In smaller facilities up to a handful of people might be in charge of the process control system. Larger companies may be made up of multiple facilities, requiring specific system integration needs for optimal business operation.
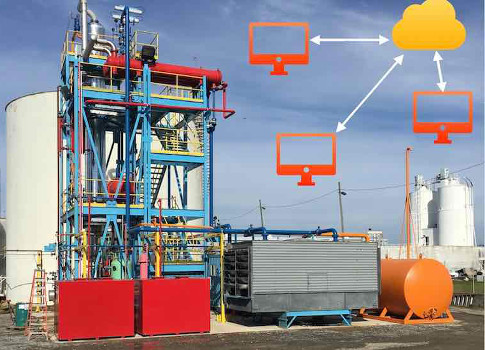
As companies grow, or seek to become wholly connected enterprises, system integrations can become costly. Determining the right level of integration for a company is key to maintaining an ideal cost to value ratio when planning integration initiatives.
Today’s manufacturing landscape consists of many types of organizations. From smaller companies with a single facility, to co-manufacturing facilities producing goods for a wide variety of customers, to a worldwide enterprise with dozens of facilities, all companies have one thing in common. They need to get the information from the plant floor to the people who need it to make the best decisions for their company. Whether that means understanding production capacity before taking on a new customer or prioritizing production to stay agile in an ever-changing consumer landscape, the overall concepts of system integration remain the same.
Information integration
Integration between business systems and process control systems can be a powerful tool for a manufacturing company. No matter how large the company, data begins its transformation into information at the process level. Real-time data is stored in process historians, quality control data is integrated for statistical process control, energy metrics are calculated and integrated with billing, and production scheduling interfaces with warehousing and operations to prioritize what gets made and when. A larger company with a corporate level system will integrate this plant level data into its systems to give corporate staff the information they need to make decisions.
Solutions at every scale
While the scale of integrated systems will vary widely between a regional manufacturing company and a worldwide one, the concepts remain the same across the board.
Think of a global company with facilities on multiple continents as a collection of smaller plants. Each facility has its own systems, process historians, shipping and receiving, quality control, and customer service systems just like any other single facility. The difference is that each plant becomes a source of information that is fed into the corporate level systems. This is no different than the system architecture at the single plant level; it has one or more additional layers of integration.
In the same way that the amount of information is pruned as it goes up the organizational chart, corporate-level staff typically doesn’t need to see finely detailed information about each plant to do their jobs. Their key performance indicators (KPIs) will be based on data at the plant level rather than the equipment level, and they may never need to drill down into a plant to see specific information on a piece of equipment, although the option can be presented if necessary.
The flow of information is just as important at any size company. Defining how data is turned into information is a key point to discuss with the system integrators and staff who will be putting together requirements and specifications to implement the project.
The cost of Industrie 4.0 and beyond
The key to integrated systems is an understanding of the costs and benefits achieved by investing in integration.
One way to keep costs manageable is to simplify the amount of data that is sent up the organizational chart. As an extreme example, sending all of the real-time plant data from the PLC to the CEO’s desk would require a lot of unnecessary effort and likely not provide much if any value to the CEO. Instead, this data should be turned into information in the form of KPI’s and reports as it moves up the chain of command. The KPI’s and reports at the corporate level will look different than what the plant manager sees and require less raw data to be sent from the plant to the corporate system.
The best way to understand the cost versus value of any integration is to first sit down with the person who will be using the new information and find out what he needs from the system to perform his job. This is in contrast to building a person a system based on assumptions and then re-working it to remove unnecessary data that is cluttering his workflow. In most cases, the information he requests takes much less work to generate than it would take to provide access to all of the available data in the system.
Reducing integration complexity
As companies grow and more systems are integrated, the overall complexity will grow. By spending time and resources up front, this complexity can be reduced by giving people only the information they need at first and growing the system with them as they become more familiar with its capabilities. The best approach is to start small and grow rather than give someone a system with an overwhelming amount of data up front. When people are overwhelmed they will resist the change, no matter the benefits the system may provide.
Alex Marcy, P.E., is the owner and president of Corso Systems, a system integration firm based in Chicago, Ill. Corso Systems is a CFE Media content partner. Edited by Chris Vavra, production editor, Control Engineering, [email protected].
MORE ADVICE
Key concepts
- Determining the right integration level is key for companies looking to maintain an ideal cost to value ratio when planning integration initiatives.
- Defining how data is turned into information is an important topic to discuss with the system integrators and staff.
- Spending time and resources up front can reduce any potential confusion system integrators and users might have at first.
Consider this
What other methods can be used to reduce costs and system complexity?
ONLINE extra
See related stories from Marcy linked below.