As processing devices advance more rapidly, they are unlocking new features for legacy industrial I/O field devices.
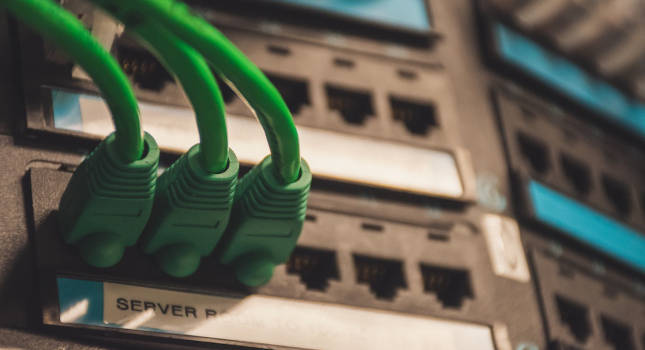
Industrial I/O insights
- Industrial I/O devices are central to the functioning of contemporary industrial automation systems, providing engineers with the capability to monitor and manage complex industrial equipment effectively.
- Their applications are extensive and include digital inputs/outputs such as proximity switches and motor start commands, as well as analog inputs/outputs like pump speed commands and level transducers.
Industrial input/output (I/O) devices play a critical role in modern industrial automation systems, enabling control engineers and operators to monitor and manage highly complex industrial equipment with confidence.
The possible use-cases for industrial I/O are broad – here are just a few real-world examples to paint a clearer picture:
-
Digital inputs, such as proximity switches can detect the presence of a part on a production line, momentary start/stop pushbuttons, maintained switches to change operating modes, and high/low float switches.
-
Digital outputs, such as motor start commands, inverter start commands, oven start commands, and valve open/close commands.
-
Analog inputs, such as level transducers, pump speed feedback signals, oven temperature readings, and flow meters.
-
Analog outputs, such as pump speed commands, conveyor speed commands, and analog valve position commands.
These examples however are really only the tip of the iceberg when it comes to industrial I/O applications, as there are nearly countless other I/O field devices available for industrial monitoring and control.
It is important to make a clear distinction between field devices and processing devices. Using a simple momentary pushbutton as an example, the physical pushbutton would be considered the field device, and the processing device would be something such as a programmable logic controller (PLC) or edge controller that the pushbutton is wired to in order to read and process the status of the pushbutton.
Major I/O device advances
While there have been some major advances in field devices, processing devices have advanced at a much faster rate and have unlocked new features for legacy field devices. For example, an existing water lift station system may consist of dozens of field devices such as sensors, pushbuttons, and more, all connected to a decades-old PLC which lacks built-in support for some modern, in-demand features such as message queuing telemetry transport (MQTT). It is a lightweight, publish-subscribe, machine to machine network protocol for message queue/message queuing service – which users are quickly gravitating towards to bring their data into the cloud and unlock the benefits of industrial Internet of Things (IIoT) connectivity. In this scenario, the processing device could be upgraded from the old PLC to a cutting-edge industrial edge controller with the appropriate I/O cards to connect the existing field devices. Additionally, a cellular sled could be installed in the edge controller to provide internet access.
From there the edge controller could be configured as needed using software. Crimson 3.2 includes Crimson Control (available in the Group 4 software package) from Red Lion, for example, gives users access to IEC 61131 programming languages such as Function Block, Ladder Diagram, and Structured Text. This functionality allows the DA70 to replace the PLC in this example. Additionally, the software has built-in support for several MQTT cloud connectors to bring all of the I/O and process data into the cloud.
With these features, the existing industrial I/O field devices in this example could remain in place while using an edge controller to unlock the power of MQTT cloud connectivity. Today it is easier than ever to upgrade existing legacy systems with cutting-edge features that make industrial I/O more readily available than ever.
– This originally appeared on Control Engineering Europe.