Best project practices: How to achieve successful plant modernization and how to properly prepare for the project. See related article: Why modernize plant instrumentation, controls.
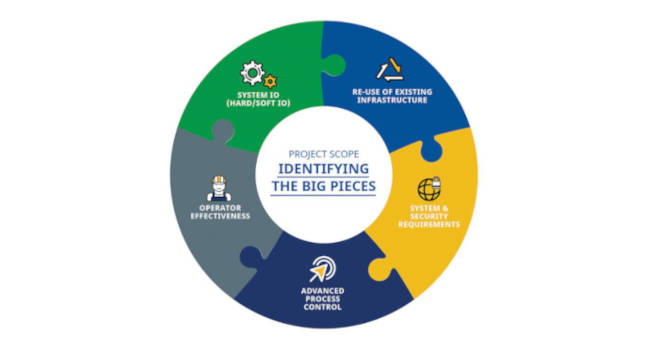
Learning Objectives
- Learn how to migrate from another brand of control system.
- Examine steps needed for a field instrumentation replacement of actuators, flowmeters, transmitters and other devices.
- Understand best practices, recommendations for use of a main automation contractor in a control system migration.
Instrumentation and Controls Modernization Insights
- Instrumentation and control system (I&CS) migration is complex, and many companies put it off years longer than they should. Migrations and upgrade can offer operational benefits beyond avoiding unplanned outages.
- Best practices include using new software and technologies that can help plan and execute the migration with less risk.
When planned well, a modernization instrumentation and control system (I&CS) project, even a large-scale system migration, can move from phase to phase on time and within budget, resulting in significant operational improvements. New tools make migration easier at less cost. Smart, software configurable I/O can be combined with standard, smart junction boxes to reduce documentation development by 80% and wiring design by 90%.
Need more convincing about migration and upgrade benefits? See related article: Why modernize plant instrumentation, controls.
Three instrumentation and control system tips: upgrades, migrations, replacements
The challenge of a plant modernization project compared to a brownfield or greenfield project is the sequence of construction must be very tightly controlled. In most cases, a “re-instrumentation” project must work within a limited shutdown window. Re-instrumentation can refer to replacement of field instruments, only, or the entire I&CS. Unlike a grassroots project with more flexibility, the re-instrumentation project also must deal with construction in an operating plant with all the hazards and limitations that entails.
The three typical modernization scenarios are the step-by-step upgrade, competitor system migration, and field instrumentation replacement.
1. Step-by-step upgrade of plant modernization
Unlike a full system upgrade, a step-by-step upgrade refers to a component base upgrade. For example, human-machine interface (HMI) stations are upgraded one by one without stopping controllers. Another example is to replace one controller which supervises a particular area without stopping other controllers. The greatest benefit of a step-by-step upgrade is to minimize production time loss and mitigate the risk of total production downtime. The upgrade schedule can be decided with the end-user’s production and maintenance schedules and budget in mind.
The key technology to achieving the above is the capability of existing control system legacy hardware and software to work together with new hardware and software and coexist. For example, in a distributed control system (DCS), upgraded human operator stations can access existing legacy controllers in a way to the latest controllers. Moreover, the ability to engineer and monitor online is maintained even if the field controllers and other HMI stations are operating with older versions of software. DCS suppliers refer to this as progressive compatibility.
When using the step-by-step upgrade method on systems that have eight or more physical workstations and servers, virtualizing these computer assets should be considered. Virtualization technology reduces the number of physical workstations and servers by hosting them on virtualization servers. Virtualization produces benefits such as a reduced hardware footprint, reduced energy costs, simplification of systems management, lower total cost of ownership, improved system availability, and rapid recovery from failure.
Today, most DCS hardware and associated components such as historians, asset management systems, and OPC servers can be upgraded into a virtualized environment.
For example, a DCS can be virtualized using high availability clusters that provide benefits such as redundancy with automatic failover, live migration capabilities for virtual machines, improved security, dedicated storage, and rapid disaster recovery.
2. Migrating from another brand of control system
Most DCS suppliers and a number of systems integrators have developed comprehensive system migration strategies for competitors’ systems. A consultative “value-added migration process” is a multiphase approach. In addition to the system migration process, it includes a feasibility study and site survey with a gap analysis, identifies bottlenecks, proposes practical countermeasures, and estimates the resulting profit improvement and return-on-investment (ROI) by using the replacement systems and solutions. System migration specialists are involved in all phases of this process.
For example, migration options are available to enable many legacy controllers and process interface units to be replaced by input/output (I/O) and controllers, using special marshalling panels and adapter cables that connect to the existing terminal panels of the legacy system.
System suppliers and integrators have also developed various database conversion tools which can transform software engineering information from third-party systems to the engineering database in the replacement system. Based on project experience, upwards of 20% of engineering costs can be saved by using conversion tools.
3. Field instrumentation replacement: Actuators, flowmeters, transmitters
Field instruments such as actuators, flowmeters, and transmitters represent a substantial share of I&CS investment costs. Today’s digital smart process automation systems and the connected field instruments can accomplish far more than legacy systems. Plant operators should take advantage of capabilities such as artificial intelligence, predictive maintenance, and integral diagnostics for the instruments and the process. A good investment, early on, will include the planning and design of a plant modernization to review the control schemes, revise and improve them, decide how to best implement and advance control techniques, and deploy the latest technologies.
Best practices, recommendations: Main automation contractors
Selecting a main automation contractor (MAC) is recommended for implementing re-instrumentation projects as the MAC ensures deployment of a team with the most appropriate and specialized skillsets. Using a knowledgeable team for the scope definition enables timely project delivery and reduces risks of trips or shutdowns.
The MAC is an automation partner capable of handling solutions and services from the front-end engineering design (FEED) stage, through detailed design and construction to startup and handover to operations.
In addition to the MAC concept are other project execution methodologies, which have been developed through the co-innovation of end-users and system suppliers. For example, agile project execution uses parallel program paths in place of the traditional, waterfall approach, in which the project was executed on one serial path.
Developing an instrumentation and control system architecture
Just like a preliminary field survey, a preliminary system architecture must be developed before proceeding with the project. This is an evergreen document with updates to the scope as it develops during the FEED study.
Accurate loop drawings and schematics could be difficult to locate and might be found in personal files maintained by staff technicians. They are keys to determining the history of changes to assure the new control system provides the same functionality as the system being replaced.
Through collaboration, the end-user and system supplier or integrator ensure the process and instrumentation drawing (P&IDs), measurement, and control schemes are fully understood to implement them in the DCS and safety instrumented system (SIS). For the latter, the required documentation includes the hazard and operability analysis (HAZOP) and layer of protection analysis (LOPA).
Any opportunities and risks should be identified during site survey and FEED studies. Improved control strategies provide for improved reliability and tighter control.
Safety instrumented systems have often been blended in with process control where safety and process logic coexist in the same processor (DCS or PLC). Today, the segregation of safety systems is a requirement per IEC 61511, where safety systems should be dedicated to safety-critical assets only. During upfront site survey activities, this will be a key component in identifying safety and process segregation and obsolescence of existing systems performing safety functions.
Scoping a re-instrumentation project
Re-instrumentation projects are marathons rather than sprints. The re-instrumentation team must maintain a clear vision of the project’s completion and measures of project success. Identifying the drivers and priorities for upgrades across the asset will help plan and scope the re-instrumentation project.
Plant re-instrumentation projects are notorious for scope changes. To ensure project success, there must be a well-established change management process that allows changes to be dealt with in an orderly fashion with the minimum possible impacts to funding and the schedule. In addition to design changes, the change management process must accommodate issues such as equipment failure, unplanned outages, or delays in the scheduled plant shutdowns.
Advances in system I/O technologies
Since the early days of digital control systems, process input/output (I/O) designs have undergone several major technological advances. Today, process and safety I/O can be smart and software configurable. Technologies such as fiber optic cabling and wireless communications can replace traditional, multi-conductor instrument cables, which are labor intensive.
Traditionally, control systems have used dedicated hardware modules, where a given module would consist of only one type of I/O such as analog inputs or discrete outputs. Today, modules are available with software configurable I/O on a per-point basis.
This kind of hardware design streamlines project execution by decoupling application engineering from field wiring and hardware installation. The hardware design works in conjunction with the aforementioned agile project execution methodology to provide major cost savings and project scheduling risk reductions. Using software configurable I/O at the edge could completely eliminate marshalling and reduce wiring by up to 80%.
Many companies now provide standardized “smart junction boxes,” which include various quantities of software configurable I/O. By deploying such standard components, project teams can eliminate the design, documentation and testing custom I/O panels require.
By using the smart junction box approach in conjunction with agile project execution, cabinet delivery, skid integration, and wiring termination can be done anytime during the project. Last-minute scope changes result in nearly zero project delays. Given the project decoupling enabled by agile project execution, a factory acceptance test (FAT) might now even be required.
Re-using existing wiring, termination, marshalling cabinets
An economical tactic is re-use as much of the existing wiring, terminations and marshalling cabinets as possible. As shown in Figure 5, I/O panels and wiring are among the longest-lived components in I&C systems. Nevertheless, project teams are urged to perform detailed assessments of the panels and wiring, especially if they have operated in corrosive environments, which would substantially reduce their lifecycles.
Many system suppliers and integrators have devised I/O adapter modules to interface the existing wiring to the new system. A trade-off assessment should compare the ROI for such custom hardware with that for the aforementioned smart junction boxes.
Automated commission expedites re-instrumentation projects
The new I/O technologies, smart junction boxes and project execution methodologies also can join together to automate the processes of verification, binding, configuration, testing and documentation for all field instrumentation. Compared to traditional methodologies, project teams can realize reductions of more than 95% in commissioning time in addition to 80% in drawings and 90% in wiring design work.
Collaborative project engineering tools for re-instrumentation
Finally, many system suppliers offer sophisticated, integrated project engineering tools, which allow project teams to collaborate on a global basis.
Software environments can facilitate project execution, system integration and site execution in a re-instrumentation or DCS migration project. The software brings certainty and confidence to all control system project phases as well as through start-up, operation, maintenance, expansion/upgrade, and extension stages of the plant lifecycle.
The tools generate a complete engineering environment, with a new database structure that feeds standardized and consistent information, maintains data integrity, eliminates inconsistencies between the design information and the actual system, manages change, and supports the system lifecycle.
In addition, the new tools facilitate the reuse of valuable engineering knowhow and eliminate duplication of work for subsequent projects.
I&CS re-instrumentation: More tools, less risk
Today, I&CS re-instrumentation project teams have numerous new technologies in terms of hardware, software and project management methodologies at their disposal. Smart, software configurable I/O can be combined with standard, smart junction boxes to reduce documentation development by 80% and wiring design by 90%. MAC and agile project execution methodologies, when used along with global engineering software tools, maintain project integrity, enable change management and reduce risks in terms of costs and scheduling.
Deployed in conjunction with sophisticated experience and skillsets, implementation of such technologies results in projects that are within budget, on schedule and produce significant operational improvements with excellent ROI in the near term and over the system lifecycle.
Kevin Finnan is advisor, market intelligence and strategy, Yokogawa. Edited by Mark T. Hoske, content manager, Control Engineering, CFE Media, [email protected].
KEYWORDS: Instrumentation and control system migration
CONSIDER THIS
What are you losing by continuing to delay an instrumentation and control system (I&CS) migration and upgrade?
ONLINE
See related articles linked below.