RFID authentication devices on original equipment manufacturer (OEM) machinery ensure the proper users are taking permitted actions, providing performance benefits and improved safety. See five methods for security for industrial machinery.
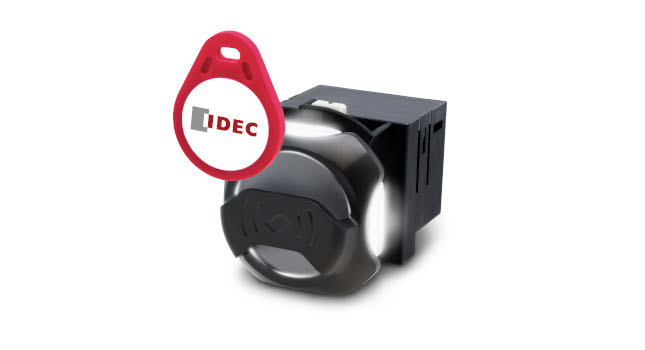
Learning Objectives
- Review methods for controlling and monitoring how machines operate and who controls them.Â
- See how radio frequency identification (RFID) is a passive tag system, but it can be used in many industries and applications.Â
- Learn how many RFID scanners are designed to work in harsh environmental conditions.Â
Automated equipment and machinery can incorporate many ways for users to monitor and control operation, such as with buttons, switches, and touchscreens. When original equipment manufacturers (OEMs) design and build machinery, they want to deliver easy-to-use functionality. However, they must balance this desire with the need to verify authorized users are at the controls and making acceptable selections.
Several authentication methods are possible, ranging in the security levels, user convenience, and features they provide. The simplest schemes may not offer enough protection, while the most complex are usually expensive and limiting.
Balanced solutions provide strong security and audit logs – and they are simple to implement, cost-effective to maintain, and easy for end users to work with, which is where radio-frequency identification (RFID) can play a role.
Authentication drivers for industrial machinery
It is possible to design machinery void of authentication methods, just as a car could be built with an on/off switch instead of an ignition key, or a house with no locks on its doors. Just as there are logical reasons to implement authentication solutions on cars and houses, there are motivations for doing so on industrial machinery, such as achieving operation restriction, traceability or both. Sometimes these motivations are driven by technical initiatives, but often they are mandated by regulatory requirements.
Operation restriction can sound negative, so operation permission may be a better term. OEMs and end user manufacturing companies incorporate authentication methods to ensure proper personnel are accessing machinery controls, but they don’t want to limit authorization to a binary yes or no. Authentication extends into defining groups of personnel and even individuals, with granular selection of what machinery information they can view and adjust.
Industrial machine traceability: Who did what, when, why
Some companies may add permissions to better ensure safe and proper equipment operation. In other cases, compliance with industry safety standards such as ISO16090 (for machine tools) or ISO10218-1 (for industrial robots) can lead to adopting authentication methods.
Traceability drivers involve gathering data, and manufacturers can use authentication to log which users operated a machine and the actions performed. This history may be used for informational purposes, which a company can analyze with the goal of improving performance. Or, the data trail may be stored to satisfy an industry requirement, such as FSSC22000 for food safety, which calls for traceability in the manufacturing process.
Five methods for security for industrial machinery
Several levels of security are possible, each with a range of benefits, disadvantages, and costs. The following methods are suitable for adapting into industrial machinery use, and are familiar to most consumers:
- Physical/mechanical keys
- Magnetic strip cards / swipe cards
- Passwords
- Biometrics
- RFID.
Physical keys are the oldest and most familiar of the authentication methods. They are simple and low cost, but easy to copy or lend. OEMs can implement a basic key switch into their machine, but it provides a binary or limited selection by any user who gains access to the key. Magnetic strip cards are an improved version of physical keys, which add some digital capability. However, they may not be convenient to carry and protect at industrial sites.
Common use of automation authentication
Modern digital devices used for industrial machine automation – including PCs, human-machine interfaces (HMIs), and mobile devices – have made passwords a common authentication method. Passwords can provide a limitless number of authentication levels per user, and are inexpensive to manage. Unfortunately, they can be forgotten or leaked, and can be difficult to use in many industrial settings where gloves are used or where a full keyboard or touchscreen may not be available.
Biometrics such as fingerprint and face scanners are common in consumer electronics and some commercial applications. Because they use personal and non-transmittable information, they are relatively secure, do not require operators to carry or remember anything and often cannot be duplicated or lent out. Unfortunately, biometric techniques are expensive to implement and manage. They don’t work well around machinery where gloves, helmets, masks and safety glasses may impede their function, either.
This brings up RFID, which occupies a sweet spot within industrial machinery authentication. RFID tags are familiar to most anyone who has used a parking lot or building access system. They are simple and relatively inexpensive to manage, and they are not easily duplicated. Although they are easy to lend, authentication is easy to modify because they are digitally managed. As a physical token, RFID tags and sensors are readily implemented for industrial applications.
Industrial-specific RFID devices
RFID is a preferred technology for many applications because the user’s tag is lightweight and does not require batteries. Reader devices, typically installed in a fixed location, generate a radio signal, causing a passive tag in range responds with a unique signal.
Consumer-grade RFID readers commonly found in commercial applications are often robust, but they usually are not built to withstand the temperature, vibration, and washdown/chemical environments associated with many machines. Most readers are designed to use rectangular cutouts, which are not convenient for many control panel designs.
However, some industrial-grade RFID readers are explicitly designed to fit industrial-friendly common control panel form factors, such as the 22-mm knockout hole (Figure 1). These devices also are available with IP67 ratings, meaning they are protected from dust, low-pressure water jets and even immersion situations sometimes found with industrial installations.
Industrial-rated RFID readers can take functionality a step further with LED multi-state and color indicator lights on the face, which can be activated to identify conditions such as standby, success or error. Some also can generate an audible signal to give users operational feedback.
RFID standards for cards, tags, fobs
Not all RFID tags are created equal, though. There are global RFID standards such as ISO14443A, ISO15693, and ISO18092 that apply to credit-card style configurations. While cards can be useful for industrial applications, there are also key fob styles which may be more suitable for carrying and using in production environments (Figure 2). Each tag carries a unique ID, which can be registered and associated with a user or a worker category.
Users may present tags at a reader for an intermittent acknowledgement, but sometimes an application requires the user to place the tag in constant contact with the reader during certain operations. In such a scenario, some industrial RFID readers include a mechanism to hold the tag.
RFID readers are intelligent devices. On the front end, they must interpret IDs from physical tags; on the back end, they must communicate with supervisory systems. This is usually performed with an industrial communication protocol such as Modbus TCP/IP (Figure 3), through which the reader can send complex tag IDs or simple authorization levels to the supervisory system, as well as receive commands to operate its light indicators and buzzer.
RFID applications and advanced RFID benefits
Industrial RFID readers are often integrated with the programmable logic controllers (PLCs) which control machinery such as machine tools and injection molding equipment. Consider one of these machines, which may have a few types of users:
- New or temporary staff
- Trained operators
- Technical leads
- Maintenance personnel.
When the new staff applies their RFID tags, machine operation can be limited to their skill level and operating authority. Trained operators may be able to access normal operation monitoring and control functions; technical leads are authorized to adjust advanced settings and make special production runs. Maintenance personnel may be restricted from running the system normally, but they may be allowed to jog motors and manually actuate devices.
RFID for access, machine procedures
For traceability, preceding users and their actions can be logged by the PLC and HMI. If the
RFID tag is at a machine access or safety cage location, it may be used in conjunction with unlock solenoids to allow the door to open for permitted personnel. Workers who inspect parts could confirm their review by scanning a tag. RFID tags can be incorporated into maintenance procedures to confirm personnel are working in the right areas, enhancing safety.
Engineering teams also can review logged user activity to analyze machine operation and determine more efficient ways to run. All actions can be stored and retrieved in a database environment to facilitate analytics and avoid inefficient paper logs.
Machines and equipment of all types can benefit from applying industrial-rated RFID readers and tags. The ability to manage and track user authority can be used to ensure basic access control and improve overall safety. More advanced functions, such as paperless traceability and database connectivity, can help OEMs and manufacturers cost-effectively meet regulatory requirements and optimize machine performance.
Linda Htay, product marketing specialist, IDEC Corporation. Edited by Chris Vavra, associate editor, Control Engineering, CFE Media and Technology, [email protected].
MORE ANSWERSÂ
Keywords:Â Radio frequency identification, RFID, original equipment manufacturer (OEM)
CONSIDER THISÂ
What do you use RFID systems for and what benefits have they provided?