There are many ways industrial communications are supporting and simplifying the digital migration process.
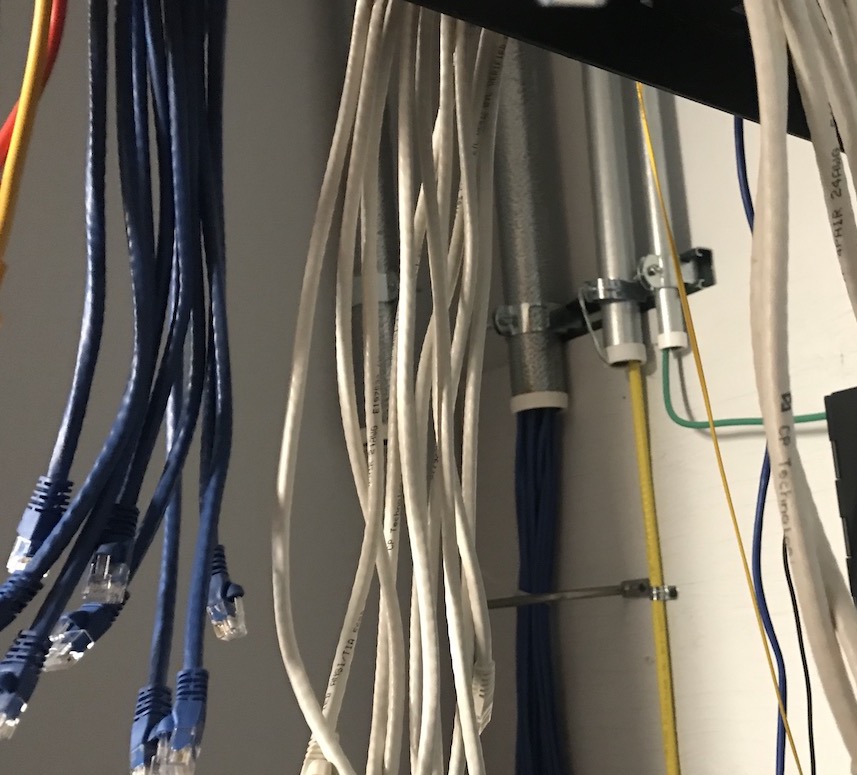
Embarking on a digitalization journey requires accurate digital models of physical assets and processes in order to predict outcomes and optimize operations in near real time. The successful migration from conventional automation frameworks to future-proofed cyber-physical systems requires state-of-the-art network technologies that connect the actual factory floor to its digital counterparts for closed-loop control.
There are a growing number of digital models that closely match the assets, machines, systems and processes used on manufacturing lines and these virtual replicas offer a tool for control and product lifecycle management (PLM) or to simulate events.
“In both cases, the digitalization process allows manufacturers to build transparency and manage plants in a more effective way, by getting meaningful information and actionable insight into their operations. Therefore, while digital models do not necessarily need to be connected to their physical counterparts to support industries, near-real-time feedback loops between these two worlds contribute to the creation of smart, responsive factories,” said John Browett, general manager of the CC-Link Partner Association (CLPA) Europe. “Indeed, only by allowing the virtual and physical worlds to communicate, is it possible to check if what is happening on the factory floor matches with what models are predicting. So, manufacturers need to consider implementing suitable industrial network technologies in their digital migration strategies towards Industry 4.0.”
The CLPA has supported industries in shifting from fieldbus to Ethernet – and now – to time-sensitive networking (TSN). Its most recent open technology, CC-Link IE TSN, is able to handle the large volume of data generated by sensors and models in cyber-physical systems in a timely manner by combining TSN technology with gigabit Ethernet. These two elements also offer a way to migrate existing, fully operational automation solutions to the future. “Ultimately, such networks let manufacturers prepare for the future while enabling them to run their current processes with maximum compatibility,” Browett said.
The intelligent enterprise
FDT technology has been at the forefront of digitization since it was first introduced in the 1990s. Its goal is to empower the intelligent enterprise with open and standardized integration independent of Fieldbus protocols and devices – driving widespread implementation of standards-based automation solutions for the process and manufacturing sectors.
Over the years, it has evolved from a single-user, desktop environment to a distributed, multi-user client/server approach with OPC Unified Architecture (UA) compatibility for enterprise-wide integration and asset management.
To help speed up the digitalization journey FDT technology helps enable industrial automation architectures to connect and communicate sensor to cloud to allow end-users to take advantage of decentralization, interoperability and integration, as well as providing a unified view of all data and functions across process, factory and hybrid control applications.
Development of the FDT IIoT Server (FITS) architecture (FDT 3.0) provides a flexible platform for deployment of various IIoT-based solutions. The emerging FITS solution empowers platform independence, comprehensive security, OPC UA integration, mobile device management, and a repository for device type managers (DTMs).
“Within the FITS architecture, the FDT Server is the heartbeat of the IIoT hub empowering the intelligent enterprise,” said Glenn Schulz, managing director at the FDT Group. “The server incorporates a web services portal allowing access from authenticated mobile devices or any major browser along with an OPC UA interface for IT/OT convergence and enterprise access. Rich control features ensure that any industrial communication protocol or vendor device can be seamlessly integrated as part of smart manufacturing practices.
“Developed with security at the core of its operating system-agnostic environment, the FDT Server is fully deployable in the cloud, on-premise, at the edge, or in a desktop environment. This makes the FITS solution a true information exchange platform and a key enabler for IIoT and Industry 4.0 applications that are essential to the digitization journey.”
According to Dr. Peter Wenzel, executive director of Profibus & Profinet International, Germany, the degree of implementation of Industry 4.0 is directly related to the two factors of consistent digitalization and standardized horizontal and vertical data and information exchange. This, he says, is based on robust, real-time communication technology for automation and a powerful, secure communications platform for production control and data exchange with the cloud and other IT services.
Distributed and synchronized production of parts of a property on several sites of the same or from different manufacturers, as well as flexible production of individualized products down to lot sizes of one, are essential features of the production in systems of generation Industry 4.0 and this requires the use of new production methods as well as a higher standardization.
“This means that communication will be even more important and dominant than it is today,” said Wenzel. “This is the driving force behind the new strategic orientation of the development of the technologies of Profibus & Profinet International (PI). In addition to targeted further development of PROFINET and IO-Link, in line with Industry 4.0, our innovations mainly concern the topics of semantics and information models, taking into account current security requirements and considering new business models that are currently emerging.”
The basis for Profinet is still the IEEE Ethernet standard. The further development of Ethernet in the IEEE 802.1 provides – behind TSN – real-time functions for all types of application of industrial automation, while maintaining a high degree of robustness with high utilization of the networks and the necessary determinism for time-critical applications. When integrating TSN into Profinet, PI selected parts of the portfolio of TSN’s features for optimal value and set scalable device capabilities tailored to their needs. “An integral part of the TSN strategy is that, additionally to real time (RT) and Isochronous real-time (IRT), Profinet can also work with TSN at the field level. The user view remains unchanged, and includes access to data, diagnostics and profiles such as Profisafe.”
Freeing the things
“Without the communication protocols that enables field sensors to communicate their data to the plant systems there would be no ‘Internet of Things.’ Instead, the things would simply be stranded islands of smart device information with no way to report back to the mothership about what’s happening in the process,” said Talon Petty, marketing & business development manager – Americas at FieldComm Group.
As users begin their digital transformation they are looking for ways to connect systems and assets never previously thought possible. Integration is paramount to allow companies to continue to meet reliability demands. It was for this reason that field device integration (FDI) was created with support from major automation vendors. All these companies have dedicated many engineering hours to making this a robust standard for process automation to ease integration work by users by unifying device drivers, configuration tools, diagnostics and documentation regardless of operating system with an independent and downloadable software package compatible with any FDI registered host system.
The FDI effort is also supported by The OPC Foundation, Profibus/Profinet International, FDT Group and ISA. On the user front, both NAMUR and The Open Group support FDI and have included it in their visions for the future frameworks that support digital transformation and Industry 4.0.
The FieldComm Group has also recently been part of a joint effort to develop a standardized information model for the process industries. Along with the OPC Foundation the vision for creating a protocol independent, process automation device information model (PA-DIM) specification to implement the requirements of the NAMUR Open Architecture (NOA) was introduced at the ARC Forum in 2018. Since then PI is now also participating in this vision.
When used alongside registered products that support FieldComm Group and PI’s joint FDI technology, the aim of PA-DIM is to simplify FDI to systems and clouds, as recommended by NAMUR and ZVEI, by standardizing on a single information model that supports the many field device protocols used in process automation including HART, Foundation Fieldbus, ISA100.11a, Profibus PA, Profinet and WirelessHART.”
“Using the OPC UA based PA-DIM with FDI products will enable end users to dramatically reduce time to market for advanced analytics, big-data, and enterprise cloud solutions that can often rely on information from thousands of geographically dispersed field devices that use multiple process automation protocols,” said Stefan Hoppe, president and executive director at OPC Foundation.
Suzanne Gill is editor, Control Engineering Europe. This article originally appeared on the Control Engineering Europe website. Edited by Chris Vavra, production editor, Control Engineering, CFE Media, [email protected].