A plant’s supervisory control and data acquistion (SCADA) system could benefit from mobile broadband on 5G with cost reductions for enhanced capabilities being applied to plant asset management.
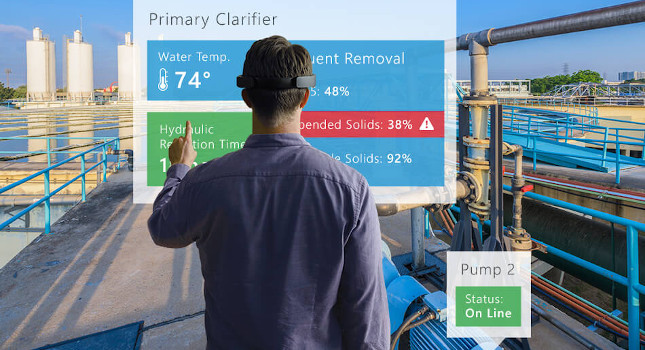
The utilities sector was an early adopter of cellular networks, coming to rely on GSM as an enabler for monitoring of remote assets. In water applications in particular, this allowed operators housed in a single control room to monitor assets such as pumping stations often kilometers apart, using a central supervisory control and data acquisition (SCADA) platform.
The wider adoption of cellular technologies has resulted in features such as the ability to send alarms, error warnings and general status updates to individuals using text messages, while 3G and 4G cellular networks and web clients have made machine-to-machine communications, and monitoring using mobile devices possible as part of the Industrial Internet of Things (IIoT).
Just as these network advances have been an enabler for easier wireless communications between automation systems and devices, so they have also been a barrier due to functional limitations. However, 5G however looks set to remove this barrier, supporting higher speed, higher bandwidth communications with improved reliability and very low latency.
This paves the way for many use cases in plant control and process automation, and it could have a disruptive impact on the wireless connectivity market. There is the potential for 5G to become a de facto standard for wireless communications throughout the plant – from field level up to the cloud and all the layers in between. Support for industrial Ethernet will accelerate its uptake in plant automation, enabling simple integration with a complementary wired infrastructure.
In the context of a plant’s SCADA system, superior mobile broadband on 5G could bring substantial cost reductions for enhanced capabilities being applied to plant asset management. Removing the need for hundreds of meters of wired IO, 5G expands the potential for decentralized control and wireless sensor networks. Further, the reliable, high speed and low latency communications promised by 5G could open up the possibility for wireless solutions to be used for closed loop control in process automation.
As the first practical mobile communication technology for automation, 5G offers performance as high as 20 gigabits per second (up to ten times faster than current 4G networks. It offers significant potential as an enabling wireless technology for applications that generate and rely upon big data.
As we journey towards an era of Industry 4.0, 5G will inevitably come to complement SCADA as a key building block for the smart factories of the future. It could provide a route for allowing devices and processes to be rendered intelligent, with SCADA providing the mechanism for aggregating this data to form the interface between the information technology (IT) and operations technology (OT) worlds within a plant. SCADA could then be exploited to a much fuller potential, freeing up communications from the limitations of both wired and existing wireless infrastructures.
There are, however, also limitations to 5G. Some plants are electromagnetically noisy and so mobile signal strength will be an issue, likewise critical automation systems will always use the most reliable control method and have redundancy built-in. Where this is not the case, we may well see many traditional wired Ethernet or Wi-Fi applications migrate to cellular technologies based on 5G.
5G will bring significant new possibilities to plant control and process automation, not simply providing the wireless communications technology of choice in a SCADA context but conceivably even removing the need for or reliance upon wired communications in many applications. With its high speed, low latency and promised ultra-high reliability, from a plant control perspective and with an eye on Industry 4.0, the roll-out of 5G cannot come soon enough.
Carl Nash is technical director at Products4Automation. This article originally appeared on the Control Engineering Europe website. Edited by Chris Vavra, associate editor, Control Engineering, CFE Media and technology, [email protected].