A system integrator deployed a Profinet industrial Ethernet network and programmable logic controllers (PLCs) for a food supplier looking to expand its facility. The integrator used the Ethernet network to improve communications and optimize operational efficiency for $125,000 in annual energy savings.
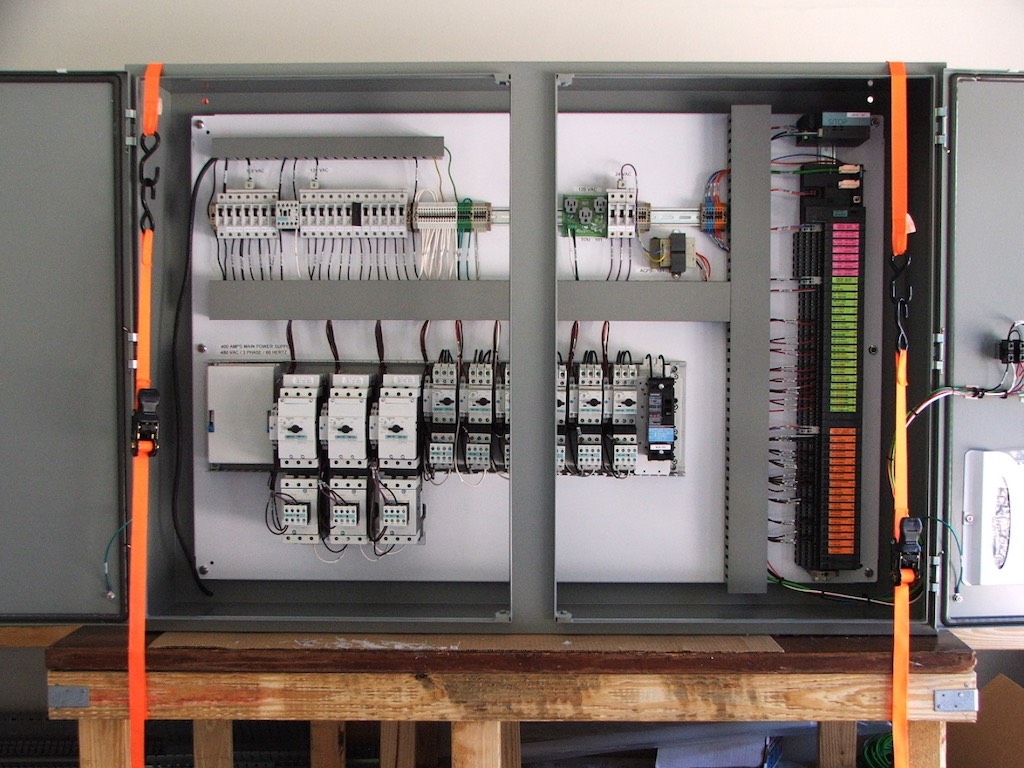
A national food supplier sought to expand its Boca Raton, Fla., distribution center to match growing business demand. This project required additional refrigeration equipment, which potentially meant higher energy bills. The company was looking to reduce energy costs and modernize its control system.
Global Controls Solutions LLC (GCS), a system integrator, wanted to achieve the company’s goal by using a Profinet industrial Ethernet network with help from programmable logic controllers (PLCs). This network transmits data from the refrigeration system to help the facility limit electrical charges in real time.
“At $0.02/kilowatt hour (kWh), energy wasn’t a big issue, but now at $ 0.145/kWh, it represents a significant operating burden,” said Vito Lampugnano, GCS president. “Calculations after the control system upgrade showed roughly 960 kW were load shed, which calculates into a savings of approximately $125,000 per year in utility charges.”
To achieve the savings, GCS implemented a two-phase approach: load shedding and load shifting.
Phase 1: Load shedding
During phase 1 operations, the facility’s electrical system is designed to shed “on” peak loads to take advantage of favorable electric rate schedules. Known as “peak shaving” or “load shedding,” it enables the facility to reduce equipment energy consumption during peak electric utility cost times. During daily load shedding, selected refrigeration equipment and parts of the electrical system are load shed (turned off).
Phase 2: Load shifting
During phase 2 operations, the facility’s energy supply shifts from the electric utility to the on-site generator. This “load shifting” refers to the ability to take the facility off the grid at peak times or at the request of the utility. The refrigeration plant is set up so the local electric utility can ask the facility to go offline during power outages, shortages, and weather-related incidents. During load shift operations, all electrical loads and refrigeration equipment are in full operation, powered by the generator.
A 2 MW generator was installed as part of the expansion along with a 4,000 A main switchgear that was interfaced with the existing switchgear. The generator and switchgear were networked to operate the facility during load shifting. A standby generator originally was used to operate the plant at nominal energy levels during normal power outages; the generator is designed as a full-time run unit. Fuel oil is sent automatically from large storage tanks to the day tanks used to feed the generator.
Distribution center, network upgrade
The distribution center is served by a central ammonia system using liquid recirculation for the low temperature evaporators and direct expansion for the medium and high-temperature evaporators. The two-stage, two-temperature system uses screw compressors for the low temperature and high temperature stages. The compressors employ thermo-syphon air coolers, and heat rejection is provided by evaporative condensers mounted on the roof.
“With the old ‘blue hose’ control system, there was no way to get the kind of data flow we needed to optimize operational efficiency,” Lampugnano said. “The distributed control system (DCS) now monitors all refrigeration plant pressures and temperatures, atmospheric dry and wet bulb temperatures, equipment operating times, plant operational set points, and system optimal set points.”
The DCS controls the switchgear, the generator, and the compressors via a Profinet industrial Ethernet backbone.
Pressure and temperature data are updated and recorded to identify operating trends. This makes it possible to adjust the refrigeration equipment to operate at the optimal design points. Being able to control and monitor an integrated system and analyze the trending data this integration enables are “key to optimizing processes, making them more reliable and reducing energy and other operating costs,” Lampugnano said.
The DCS is networked to PLCs that support Profinet and Profibus as standard protocols. Profibus is used for field-installed equipment and Profinet for communication between the control panels and as an interface with the compressor microprocessors. Modbus TCP was embedded into the PLC’s CPU as an add-on to communicate with the third-party microprocessors from the screw compressor supplier. These microprocessors have their own control panels.
Four main control panels for the refrigeration system were installed during the project to reduce sensor-wiring costs. Using an automation portal for recording and tagging components shortened programming and system startup time, according to Lampugnano, and reduced installation costs by over 25%.
Challenges: running during upgrade
“One of the biggest challenges of the project was to keep the existing refrigeration plant operating while installing and starting up the expanded system, especially since some code for the compressor microprocessors had to be corrected after integration,” Lampugnano said. “For similar projects in the future, we will recommend that the refrigeration system be fully integrated to control the compressors directly from the plant PLC rather than using the compressor microprocessors. Using a single PLC with a ‘hot swap backup’ greatly reduced hardware costs and developmental programming and made integration go more smoothly.”
Constantly changing compressor communication protocols make integration and data acquisition challenging in this type of project. “If compressor manufacturers all followed a Profinet or Profibus protocol, you could use standard code blocks to simplify communication,” he said.
Profinet network, annual savings
The national food supplier is equipped with a Profinet network for their Boca Raton distribution facility. GCS delivered an industrial Ethernet network suitable for energy management. The network upgrade is expected to translate into $125,000 of utility savings per year.
This installation did not use ProfiEnergy, a Profibus and Profinet International (PI) energy management application profile for Profinet. Future installations using ProfiEnergy would allow the food supplier to realize more savings. Devices using the profile could be programmed to go into an energy-saving sleep mode when not in use. The profile could help with extracting appropriate data from the network and with application of energy management algorithms.
Nelly Ayllon Lazo, technical marketing director, PI North America. Edited by Chris Vavra, production editor, Control Engineering, CFE Media, [email protected].
MORE ANSWERS
Keywords: Profinet, programmable logic controller, Ethernet
A system integrator deployed a Profinet industrial network to improve a food supplier’s operations.
The Profinet network helped streamline communications, implement more effective energy management, and optimize operational efficiency.
The network upgrade will provide the food supplier with $125,000 of utility savings per year.
Consider this
What benefits can a Profibus industrial Ethernet network provide to your company?