integrate the data into the production value chain. With some industrial data platforms, solving these incompatibilities can require expensive hardware and time-consuming programming to access and connect the data.
There are innovative new approaches being launched in the automation, manufacturing, and process industry marketplaces to address these challenges. Powerful, feature-rich industrial data platforms have sophisticated capabilities across a range of industrial applications yet are much easier to implement and use.
Rather than specialized functionality, these “Swiss army knife” software platforms simplify access to industrial data with drag-and-drop capabilities that minimize the need for specialized programming and software engineering skills.
These platforms can support basic to advanced level industrial applications with capabilities such as protocol conversion, edge computing, advanced networking, remote access, visualization, cloud integration and the ability to send data to relational databases.
There are advantages to having a single software platform with consistent user interfaces, standard tools and drag-and-drop features. A common environment simplifies many of the tasks critical to accessing industrial data, connecting that data to other systems within the plant or across the enterprise and visualizing the data in real time so operators and plant managers can optimize industrial performance.
These platforms also are designed to simplify common yet critical tasks. One example is network component installation. If a new piece of equipment with a PLC is being added to a production line, these all-in-one software platforms have default settings that implement all the key tasks associated with that integration step. Steps such as adding data tags are automated, so bringing the PLC into the industrial network requires minimal configuration steps.
At the same time, these platforms provide advanced functionality for systems integrators or end users who want to carry out more customized configuration setups based on unique manufacturing or production requirements.
Choosing the right industrial data software platform calls for careful consideration of their capabilities, to determine which platform will provide the most complete program for long-term success and growth.
Developing robust protocol conversion
These all-in-one software platforms support many capabilities. One of the most critical is protocol conversion where the platform acts like a friendly translator that helps devices communicate with each other and brings data from these various devices to a centralized location.
Many manufacturing and industrial systems incorporate PLCs, sensors, electronic valves, servo drives and other control devices installed 10 to 20 years ago. These devices support legacy or proprietary communication protocols that may not be compatible with newer technologies. Often this legacy hardware supports serial communication drivers which make it even more difficult to gather data and send it over the network to the SCADA system or cloud. While these facilities are moving towards incorporating newer technologies like OPC UA and message queuing telemetry transport (MQTT), it is very expensive to install new hardware and convert all the legacy devices to new ones.
The most effective solution to this challenge is a robust set of protocol conversion capabilities. This can be one of the strengths of the new all-in-one industrial data software platforms. Some technology suppliers have robust built-in protocol conversion capabilities, able to support up to 20 simultaneous protocols from libraries of over 300 legacy and newer drivers.
Modular flexibility for industrial operations
No two industrial operations are the same — and no industrial operation stands still once production lines or manufacturing systems are brought online. New products are introduced, and growth demands expansions or upgrades of existing facilities, which means industrial data access and connectivity need to be upgraded or enhanced along with the new equipment.
Advanced industrial data platforms will have the modularity needed to accommodate these evolving production systems with ease. For example, if a facility is adding wireless communications capabilities to a production line, there are companies that offer modules that can be field-upgraded to Wi-Fi or cellular interfaces with a software change, rather than purchasing new hardware.
In some applications, a system integrator will specify installing a protocol conversion device to interface with an older piece of equipment. As production needs change or additional equipment is added to the network, there can be advantages to upgrading the protocol converter to an edge computing gateway with more advanced networking capabilities.
Leading industrial data platforms will support this changeover via a software change — a capability that’s a standard feature built into the software. There are some automation network suppliers that will insist on swapping out the module for a new device and charge for both new hardware and software.
Developing comprehensive cybersecurity approaches
It’s an unfortunate fact of modern life that industrial networks have become major targets for cybercriminals. Hackers and ransomware criminals will try and target industrial systems for vulnerabilities so they can access enterprise IT networks through industrial data systems — in part because at many companies these networks were not as rigorously protected in the past as the main computer networks.
It is vital to assess the cybersecurity capabilities of industrial data software platforms. Modern industrial networks are often based on Ethernet network designs that are wide open out of the box. Without security measures in place, the environment is vulnerable and significantly increases risk for uncontrolled access to critical system components.
By design, most network hardware can be configured for proper network segmentation to limit network access. Securing the network perimeter limits the access coming into or out of the plant floor. Furthermore, segmenting the network prevents devices on the plant floor from accessing other systems.
To support this “defense in depth” segmentation approach, it’s important that industrial data platforms incorporate the latest security features, such as a stateful firewall, access control list capabilities, packet filtering and secured virtual private network (VPN) connections.
These features need to be as flexible as possible, giving network managers the ability to fine-tune their security features to optimize both data security and network performance. This includes setting password expiration rules and implementing access control lists and firewall rules so specific ports only open at specific times, minimizing the risk of improper access. There are even cybersecurity features that can take legacy data protocols that are not encrypted and encrypt the data as it passes through nodes in the network, eliminating additional vulnerabilities.
Optimize the cloud for industrial data platforms
Many industrial enterprises store critical operational data in cloud-based platforms to get sophisticated reporting and analytics on their systems. These platforms provide greater flexibility and give manufacturers access to powerful, cutting-edge platforms. They make it easier to consolidate and manage manufacturing data from hundreds, even thousands of production point sources, mining that data for real-time insights into ways to improve productivity, efficiency and return on capital.
A critical challenge for manufacturers is managing this volume of data so that it doesn’t drive up bandwidth costs and bog down cloud services. Many production systems have devices that generate streams of data about device performance, alarms and other data points. Depending on the system, it may not be necessary to collect all that data all the time.
Industrial data platforms can play an important role in optimizing this process. Rather than capturing and delivering all the data every device and system generates, the most effective platforms make it easy to discriminate and manage cloud data usage. These platforms support the ability to choose how frequently to send data from any given system. More frequently for critical points of concern; less frequently for standard performance data that doesn’t need constant updating.
Manufacturers want the flexibility to easily define both machine-level and production line data points such as alarms about drives overheating or linear systems not fully completing each duty cycle. Cloud-based analysis can correlate patterns and issues across multiple systems, to modify preventative maintenance practices, invest in equipment upgrades or adjust production processes.
Well-designed industrial data software platforms will incorporate support for the MQTT protocol, which can “report by exception.” This means data is only transmitted when it has changed. Industrial data software platforms also should make it easy to buffer data, so critical data is not lost if there is an interruption in connectivity.
Manufacturers are seeking to maximize production system efficiency. The right data platform with well-designed tools can help streamline and optimize their use of cloud-based systems.
Visualizing industrial data to drive user actions
Industrial data software platforms need to do more than efficiently access data and connect it across the enterprise. Actionable data needs to be visualized and presented in clear and compelling formats that give machine and plant operations real-time data on the performance of their systems.
The latest HMIs and operator panels are designed to deliver data on the factory floor in ways that match the specific operational requirements of each manufacturing line, machine or process. They incorporate features that let users integrate data from across multiple devices and, in conjunction with edge computing platforms, acquire and display data that has been converted from multiple legacy protocols.
HMIs and panel meters often are stand-alone products with programming and configuration tools that are separate from the rest of the industrial data software platform. That means original equipment manufacturers (OEMs), system integrators and end users have to learn a whole separate package of visualization software.
However, leading industrial data technology suppliers integrate visualization programming into their software platforms to simplify and speed the process of bringing these vital factory floor systems online. The latest panel meters and touchscreen HMIs feature large, easy-to-read displays. They also include user-selectable graphics and intuitive screen libraries that are simple to configure and customize to specific plant and production line requirements.
Integrating visualization into the functionality of industrial data software platforms makes it easier to deliver this new generation of visualization technology. Operators and line personnel can respond to issues faster, process critical information immediately and even have one operator monitor multiple machines and processes with a wireless tablet HMI. These tools let operators see more than just information. They also see what that information means, which helps them react faster while taking the right steps.
Choosing the right industrial data platform
Many industrial technology providers have powerful, effective software integrated with their product lines. Often, this software is highly proprietary and different components — like protocol converters or remote access devices or edge computing gateways — have stand-alone programming and configuration tools that can complicate and slow down the integration of new production equipment into existing facilities.
There are distinct advantages to working with a technology provider whose industrial data access, connect and visualization systems share a common, all-in-one software platform. This kind of platform, with automated capabilities for many tasks, as well as drag-and-drop configuration tools, can save significant time and effort when new equipment is added to production lines.
Combined with robust protocol conversion capabilities, as well as visualization, advance networking, remote access and cybersecurity features, the right industrial data software platform can help businesses across many industries advance the digital transformation of their manufacturing systems and leverage the full value of their most valuable asset: their industrial data.
Megha Agrawal is a software product manager at Red Lion. Edited by Chris Vavra, web content manager, Control Engineering, [email protected].
MORE ANSWERS
Keywords: human-machine interfaces, HMIs, industrial data platforms
ONLINE
See additional HMI, OI stories at https://www.controleng.com/control-systems/hmi-oi/
CONSIDER THIS
How can all-in-one automation platforms help improve your operations?