Eight years after Industry 4.0 began, have you answered three flexible factory problems? Five Industry 4.0 trends help create flexible factories.
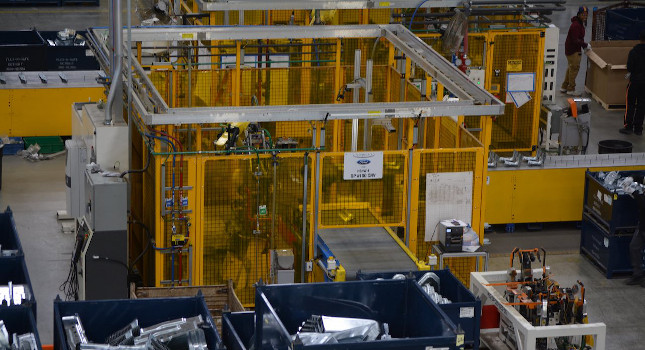
Learning Objectives
- Learn the five trends of Industry 4.0 to help form flexible factories.
- Answer three common flexible factory problems.
- Consider five Industry 4.0 trends that can help create flexible factories.
What will the future factory look like? Maybe there is no right or wrong, only more appropriate applications of technologies. [A Chinese saying about Shakespeare applies here: “There are a thousand Hamlets in a thousand people’s eyes.] Among all the answers, at least one common thing is that the future factory must be a flexible factory that can produce on demand and realize mass customization, which also is one of the main goals of Industry 4.0 proposed by Germany in 2013.
Now, nearly eight years have passed since Industry 4.0 was put forward. How about the development of Industry 4.0? And what trends have been presented? Is the “flexible” factory of the future already taking shape?
Industry 4.0 progress
Recently, Philipp Wallner, industry manager of industrial automation and machinery of MathWorks, was interviewed by Control Engineering China to discuss the latest progress and trends of Industry 4.0.
Philipp Wallner said that the future factory must be a flexible factory. One reason is the driving force of the market, the greater demand for personalized goods, which makes the factory change from large-scale production to large-scale customized production, that is, stronger demand for flexible production. In addition, the demand for independent production lines and the shortening the product iteration cycle also drive the factory to flexible production.
Three answers to flexible factory problems
The current technological development has made flexible factories possible. Wallner said three important production factors are needed to solve these complex problems:
- More powerful hardware and high-efficiency hardware can make these complex algorithms run in the field environment.
- The new design process and tools are sufficient to support the development, testing and deployment of complex software systems, or software systems including those artificial intelligence (AI) algorithms.
- More engineers with domain knowledge gradually master the technology of data analysis and AI. They integrate domain knowledge with new AI technology knowledge to make the factory flexible.
Five Industry 4.0 trends that help flexible factories
What will the flexible factory look like in the future? Wallner describes the five latest trends in industry 4.0.
Trend 1: The economic advantage of the AI project is increasingly prominent, and it will become a common application in future factories.
In the past, AI was mostly discussed in scientific research and academic fields, but AI has been applied in specific industrial scenarios, such as predictive maintenance, health monitoring, production optimization, vision-based quality inspection and other mainstream applications. Many companies, including MathWorks, have developed special AI tools and applications to design, train and deploy these AI algorithms, greatly reducing the burden of developers and designers, and achieving certain economic benefits.
Trend 2: Verification of machine development becomes digital. The increasing system complexity needs the support of digital design. This complexity often comes from our demand for flexible production, modular production, higher quality and precision, more data throughput, and shorter time to market and delivery cycle. In this way, digital modeling and simulation will handle the complexity. These models will run through the whole life cycle of design, delivery, operation and maintenance. The future factory will be built in the virtual environment first, and then in the physical environment.
Trend 3: Production workshop and office space will be more integrated. This has two meanings. First, standard industrial protocols, such as OPC UA and 5G enable all devices or automation components to be interconnected. These automation components also can be connected to the office scene to realize data interaction. In the past, complex software could only be run on the desktops of office, but now more of these complex software are deployed to the industrial scene, that is to say, the algorithm developed on the desktop computer can run on the industrial controller, so that there will a better integration between the desktop and the factory workshop.
Trend 4: Robotics will add flexibility to the factory. Today’s robots are usually programmed in a directed way to achieve a specific type of action and do not have the ability to make decisions on their own. This is incompatible with the flexible and modular production methods of the future. Therefore, autonomous robots with self-awareness and self-determination have emerged. This kind of robots have been successfully applied in material handling and sorting in factories.
Trend 5: Engineers with domain knowledge and new knowledge will be the most needed for future factories. AI and other new technologies make the future factory more intelligent, which also leads to the future factory engineers not only need to have professional knowledge, but also need to have new technical skills, such as mastering AI technology at the same time. Domain knowledge refers to the professional knowledge of the industry in which the engineer works, such as industry knowledge of equipment, processes, and procedures. New knowledge refers to knowledge of AI technology, cloud, software design, etc.
Faster AI integration into manufacturing
More plant engineers are adding skills such as software design and AI to their own skill sets, and engineering tools like MathWorks Matlab are providing engineers with automated tool apps that facilitate the development, testing, and deployment of AI algorithms. In this process, MathWorks Matlab provides a wealth of applet applications that can help engineers with specialized knowledge to quickly integrate new technologies, such as AI, into their practical work.
“The importance of digitalization has been demonstrated in 2020. With the transformation of the whole industrial field from large-scale production to customized flexible production, in 2021, we can see that digitalization transformation will become more important than ever, including the autonomy of production system, engineers, confirmation of system behavior through simulation, etc. The five trends shared today may just outline the rudiment of the future flexible factory. After all, the future has come!” Wallner said.
Digital transformation for manufacturers
“While the importance of digitalization has been demonstrated in 2020, in 2021 we can see digital transformation becoming more important, as the entire industrial sector transforms from mass production to customized and flexible production, including the autonomy of production systems and the confirmation of system behavior by engineers through simulation. And these five trends shared today may just outline the shape of the flexible factory of the future. After all, the future is already here!” Philipp Wallner said.
Stone Shi is executive editor-in-chief, Control Engineering China. Edited by Mark T. Hoske, content manager, Control Engineering, CFE Media and Technology, [email protected].
KEYWORDS: Industry 4.0, flexible factories, smart factories
CONSIDER THIS
Are you using Industry 4.0 to make factories more flexible?