In a November 9 webcast, “PLC series: PLC hardware speed, I/O, communications, redundancy,” David Ubert, senior automation specialist at Black and Veatch, and Eelco van der Wal, managing director at PLCopen, discussed how PLC designs have changed to meet automation and control challenges in recent years.
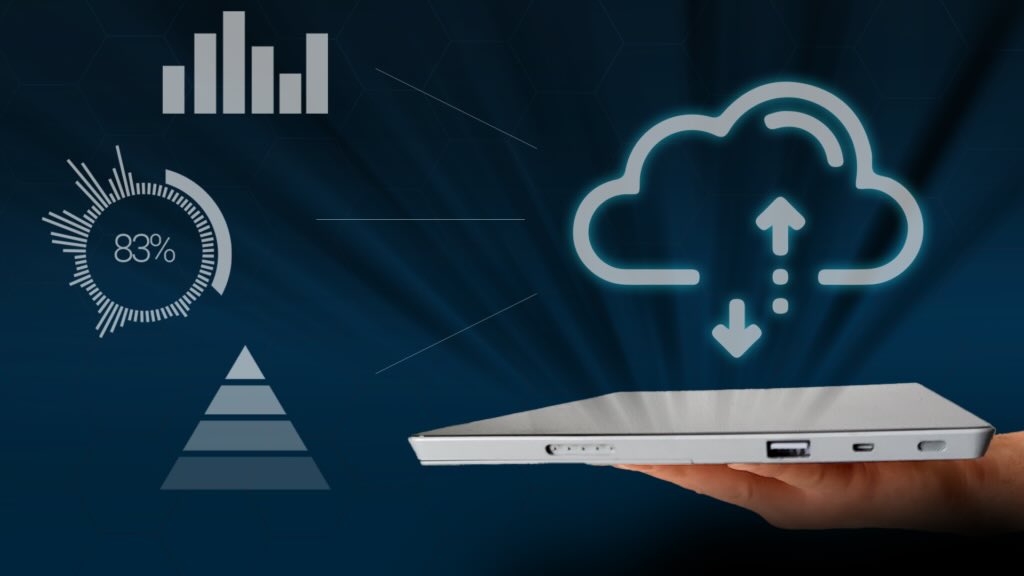
Programmable logic controller (PLC) insights
- In a November 9 webcast, “PLC series: PLC hardware speed, I/O, communications, redundancy,” David Ubert, senior automation specialist at Black and Veatch, and Eelco van der Wal, managing director at PLCopen, discussed how PLC designs have changed to meet automation and control challenges in recent years.
- In Part 3, van der Wal discusses the evolution of PLCs and provides several key examples of their potential applications.
In the ever-evolving field of industrial automation, programmable logic controllers (PLCs) have been a mainstay, adapting to the changing needs of various automation applications. Known for their robustness and versatility, PLCs remain a preferred choice for machine control, motion control, and even certain process control applications. However, as the demands of modern automation grow increasingly complex, it’s essential to understand where PLCs fit best in today’s industrial landscape.
In a November 9 webcast, “PLC series: PLC hardware speed, I/O, communications, redundancy,” David Ubert, senior automation specialist at Black and Veatch, and Eelco van der Wal, managing director at PLCopen, discussed scenarios where PLCs are most effective, how their designs have changed to meet contemporary automation challenges, and what key criteria end-users should pay attention to when selecting PLCs for specific applications.
The transcript of their presentation has been provided with minor edits and adaptations.
Introduction to evolving PLC technologies
Eelco van der Wal: An excellent example of PLC hardware evolution can be seen in the progression from the production line of the original T Ford, which represented early automation, to the sophisticated, robot-coordinated automotive factories of today.
The evolution from operational to information technology in PLCs
Dave mentioned that PLCs are now over 50 years old, marking a significant shift from operational technologies (OT) to information technology (IT). Initially, PLCs focused purely on logic programming. Over time, motion control was integrated, expanding the domain knowledge beyond simple logic. This integration of motion with logic in the same development environment and controller represents a significant advancement in PLC technology.
Safety and communication in modern PLCs
Another crucial aspect is safety, particularly for operating personnel. This includes light curtains, emergency stops, and other safety measures around machines and production lines. Safety represents a domain distinctly different from both logic and motion, requiring specialized knowledge and considerations.
Communication capabilities have also been added to PLC systems. Contrary to the isolated systems mentioned by Dave, modern PLCs need to be interconnected, allowing access to information, program updates, and data extraction. Communication introduces another layer of complexity distinct from logic.
The critical role of security in PLCs
With the advent of communication capabilities, security becomes paramount. It’s essential to verify the identity of the communicating entities, especially considering modern cyber threats, such as those seen in recent conflicts where controlling power stations remotely can be as impactful as physical attacks. Security is now at the forefront of PLC system design, underpinning safety.
New challenges in security and digitalization
Addressing security in PLCs introduces the need for certificates, a novel concept in traditional operation technology. Certificates ensure the authenticity of communication between controllers. Unlike the simplicity of connecting a thermocouple to an input/output module, communicating with another controller requires validation of its security certificate, which is not indefinitely valid, introducing a new domain for classical operation technology programmers.
Finally, digitalization and simulation represent the latest frontier in PLC technology. Machines and systems are now designed and tested in digital environments, where both the hardware components and the software programs, including their timings, are simulated and optimized.
The concept of digital twins in PLC systems
The concept we now refer to as a “digital twin” represents a significant advancement in PLC technology. A digital twin is essentially a digital replica of what is being created in reality – it’s the virtual counterpart of a physical machine. This virtual representation behaves in the same way as the actual machine, bridging the gap between operational technology (OT) and information technology (IT). We have transitioned from a world dominated by OT to one increasingly influenced by IT. Previously, the world of PLCs was isolated, with unique programming languages and tools. However, the advent of new software and technological advancements in other areas has necessitated our adaptation. Despite being a multi-billion dollar industry, PLC technology is relatively small in scope, compelling us to integrate tools developed externally.
Modern PLC applications in five industries
Modern PLCs find applications in a diverse range of machine controls. This spans across various sectors:
-
Food packaging and production: Automated production lines are extensively used in food packaging, contributing to higher cleanliness standards compared to manual packing. Automated lines help reduce contamination risks, like hair or blood, thus extending the shelf life of food products.
-
Pharmaceutical production: The recent COVID-19 pandemic highlighted the need for rapid, large-scale vaccine production, a feat unachievable without automation. Speed and efficiency in pharmaceutical production lines are critical, and automation plays a vital role in meeting these demands.
-
Robotics and manufacturing: In manufacturing, robots vary from simple two-axis systems, used for tasks like moving heavy items, to sophisticated six-axis robots and AGVs (Automatic Guided Vehicles). These robots offer increased flexibility and are often incorporated into complex systems with up to 100 axes, controlled by multiple interconnected PLCs.
-
Automotive manufacturing: Car manufacturers utilize hundreds of PLCs for various processes, including transporting car bodies, handling robots, welding, and assembling parts like seats and dashboards. The integration of cobots (collaborative robots) working alongside humans is becoming increasingly common.
-
Infrastructure and environmental management: In the Netherlands, for example, most bridges, as well as water distribution and wastewater treatment systems, are controlled by PLCs. These applications highlight the extensive use of PLCs in infrastructure management and environmental protection.
Challenges in maintaining and updating PLC systems
With the widespread use of PLCs in these industries, new challenges arise in system maintenance and updates. For instance, updating hundreds of PLCs during a short break, like a coffee break, necessitates a completely different approach than traditional methods. This highlights the need for efficient, large-scale update and maintenance protocols in modern PLC systems.