Accurately measuring levels in tanks and vessels can be challenging. Non-contacting radar transmitters designed for food and beverage applications are helping manufacturers improve production processes, according to a company with a Control Engineering Engineers’ Choice Award product.
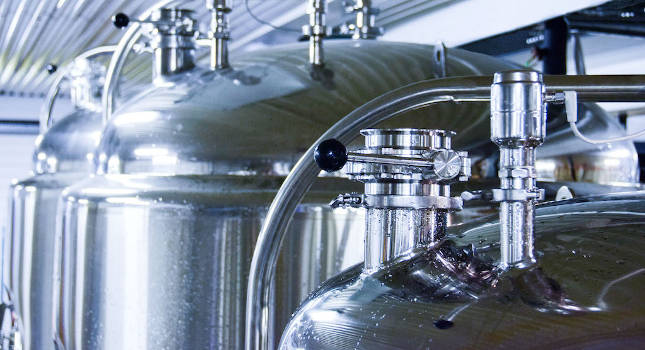
Learning Objectives
- Understand how non-contact level measurement sensors and transmitters help food safety.
- Learn about more accurate measurements with radar-based sensors and how compact designs of level transmitters fit in tight piping arrangements.
- Examine how software configuration tools ease integration of non-contacting radar transmitters for level measurements.
The ability to measure the level of materials accurately and reliably in storage tanks, mixing tanks and process vessels is an important element of food and beverage production. These measurements are needed for inventory management, overfill prevention and processes such as blending, batching and mixing of ingredients. Several level measurement technologies are available and used within the wider process industries, but food and beverage applications provide a unique set of challenges.
Accuracy and reliability are vital, while measurement devices must of course comply with the industry’s stringent hygiene and food safety standards. The chosen technology must be able to cope with the specific process conditions of the application and devices must be suitable for installation within the existing equipment layout. Finally, integration into an existing or new automation system needs to be very simple to encourage adoption, especially if the technology is new to the plant.
Level measurement technologies
There are many different technologies that can be used to provide either continuous level measurement or point-level detection in food and beverage plants. These include load cells, capacitance switches, vibrating fork switches, differential pressure transmitters, ultrasonic transmitters and guided-wave radar (GWR) transmitters. However, non-contacting radar transmitters best meet the industry’s need for measurement accuracy while also providing key advantages.
Radar transmitters are very accurate with measurement unaffected by process conditions such as density, viscosity, conductivity, coating, corrosiveness, vapors, and changing pressure and temperature. As these devices are top-mounted, this immediately reduces the risk of product loss through leakage. In addition, unlike many of the other technologies, they are not in contact with the material being measured, which eliminates the possibility of contamination and helps reduce maintenance and maintain long-term reliability.
Non-contacting radar transmitters are deployed widely within the oil, gas and petrochemical industry, where reliability and precise level measurement in safety-critical applications are essential. Despite the significant advantages they offer, their use within food and beverage production has been limited because the industry considers them too large and expensive. The lack of a full range of hygienic approvals and process connections also has been prohibitive.
However, current non-contacting radar transmitters have been designed to provide highly accurate continuous level measurement specifically in food and beverage applications. These devices match the industry’s strict hygienic requirements and offer manufacturers a compact and cost-effective solution that provides a range of significant benefits.
Non-contact sensors help food safety
Food safety is paramount and every effort must be made to reduce the risk of contamination during production processes. A key part of that is the use of clean-in-place (CIP) and steam-in-place (SIP) processes for tanks and vessels. The latest non-contacting radar transmitters have been designed to not only withstand these arduous processes, but also maximize the effectiveness of the cleaning process and ensure continued measurement performance.
To achieve this, the transmitters have a hygienic antenna that is flush with the process connection, insensitive to condensation and build-up and featuring a drip-off sealing that ensures the removal of process residue during CIP and SIP. The devices also have a broad range of hygienic process connections that fit most common tank connections and sizes.
In addition to internal tank cleaning processes, many manufacturers wash down the outside of tanks with foaming chemicals and/or high pressure and high temperature water. The design of the latest non-contacting radar transmitters enables them to cope with high pressure and high temperature washdowns, while an IP69-rated sealed polished stainless-steel housing with minimal crevices ensures water and sediments drain from the device’s body, reducing the risk of bacteria growth. A full range of hygienic approvals enables the transmitters to meet global food safety standards.
More accurate measurements with radar-based sensors
A key advantage of radar over other technologies is its measurement accuracy. Radar transmitters measure liquid level by sending out microwave signals that bounce off the product surface and return to the sensor. The transmitter measures the time delay between the transmitted and received echo signal and the on-board microprocessor calculates the distance to the liquid surface. However, the latest non-contacting radar transmitters use fast sweep technology to provide a continuous echo against the material surface. This allows them to collect up to 40 times more information compared to legacy radar devices. This makes them ideal for applications involving small fast filling tanks while delivering accurate and reliable measurements. This is especially important when trying to establish if there is liquid remaining in a vessel that might otherwise be lost during the cleaning process.
A crucial challenge for food and beverage manufacturers is maximizing tank utilization so they can keep up with customer demand and increase revenue. Current non-contacting radar transmitters have been designed to perform accurate level measurements right to the top of the tank, with no dead zone, thereby enabling optimized tank usage whilst also ensuring the vessel is not overfilled.
Compact design of level transmitters fit in tight piping arrangements
Whereas oil and gas applications are unlikely to place demands on level measurement technology in terms of the space it takes up, the same does not apply in the food and beverage industry. Skids are often designed to be compact and have very tight piping arrangements, which makes it difficult for large or bulky devices to be installed.
The latest radar transmitters can meet this challenge because they are very compact. This is achieved by providing 80 gigahertz (GHz) frequency modulated continuous wave (FMCW) technology on one electronic chip, rather than having a separate circuit board. Single-chip technology also enables exceptional radar beam focusing, which together with smart algorithms enables greater measurement accuracy, even when tanks contain objects such as agitators.
Simple integration with software configuration tools
Reducing design complexity is an important aim for food and beverage manufacturers, and instrumentation needs to be easy to integrate with any automation system. Current radar devices provide conventional 4 to 20 mA, switch outputs and digital high-speed IO-Link communication. To further reduce complexity and ensure trouble-free operation, software configuration tools allow the devices to be connected and configured online or offline, with graphic interfaces decreasing commissioning time, optimizing device replacement processes and digitally recording parameter settings.
Non-contacting radar transmitters for level measurement applications
By combining the performance and reliability of a non-contacting radar device, typically deployed in the oil and gas industry, with a compact hygienic design and simple integration, current non-contacting radar transmitters provide food and beverage manufacturers with the ideal solution for their demanding level measurement applications. Implementing these devices can result in increased food safety and product quality, minimized product loss and increased production capability through optimized tank utilization and inventory management.
Felix Johansson is solutions engineer for Emerson’s radar level business. Mark T. Hoske, content manager, Control Engineering, CFE Media and Technology, [email protected].
KEYWORDS: Level measurement advice, Engineers’ Choice Awards
CONSIDER THIS
How are you using non-contact level measurements to improve operations?