System integrator, Vertech, provided automation for AriZona Beverage Co.’s new greenfield facility
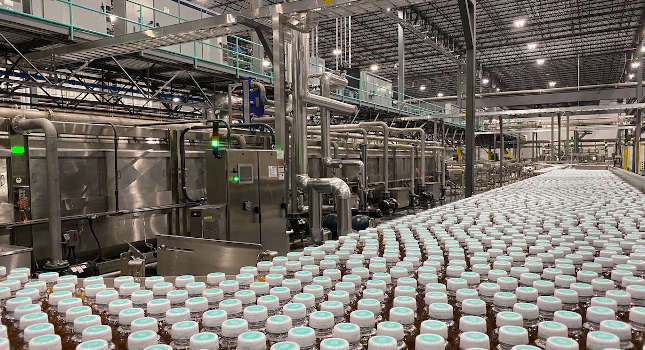
In November 2019, AriZona Beverage Co., the company behind the AriZona Iced Tea brand, opened its newest manufacturing facility in New Jersey (see Figure 1). This modern facility consumes 621,000 square-feet, houses five bottle and can production lines, a plastic bottling plant, syrup concentrate batch system, a reverse osmosis (RO) water generation system, warehouse space and amenities distinctly “AriZona.”
As an integrator for Inductive Automation and Sepasoft, Vertech quickly became the front-runner to provide a world class automation solution for this new facility. AriZona had stipulated Inductive Automation’s Ignition platform to be used for all supervisory control and data acquisition (SCADA) functionality and to use Sepasoft modules for manufacturing execution system (MES) functionality as it related to syrup concentrate batching and tracking of bottle and can production across five packaging lines.
Project details
Vertech’s scope of delivery crossed multiple areas: SAP integration with MES for production scheduling, SAP integration for tracking real-time batch and finished goods production reporting, ISA-88 batch control and associated programmable logic controller (PLC) programming, overall equipment effectiveness (OEE) and downtime tracking, control panel design build and overall system commissioning. Vertech provided a solution that stretched across all layers of the automation stack (see Figure 2).
Figure 3: Vertech’s electrical team designed the required panels, which required more than 2,000 control points. The panels were built in Vertech’s panel shop. Courtesy: Vertech[/caption]
In addition, three motor control panels also were provided for integration of Rockwell Automation PowerFlex 525 drives to handle control for agitation motors and liquid transfer pumps.
At the core, a Rockwell Automation ControlLogix programmable automation controller (PAC) was used for all batch and process control functions. ISA-88 concepts were to be followed. Within the ControlLogix, PAC Phase Manager was used for equipment phase control. A custom batch solution was created within Ignition to allow flexible batch recipes to be created at run time. This ensures AriZona can leverage the flexibility of the batch process equipment to produce its entire portfolio of beverage products. AriZona can create new recipes and change the procedural execution of those recipes without having to modify any portion of the control system.
After batches are produced, the batch control system interfaces with other PLC systems at each packaging line for product transfer to inline blending systems and onto packaging. The PLC communicates with 16 other PLCs to carefully coordinate not only batch production but to also control the transfer of syrup concentrate to production lines and cleaning of all batch equipment, process tanks and line equipment.
Project challenges
The biggest challenge of the project was creating a batch control system inspired by ISA-88 principles within Ignition. Traditionally, industrial batching is often handled by dedicated batch software, which runs in parallel to a traditional SCADA system. Dedicated software has benefits, however, depending on the industry not all the software features are fully implemented. In the case of food and beverage, most often the core requirement is to have the ability to build dynamic and flexible procedures for creating a product using the process equipment at hand with a relatively straight-forward process.
Figure 5: Allowing Ignition to be configured for active directory authentication, single sign on and integration of email allows Ignition to automatically send email notifications on shift, weekly and monthly basis for overall plant production reporting. Courtesy: Vertech[/caption]
It was established early on that integration with traditional corporate IT services were essential to further enhance the value of Ignition to AriZona. Allowing Ignition to be configured for active directory authentication, single sign on and integration of email allows Ignition to automatically send email notifications on shift, weekly and monthly basis for overall plant production reporting (see Figure 5).
Using the Ignition Perspective module, a mobile application is accessible through a secure corporate wireless network. This application shows production status of each of the packaging lines as well as syrup tank product information and bulk sugar inventory with a quick glance of a user’s smartphone or tablet. An additional Perspective application displays real-time production information on TV dashboards located throughout the plant.
To collect data related to OEE, downtime and overall production tracking, each of the production line control PLCs have been be integrated into Ignition to allow monitoring of line machine center status and line production counts. At each production line, the filler is considered the “key” cell for identifying line downtime or uptime. The Sepasoft OEE module monitors the key cell to determine production modes and states, in combination of production counts obtained at the filler and line control PLC, the OEE modules calculates OEE metrics (see Figure 6).
Figure 7: Ignition MES automatically reports the batch and packaging work order production schedule to SAP where raw material inventory ordering and delivery is handled. Raw materials for packaging such as trays, wraps, lids and raw materials required for batching are delivered in a just-in-time fashion. Courtesy: Vertech[/caption]
Vertech has provided a solid foundation in Industry 4.0. Ignition will become the central data hub for all plant manufacturing data, granting the facility unprecedented access to data across all systems through the MES layer. Future integration opportunities include utility monitoring, building information systems, warehouse management, maintenance management systems and additional production lines and batch tanks.
To the untrained eye, it appeared the goal of this project was provide an automation solution that enabled the process engineering equipment to ensure the facility was capable of fulfilling the market demand of AriZona Iced tea. While it is extremely satisfying to witness a greenfield sight come alive as bottles and cans begin to travel down the production lines on their way to be palletized shipped, the real challenge is sustainability. AriZona’s core brand strategy is to keep the 23-ounce can product at a 99-cent price point. Vertech recognized sustainability was just as important as production.
Transforming production data into consumable information and analytics will help AriZona adhere to its mission statement to bring customers great-tasting products, using top-quality ingredients, presented in a uniquely designed packaging, skillfully produced and made affordable to everyone.
Vertech is a certified member of the Control System Integrators Association (CSIA).
This article appeared in the Global System Integrator Report.