Machines, particularly PLCs and PACs, have a key role to play in enabling smart manufacturing and more interconnected factories.
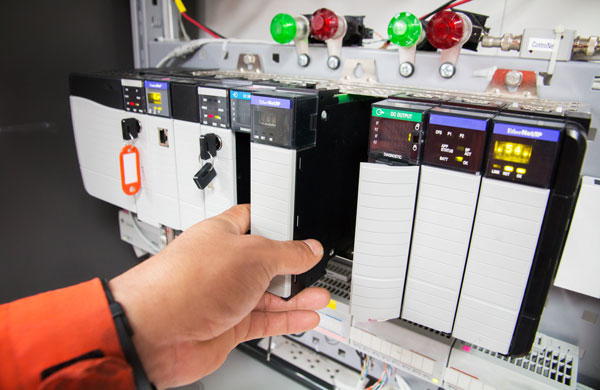
In the rapidly evolving landscape of smart manufacturing, control units such as programmable logic controllers (PLCs) remain essential components in automated operations, helping to streamline processes, enhance productivity and optimize plant performance.
“As we progress further into the digital age, controllers continue to push the boundaries of what is possible, paving the way for ever smarter, more interconnected factories,” said Daniel Sperlich, strategic product manager – controllers EMEA at Mitsubishi Electric. “PLCs and other controllers represent a key enabling technology for smart manufacturing, helping end users set up increasingly more intelligent, interconnected and effective factories. While these devices have been crunching data since their launch, they are now capable of handling unprecedentedly large volumes of information.”
They can process and share data from a variety of sources to enable industrial Internet of Things (IIoT) applications. As well as common operational technology (OT) data traffic from drives and other automation devices, machine controllers can now connect to cameras and information technology (IT) systems by accommodating TCP/IP messages.
“Taking this a step further, when coupled with AI-based analytics tools, it is possible to feed the data generated by the controller to advanced algorithms that can produce valuable insights,” Sperlich said.
One key activity across industry, where these capabilities can be extremely beneficial to users, revolving around maintenance tasks. Sperlich said, “Control solutions that can integrate with cameras strategically located on production lines can help streamline troubleshooting and root cause analysis if issues arise. They can offer valuable, easily accessible visuals about what is happening or has occurred on the line. When combined with control data and AI-based analytics, these solutions also simplify the identification and resolution of errors, minimizing downtime and costs.”
Sperlich went on to point out that it is possible to easily pinpoint where errors may have occurred as well as correct them before issues are propagated through the entire production line. Such solutions enable effective remote maintenance, reducing downtime and associated costs, especially if plants are located in areas with limited accessibility.
In praise of programmable automation controllers (PACs)
As manufacturing plants continue to digitally transform in order to make operational improvements, there is a growing demand for plant control technology that meets the demands of a modern system architecture. According to Steve Ward, director, application engineering EMEA at Emerson, this need can be met through the adoption of programmable automation controllers (PACs).
He said: “Although programmable logic controllers (PLCs) are still utilized to handle simple processes and smaller applications with a few I/O points, PACs are now typically deployed for more complex processes, especially those that require advanced control algorithms and data processing capabilities.” PACs are designed for handling large amounts of data and performing complex data analysis, storing data in databases, and generating reports that support continuous improvement programmes.
Typically, these modular, open, scalable and interoperable PAC solutions feature enhanced networking capabilities with plug and play connectivity to make it easy to add machines and devices to an existing automation architecture. Modern controllers support a variety of protocols – such as PROFINET and OPC-UA – which enables secure communication with multiple devices and systems, including databases, servers and other controllers.
“To drive productivity improvements, production uptime is essential,” Ward said. “To support this, control systems can be configured with redundant controllers and network connections, ensuring that the process continues to operate even if a component fails. Extremely fast switchover to redundant hot standby controllers ensures high availability control solutions.
“At the heart of digital transformation is the use of existing and new data to provide actionable insights. Traditionally, data analytics has involved collecting massive amounts of data for analysis centrally, which required costly infrastructure, expensive planning and special skills. Modern controllers overcome this by enabling data to be analyzed at the machine level allowing fast action to be taken. Edge controllers combine real-time deterministic control capabilities with data processing, logging and analytics all in device. Multicore hypervized processing power enables near real-time analytics to be performed locally in parallel with the control processes. Using this functionality, it is possible to implement a data-driven feedback loop – without interfering with the deterministic control.”
– This originally appeared on Control Engineering Europe.