Consider how to differentiate on how to select the right controller based on the operational needs of an application.
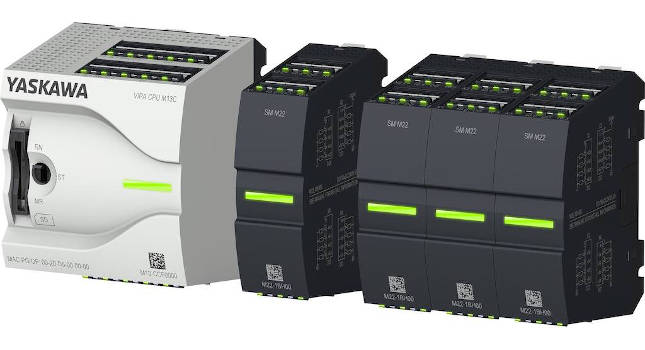
Control systems insights
- Programmable logic controllers (PLCs) offer cost-effective solutions for small-scale automation, while programable automation controllers (PACs) and industrial PCs (IPCs) provide advanced capabilities for complex, scalable operations.
- The choice between PLC, PAC, and IPC hinges on specific application needs, balancing cost, functionality, and long-term scalability.
At the heart of any automated setup is a controller. However, the choice among a programmable logic controller (PLC), process automation controller (PAC) and industrial PC (IPC) hinges on a series of decisions dictated by each individual application. The distinction between PLCs, PACs and industrial IPCs are often not clear-cut. A simplified explanation of each follows:
A PLC is considered the standard controller that is primarily designed for straightforward, robust control tasks. A PAC builds on the capabilities of a PLC, offering additional features and flexibility for more complex automation needs. Meanwhile, an IPC can run the same software as a PAC but includes all the capabilities of a personal computer, providing extensive processing power and connectivity options.
The next step is to understand the differences between the controller options.
-
PLCs: The first semiconductor-based PLC was created in the late 1960s to replace the inflexible hardwired relay systems of the time. Today, PLCs execute pre-programmed instructions, often in ladder logic or other structured languages. They monitor inputs from sensors, make logical decisions and control outputs. Their cost-effectiveness makes them a popular choice for small-scale projects. Advanced PLC models can handle remote input/output (I/O) and motion control, providing flexibility and functionality for complex automation tasks.
-
PACs: PACs use exception-based logic rather than ladder logic and this allows them to handle events or exceptions as they occur rather than following a sequential process. This means they can manage complex applications, such as advanced process control and motion control, by responding dynamically to real-time changes and conditions in the system. While PACs generally offer more advanced functionality and better performance, they are also more expensive than PLCs. However, as technology advances and R&D costs decrease, the distinction between the two types of controllers is likely to become less clear.
-
IPCs: An industrial PC is a rugged computer designed for industrial or harsh environments. It can support standard hardware interfaces, such as USB and PCI, ensuring easy integration with everyday peripherals. Engineers can also use frameworks like .NET and tools like Visual Studio to create customised applications and interfaces for specific industrial needs. IPCs can also manage tasks parallel to the operating system (OS), enabling critical real-time tasks, such as control processes or data acquisition, to operate independently and concurrently with the OS without being disrupted by changes or updates to the OS itself.
Which controller to choose?
PLCs are often chosen for use in standalone machine applications. Yet if motion control, safety integration or managing remote I/O are needed, a PAC may offer a better solution. For applications with advanced features or extensive software requirements, an IPC could be the appropriate solution.
However, if the total cost of ownership is a determining factor, investing more initially can save money over time by meeting future scalability needs and enabling data-driven process improvements.
Strategic upfront investments can, alternatively, yield substantial long-term savings and operational efficiencies, ensuring that businesses meet immediate growth needs and optimize processes through valuable data insight.
– This originally appeared on Control Engineering Europe.