Latest remote I/O combines IIoT communication with even more processing power than traditional intelligent I/O
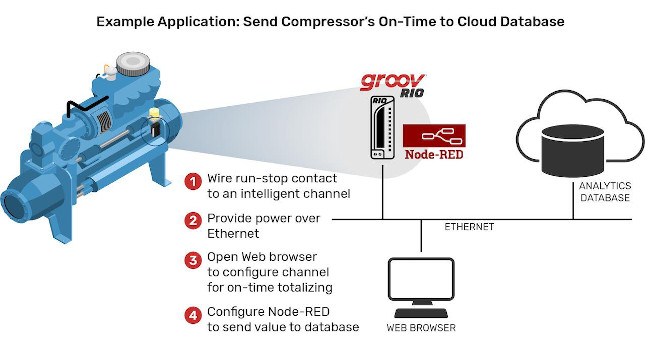
When intelligent input/output (I/O) systems first appeared, they were an alternative to the prevailing options at the time, including 1) low-cost I/O for discrete control applications, often used with programmable logic controllers (PLCs), and 2) more expensive analog I/O for continuous control, typically part of large-scale distributed control systems (DCS).
These early I/O systems were limited to converting raw electrical signals into digital values. The burden of processing, filtering and shaping these signals to create clean, usable data for process control and visualization rested completely on the controller.
The “intelligent” moniker given to new I/O systems pertains to their embedded computing power. Rather than rely on the controller, they can perform operations for signal processing and PID control internally. Computing power reduced use of custom programming to perform common tasks, like latching, counting, and thermocouple linearization, relieving the burden on the controller (and programmer).
Intelligent I/O also paved the way for other control options, like distributed control, as well as hybrid control systems that addressed the needs of both discrete and continuous control functions for large-scale applications. Since then, I/O systems continued to evolve, now with the motive of addressing Industry 4.0 needs.
Changing needs in the field
Early intelligent I/O systems provided key distinguishing benefits:
- With extra processing power in a modular format, it was easier to add advanced functionality to small and low-cost control systems.
- By distributing processing and control throughout the system, intelligent I/O created options for redundancy and fault-tolerance.
- With I/O modules handling signal processing and PID loops locally, logic scan times decreased, making systems more responsive.
- In short, the focus of these I/O options was to create affordable, resilient, and responsive automation systems.
However, the push towards a digital transformation introduces goals that begin with reliable automation as a given and reach beyond operations technology (OT) to connect with the information technology (IT) domain in meaningful ways.
These new goals include:
- The convergence of IT and OT systems, opening data silos
- Ubiquitous connectivity and communication between field devices and software
- Machine-to-machine communication for predictive analysis and autonomous control and
- Other productivity stepping stones, like mobile and augmented visualization
So generally, beyond reliability, control systems are being asked to deliver more data and more connectivity. However, some obstacles lie in the way to achieving these goals.
With most industrial data still residing in unintegrated sensors and switches and a large installed base of standalone machinery across many brownfield sites, the industry has a long way to go to achieve ubiquitous connectivity. To complicate things further, the traditional options for integration —RTUs, PLCs, OPC and SCADA servers. These simply don’t scale to the level needed to integrate everything, lacking the communication and security protocols needed to do so safely and incurring additional costs per I/O point with every level of middleware required.
I/O to the rescue
Next to field devices themselves, I/O systems are the closest point to highly prized field data. They are also a required integration point for hardwired equipment and its untapped data. Intelligent I/O systems are targeting features that allow engineers, technicians, and developers to tackle data integration efficiently and securely.
These systems are appearing in the market under a variety of names, sometimes simply as “smart remote I/O,” but the term “edge I/O gateway” is also common and helps to distinguish the unique functionality they offer compared to previous generations. The term is derived from the concept of edge computing, a distributed architecture that relies on lightweight local computing resources working in partnership with heavyweight cloud services or data centers to improve data processing and local performance. Edge computing is finding applicability within Industrial Internet of Things (IIoT) applications because of the need to support higher volumes of data for business intelligence and analytics systems.
Industrial edge I/O modules and systems provide even more computing power than traditional intelligent I/O and apply it to data processing and IT connectivity, in addition to enhancing basic control functions. Rather than dealing only with I/O signal processing, these devices can become part of the network infrastructure, connecting field devices directly to maintenance systems or business applications using native protocols for communication and security.
Defining industrial edge I/O
Naturally, systems from various vendors differ in their specific form factors and I/O options, but they share a common feature set that addresses the specific goals and obstacles of connected control systems.
More processing power: Distributed computing power is the defining attribute of intelligent I/O. Edge I/O takes it to the next level with faster CPUs and more RAM to support complex signal processing and embedded applications. Some models run their own real-time operating systems on chipsets like those powering modern mobile devices.
More connectivity options: Edge I/O connects the real world to the digital world with a selection of communication interfaces that bridge both domains. Typically, these devices offer a mix of I/O types, analog and discrete inputs and outputs as well as serial options. Importantly, though, edge I/O complements these with multiple options for transmitting information to automation and business networks: wired Ethernet, WiFi, or cellular.
Support for OT and IT protocols: As opposed to previous I/O systems that focused only on automation connectivity, edge I/O provides for native communication with IT systems, as well. It pairs options such as Modbus/TCP, EtherNet/IP, PROFINET, and OPC UA with REST, MQTT with Sparkplug B, SNMP, VPN, and other protocols that support a completely new communication architecture for I/O. With the combination of appropriate media and protocols, edge I/O devices can translate raw I/O signals into both OT- and IT-compatible data.
Embedded security: Critically, IT compatibility introduces security options that have frequently been lacking in automation hardware. Features like user authentication, SSL/TLS data encryption, certificate management, and internal firewall configuration enable secure data transmission directly from the field or plant floor, even across public networks.
Embedded logic: Secure IT communication and embedded computing power make it possible for edge I/O systems to take on even more of the tasks typically given to a controller. In addition to traditional signal processing features like scaling, ramping, totalization, and output pulsing, edge I/O adds simple programming options such as Node-RED to store and filter data, combine data from different sources, and execute transactions with databases and web services.
What’s possible now?
What do these new I/O options do to move the industry closer to a digital transformation and how do they help to overcome the obstacles that stand in the way?
Meeting the bandwidth and computing demands of Big Data as well as the local requirements of embedded artificial intelligence and advanced visualization requires industrial automation specialists to consider a new, more scalable system architecture. Edge computing is already demonstrating its effectiveness in commercial applications, and it holds potential for industrial applications as well. Unfortunately, ripping out existing infrastructure is an expensive proposition. Automation engineers need options that can run in parallel with existing systems to achieve the same outcome.
Edge I/O enables additional computing and networking to be added piecemeal, in place of or in addition to, existing automation infrastructure, providing multiple paths for engineers to architect scalable communications. For example:
- Edge I/O can be used for lightweight integration by connecting I/O signals to data networks in parallel with legacy automation systems.
- Hardwired equipment can be retrofitted with basic sensors and edge I/O as a controller-less integration option that sends data directly to supervisory systems.
- Existing middleware such as PLCs and Windows PCs can be bypassed or removed by allowing edge I/O to handle data acquisition, preprocessing, and transport to higher-level systems.
- Since many edge I/O models are designed for hazardous locations, edge I/O also provides a more affordable path to remote condition monitoring of hard-to-reach equipment.
In combination with edge controllers, edge I/O makes available more design possibilities, particularly for integrating legacy automation devices. But it’s the controller-less potential of industrial edge I/O that allows for flexible deployment of intelligence and connectivity into the process. That kind of scalability, with security as a first principle, helps to make large-scale machine-to-machine communication feasible.
Gist of it
I/O systems continue to evolve in response to the changing needs of the automation industry. Edge I/O combines distributed intelligent I/O processing with IT-oriented communication, expanding the options for creating ubiquitous connectivity and overcoming obstacles to total integration. The critical differentiator between these systems and previous generations of intelligent I/O is their ability to interface with IT systems and software natively, allowing them to bypass traditional communication middleware and send data directly to its destination. The same capability allows these systems to share a larger scope of responsibility in automation tasks and to act independently of traditional automation controllers such as PLCs, PACs or IPCs.