Single-pair Ethernet (SPE) enables a simultaneous power supply of terminal devices via power over data line (PODL) over a single pair of copper wires, opening up new possibilities and fields of application for industrial Ethernet and the Industrial Internet of Things (IIoT).
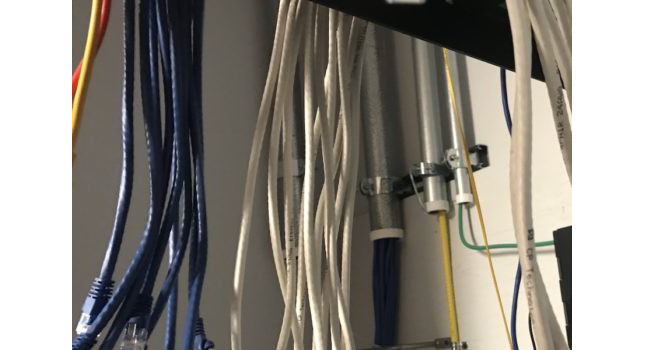
Ethernet networks have traditionally prevailed from the company level via the operation and process level right up to the control level. The field level, however has mostly been connected via various bus systems due to the huge number of devices here, which has made the use of Ethernet cost-prohibitive.
This looks set to change as single-pair Ethernet (SPE) technology starts to take shape. In addition to data transmission via Ethernet, SPE also enables a simultaneous power supply of terminal devices via power over data line (PODL) over a single pair of copper wires, opening up new possibilities and fields of application for industrial Ethernet.
Recently, the international standard for Single Pair Ethernet (SPE) interfaces in industrial applications has been published within IEC 63171-6 which is incorporated into current SPE cabling standards of the ISO/IEC 11801-x series of standards for structured cabling. The implementation of SPE in the ISO/IEC 11801 documents is important because it describes the cabling channels with all necessary parameters – length, number of connections, bandwidth and the complete set of transmission parameters – in relation to the environment and can therefore be metrologically verified after installation. To find out more, Control Engineering Europe posed the following questions to members SPE Industrial Partner Network members:
Q: How and where is SPE expected to offer an alternative to existing industrial ethernet infrastructure in process and manufacturing plants and what impact do you expect it to have on the growth of the Industrial Internet of Things (IIoT)?
Jonas Diekmann, technical editor at Harting (JD): SPE will not replace the existing 8-wire multi-pair Ethernet cabling, which is ubiquitous in office and control equipment today. Instead, it has the potential to replace the jumble of fieldbus protocols employed at field level with one communication standard – Ethernet.
Trends such as IIoT bring with them predictive maintenance capabilities, which requires a large number of additional sensors to provide the data. Ethernet is the right standard and SPE is the right infrastructure to implement this idea in a space, financial and resource-saving manner. In short, SPE will provide the infrastructure for the IIoT.
Nigel Broad, UK director PMM Cable PMM Connectivity at Lutze (NB): While Ethernet, and especially Industrial Ethernet, has become more accepted for time-critical applications in industrial automation, alternative technologies are often still used to connect sensors and actuators. This means that there is a break between the Ethernet-based control level and the field level. In most cases, fieldbus systems or even analogue systems are still used here and this is where SPE comes into play and convinces with a variety of advantages. For example, the transition from the control level based on Ethernet with 4-paired cables, to the field level does not require any change in the content of the Ethernet packets. A simple media converter makes the conversion to SPE possible. This transparency – from the point of view of communication protocols and other software – makes it possible to configure a sensor via a laptop, regardless of its geographical location. Even complex sensors with update options can be integrated with little effort, and error diagnosis is also easier and more accurate.
Uwe Widman, technology & standardization at Belden Deutschland (UW): Existing Ethernet network infrastructures enable point-to-point communication with shielded twisted pair Ethernet cables up to 100m with bandwidths of typically 100 MHz (CAT 5) or 500 MHz (CAT 6A). The limited transmission distances and the high costs of Ethernet ports and components have been a barrier to adoption of Ethernet at field level.
SPE, as part of IEEE 802.3cg with bandwidths of 20 MHz and transmission distances of up to 1,000m and the ability to transmit data and power according to IEEE 802.3bu (PODL) now enables Ethernet access for the process industry in hazardous areas. SPE, in combination with PODL, has the ability to replace existing fieldbus infrastructures in the process industry. Additionally, IEEE 802.3cg makes it possible to implement cost-effective point-to-point connections up to 25m with unshielded twisted pair cables.
The process industry is, however, only one area where SPE can replace existing fieldbus systems – with a transmission rate of 10 Mb/sec, it can replace many fieldbus systems with data rates 9.6kb/sec to 10 Mb/sec, with distances exceeding 100m.
The IO-Link standard – which is widely used in the automation market – is currently limited to data rates of 230 Kb/sec and a transmission distance of 20m. However, it is now being evaluated in a concept study for SPE integration to bring the advantages of both technologies into IO-Link specification.
With the ongoing digitalization in industry, a variety of new application fields are appearing. New field devices, with higher functionality, simpler fast connection technologies for cables & connectors; progress in miniaturization, a cost-effective component infrastructure; and in combination with the TSN technology, SPE fulfills the requirements to create successful IIoT model in the process and automation sectors.
Q: What are the barriers to adoption of the technology in existing plants, which will often have a great deal of legacy systems
JD: In the future field-level equipment will need to be equipped with new interfaces, magnetics and chips. Since this process of renewal can be carried out gradually, there is no requirement to change everything at once. Devices and subscribers can be gradually converted and connected to Ethernet. Implementation will most likely, therefore, take place within the usual renewal processes of structures.
If you consider that fieldbus systems still account for a market share of about 40% today and that these could be replaced by SPE in the future, the potential becomes clear. It will still take up to two years before a significant number of applications go into production. Good market penetration is expected to take place within about five years and it could be 10 years before SPE becomes the dominant standard at the field level.
NB: The introduction of SPE technology in the industrial field together with TSN gives the industrial sector an opportunity to make a leap forward in both precision and accuracy. The biggest obstacle will be that components will have to be changed and the entire active and usually also passive infrastructure will need to be adapted. The true benefits will not become accessible until network products, hardware and software are all available. However, it should not be too long before these barriers are removed.
UW: With the publication of the IEEE 802.3 SPE standards and the future IEC standards for generic cabling, cables and connectors, SPE has set the basis for success. There will be a fast breakthrough into existing legacy systems with the relevant fieldbus systems if the interfaces between the new SPE technology and existing ‘legacy technologies’ are made available. Vital elements for success include miniaturization; weight reduction and simple connection technologies.
Q: What advice can you offer control engineers considering converting their field level to SPE?
JD: For the first time, SPE – as a new physical layer – offers the possibility of bringing Ethernet to every sensor at the field level in a space- and cost-efficient manner. Using the TCP/IP protocol, all participants can be identified and the TSN protocol, which can also be used with SPE, allows sensors to deliver data in real-time. It is important than engineers start to plan now for this change.
NB: The present technology break between the control and field level makes the operation and administration of such a network unnecessarily complicated. A complete review of the field level is the place to start. The advanced physical layer (APL) working group considers the 10 Base-T1L standard to be ideally suited for extending Profinet or Ethernet/IP to the field level. These are common networks within the automation and control arena. Due to the physical requirements for the cables, Ethernet was previously unsuitable for use in hazardous areas. The use of SPE technology, in conjunction with single-pair cables will enable a transmission rate of 10 Mbit/sec with segment lengths of up to 1,000m. As SPE allows PODL this means that it is possible to power sensors from the network.
UW: The network system philosophy is important. Consider everything from the field level, through the edge to the cloud. Belden considers SPE as a further element of the Ethernet infrastructure. SPE technology will be further developed by IEEE 802.3 and international standardization organizations and user organizations will include this technology in their specifications. With APL technology, a first IEEE 802.3 SPE standard for the process level is already available. Do consider SPE in a future network infrastructure and utilize it in brownfield expansions where interfaces to legacy technology are available.
This article originally appeared on Control Engineering Europe’s website. Edited by Keagan Gay, digital media & production coordinator, CFE Media, [email protected]